Electrical connections, Gas piping installation – Aerovent IM-500 User Manual
Page 6
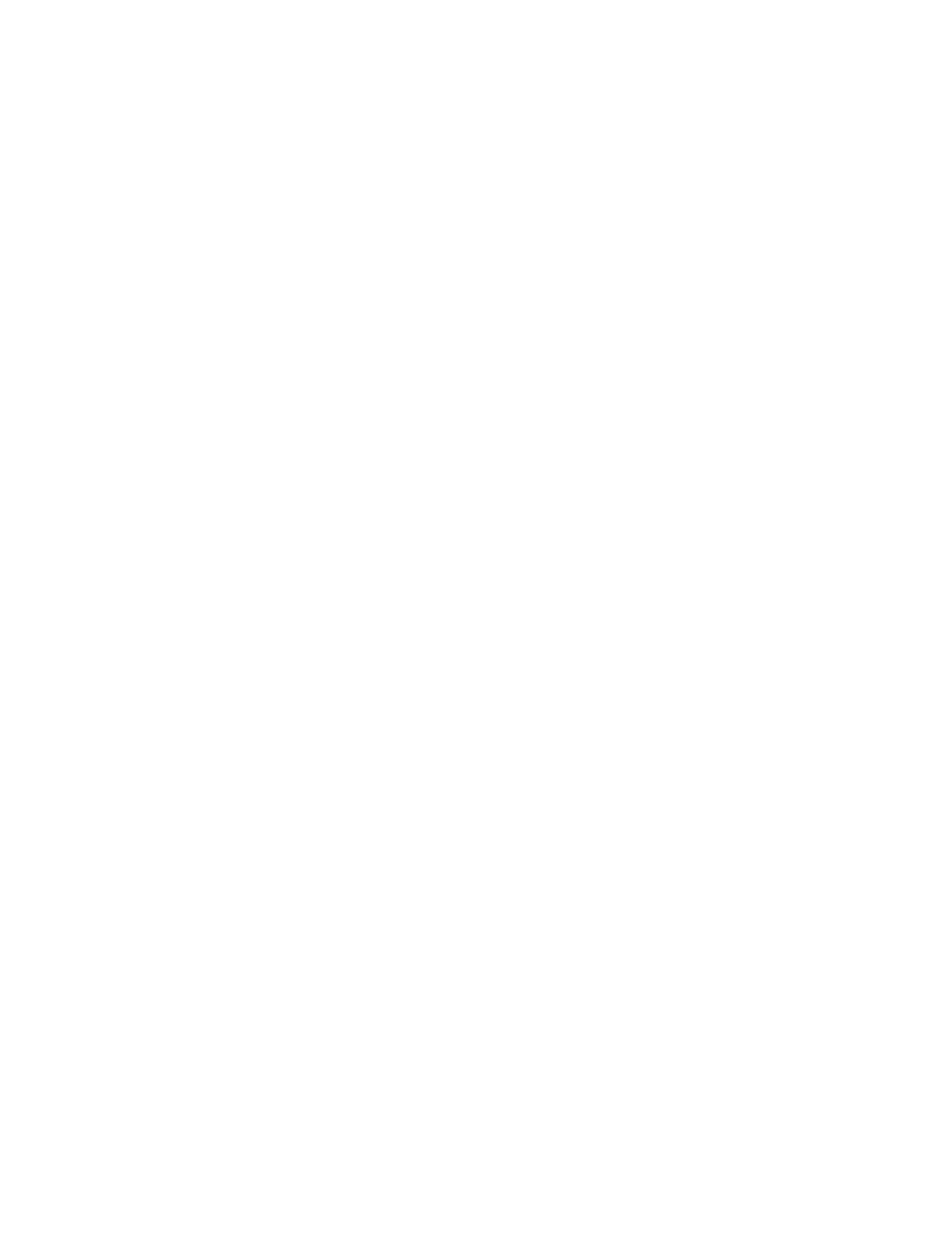
6
Aerovent IM-500
required, as structural design of accessories
will support these items. However, rails should
be extended to support cross members of the
accessories. Check the drawings in the front of
this manual.
