Specifications, Preliminary information – Enerpac PL-Series User Manual
Page 2
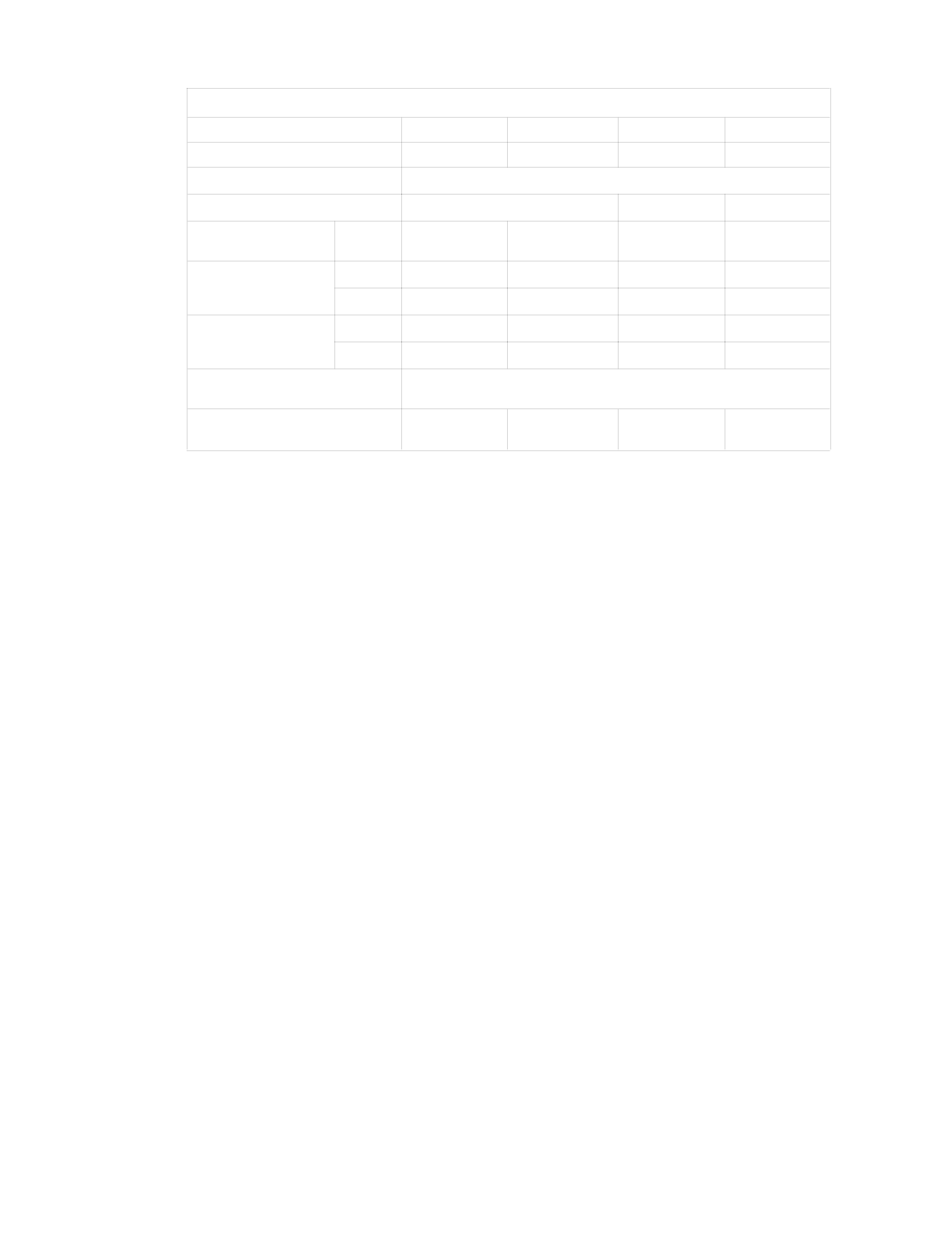
SPECIFICATIONS
Cylinder Specifications
-22 Series
-52 Series
-92 Series
-352 Series
Capacity [kN (lbs.)]
2,2 (500)
5,6 (1250)
9,0 (2000)
35,0 (7900)
Body Style
threaded body, lower flange, or upper flange mounting
Cylinder Type
single-acting and double-acting
double-acting
double-acting
Hydraulic Stroke
[mm (in.)]
clamp/
unclamp
16,7 (0.658)
23,0 (0.906)
22,0 (.867)
30,0 (1.182)
Effective Area
[cm
2
(in
2
)]
clamp
0,75 (0.116)
1,79 (0.278)
3,13 (0.485)
12,42 (1.925)
unclamp
1,54 (0.238)
3,80 (0.589)
8, 04 (1.246)
23,76 (3.683)
Oil Capacity
[cm
3
(in
3
)]
clamp
1,25 (0.076)
4,12 (0.251)
6,88 (0.420)
37,20 (2.269)
unclamp
2,57 (0.157)
8,74 (0.533)
17,69 (1.079)
71,28 (4.348)
Max. Pressure
[bar (psi)]
350 bar (5000 psi)
Max. Flow at 350 bar (5000 psi)
[cm
3
/min (in.
3
/min)]
393 (24)
820 (50)
122 (2000)
7867 (480)
PRELIMINARY INFORMATION
IMPORTANT: Failure to read and follow these instructions may lead to
system malfunction or product failure, and could invalidate your warranty.
(1) High flow rates can lead to excessive cylinder speed which can cause cylinder damage.
Hydraulic pressure and cylinder speed must be adjusted to match the particular
cylinder. The push/pull force also varies with the system pressure. Refer to the
operating specifications above.
(2) Flow controls with return checks may be required to reduce pull cylinder speed to the
recommended rate. The return checks help minimize back pressure that could lead to
an unclamp malfunction on single-acting systems.
(3) When using single-acting pull cylinders, limit the return flow back pressure to
3,45 bar (50 psi) maximum. Large diameter tubing (10 mm O.D. or larger) and flow
controls with free flow return checks help minimize back pressure. Consult Enerpac for
proper system design.
2