Inspection – ERICO CADWELD for Rebar Splicing System User Manual
Page 11
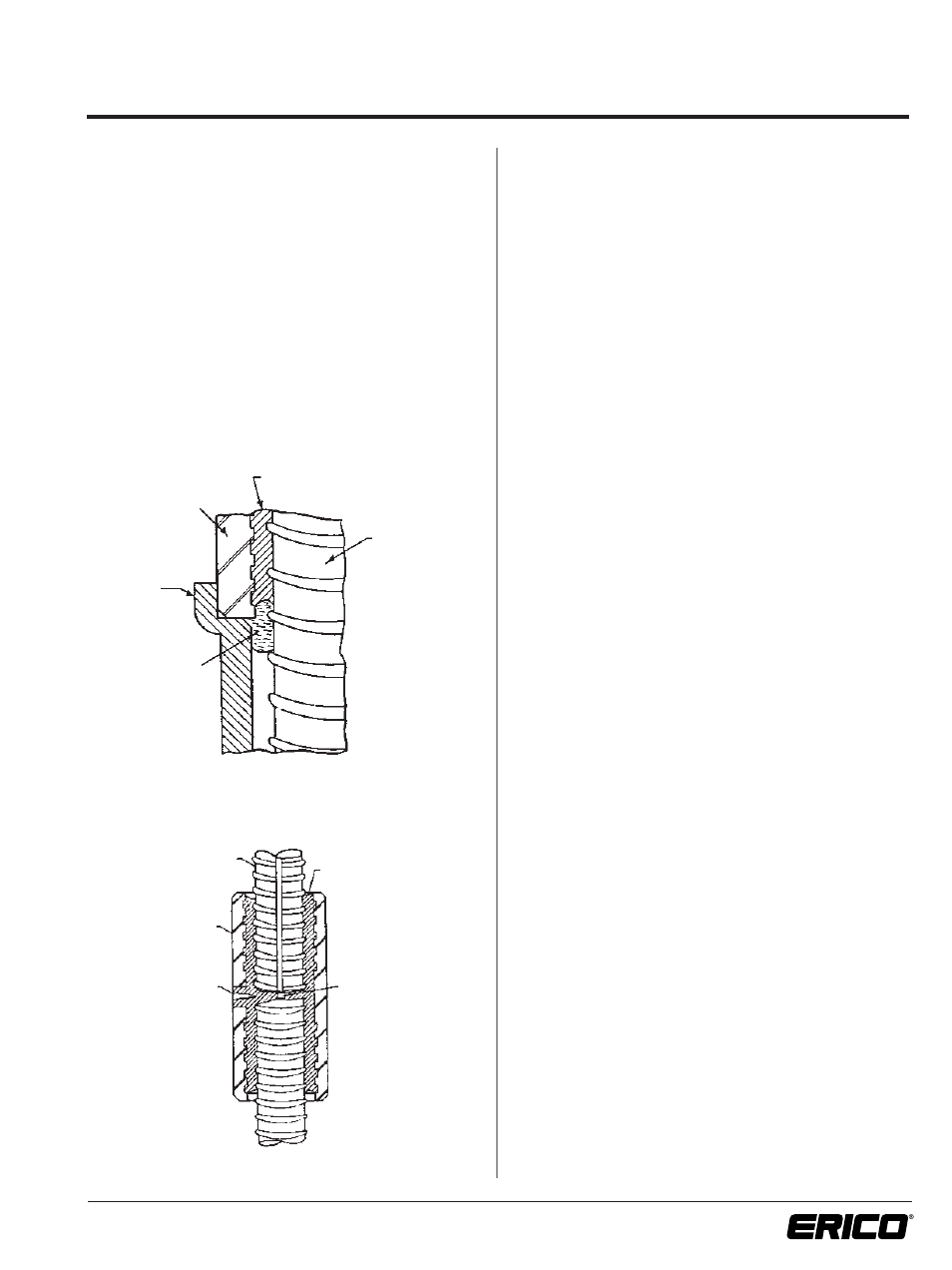
9
www.erico.com
Inspection
Inspection of a CADWELD
®
splice is a visual process.
Properly made splices will have filler metal visible at both
ends of the sleeve and at the Tap Hole.
Due to the gasket action of the packing, the filler metal will
not always flow to the very edge of the sleeve. This condi-
tion is most prominent in splices that require use of the
Horizontal Packing clamp which, when tightened, forces
the packing into the sleeve. The bottom of a vertical splice
will exhibit the same tendency due to the weight of the
equipment forcing the packing into the sleeve.
This indent caused by the packing will vary from 1/8-in.
(3 mm) to 1/4-in. (6 mm) in depth. Occasionally, where
a loose end of the packing has been forced into the sleeve,
the indent can vary from 3/8-in. (9.5 mm) to 1/2-in.
(12.7 mm) in depth. See Figures 1 and 2 for illustrations.
NOTES:
1. Do not manually force packing into sleeve. As described
above, the packing will be forced into the sleeve by
either the Horizontal Packing Clamp or by the weight of
the splicing equipment.
2. When making vertical splices, it is important that the
proper length packing be used at both the top and the
bottom of the sleeve. The longer bottom packing (2-1/2
wraps) is used to seal the bottom of the sleeve while the
shorter top packing (1-1/4 wraps) is loosely placed around
the top of the sleeve in order to permit expanding air to
escape and allow proper fill. Top packing should never
be forced inside the sleeve.
Due to the loose top packing, filler metal will often
flow above the top of the sleeve. This overflow is not
detrimental to the splice and should not be a cause for
rejection. In fact, an overflow is evidence of complete
fill. It is not necessary to remove filler metal flash
(collars) at the end(s) of the splice sleeves.
Adequate venting is essential for proper fill in all splice
positions. See page 8 for recommended venting
procedures on horizontal splices.
3. When the riser is removed, a shrinkage bubble may be
exposed in the Tap Hole area. This bubble should not
be distinguished from general porosity and shall not
constitute cause for rejection.
Eccentricity And Cocking Of Rebars
If the splice sleeve is filled with sound metal, eccentricity,
cocking and contact of rebars within the sleeve will have
no effect on splice performance and are not cause for
rejection. Standard splicing procedures for horizontal splices
require lifting of the splice sleeve until contact is made with
the bottom of the rebar.
Figure 1
Figure 2
Filler Metal
Reinforcing Bar
Splice Sleeve
End Alignment
Fitting
Packing
Note How It Bulges Into
Opening Between Splice
Sleeve And Reinforcing Bar
(See Note 1.)
Spacer
Reinforcing Bar
Splice Sleeve
Filler Metal
Shrinkage
Bubble
(See Note 3.)