Electrical Connections
CAUTION:
Disconnect power source before making wiring connec-
tions to prevent electrical shock and/or equipment damage.
WARNING:
ALL UNITS MUST BE WIRED STRICTLY IN
ACCORDANCE WITH THE WIRING DIAGRAM
FURNISHED WITH THE UNIT AND IN
ACCORDANCE WITH THE NATIONAL ELECTRIC
CODE ANSI/NFPA 70, LATEST EDITION. UNIT
MUST BE ELECTRICALLY GROUNDED IN
CONFORMANCE TO THIS CODE. ANY WIRING
DIFFERENT FROM WIRING DIAGRAM SUPPLIED
SHOULD BE CLEARED WITH FACTORY
ENGINEERING WITH WRITTEN APPROVAL FOR
VALIDATION OF UNIT WARRANTY.
Any damage to, or failure of this equipment caused by
incorrect wiring of the unit is not covered under the stan-
dard product warranty.
Electrical wiring diagrams are furnished with each unit
and can be found in the O&M manual, and a permanent
laminated diagram is located on the inside of the electric
control cabinet door. All units are supplied with a labeled
terminal strip for ease of wiring.
The power supply to the standard unit is be protected
with a lockable type fused disconnect switch. If a discon-
nect switch is not supplied with the unit, the field supplied
disconnect must have adequate ampacity and must be
installed in accordance with Article 430 of the National
Electrical Code, ANSI/NFPA 70.
External electrical service connections which must be
made include:
1. Main power supply to unit (120, 208, 240, 480, or 575
volt).
2. Remote control panel. Consult unit wiring diagram.
3. Separate 120V service for lighting and receptacles as
required.
4. Control wires connected to the remote temperature
selector must not be run close to or inside conduit with
power or ignition wires. Doing so may cause the unit
to function erratically or may destroy the amplifier. If
shielded wires are used, shield must be insulated and
grounded at the amplifier location only.
Supply voltage must be within 10 percent of the power rat-
ing with each phase balanced to within 2 percent of each
other. If not, advise the power company.
Before powering unit, make sure all multi-
voltage components (transformers, motors, etc.)
are wired in accordance with the correct supply
voltage.
The lighting circuits and unit receptacles
require the installation contractor to supply a
separate 120 volt single supply source to the
unit and be installed in accordance with Article
210 of the National Electrical Code ANSI/NFPA
70 - 1987.
Gas Piping Installation
CAUTION:
Gas pressure to main gas manifold must NEVER
EXCEED 5 psi.
The unit and its individual shutoff valve(s) must
be disconnected from the gas supply during any
pressure testing of the piping system. Before
assembling piping to unit manifold contractor
should be sure all rust, piping compound and
shavings have been removed from new piping.
(Strainers are recommended between unit pipe
train and supply piping.)
Always check the unit’s data form to determine the cor-
rect gas supply pressure for which the unit was designed.
1. Installation of piping must be in accordance with local
codes, and ANSI Z223.1, latest edition, “National Fuel
Gas Code”. (In Canada CAN/CGA-B149 Code).
2. Piping to units must conform to local and national
requirements for type and volume of gas handled,
and pressure drop allowed in the line. Refer to the air
make-up data form to determine the Btu capacity of
the unit and the type of gas the unit is designed to use.
Using this information refer to the ASHRAE Guide
Fundamentals Handbook, or other gas pipe sizing
guide to determine the correct supply pipe size. Allow
sufficient pipe size based on allowable pressure drop
in supply line. Where several units are served by the
same main, the total capacity of all the units served by
the main must be used. Avoid pipe sizes smaller than
1
/
2
".
3. After threading and reaming the ends, inspect piping
and remove loose dirt and chips.
4. Support piping so that no strains are imposed on the
unit controls.
5. Use two wrenches when connecting field piping to
units.
6. Provide a drip pocket before each unit and in the line
where low spots cannot be avoided.
7. Take-off to unit should come from top or side of main
to avoid trapping condensate.
8. Piping subject to wide temperature variations should
be insulated.
9. Pitch piping at least
1
/
4
" per 15 feet of horizontal
run.
10. Compounds used on threaded joints of gas piping
must be resistant to action of liquefied petroleum
gases.