Unit location restrictions and considerations, Sound and vibration levels, Installation – Aerovent IM-500 User Manual
Page 4
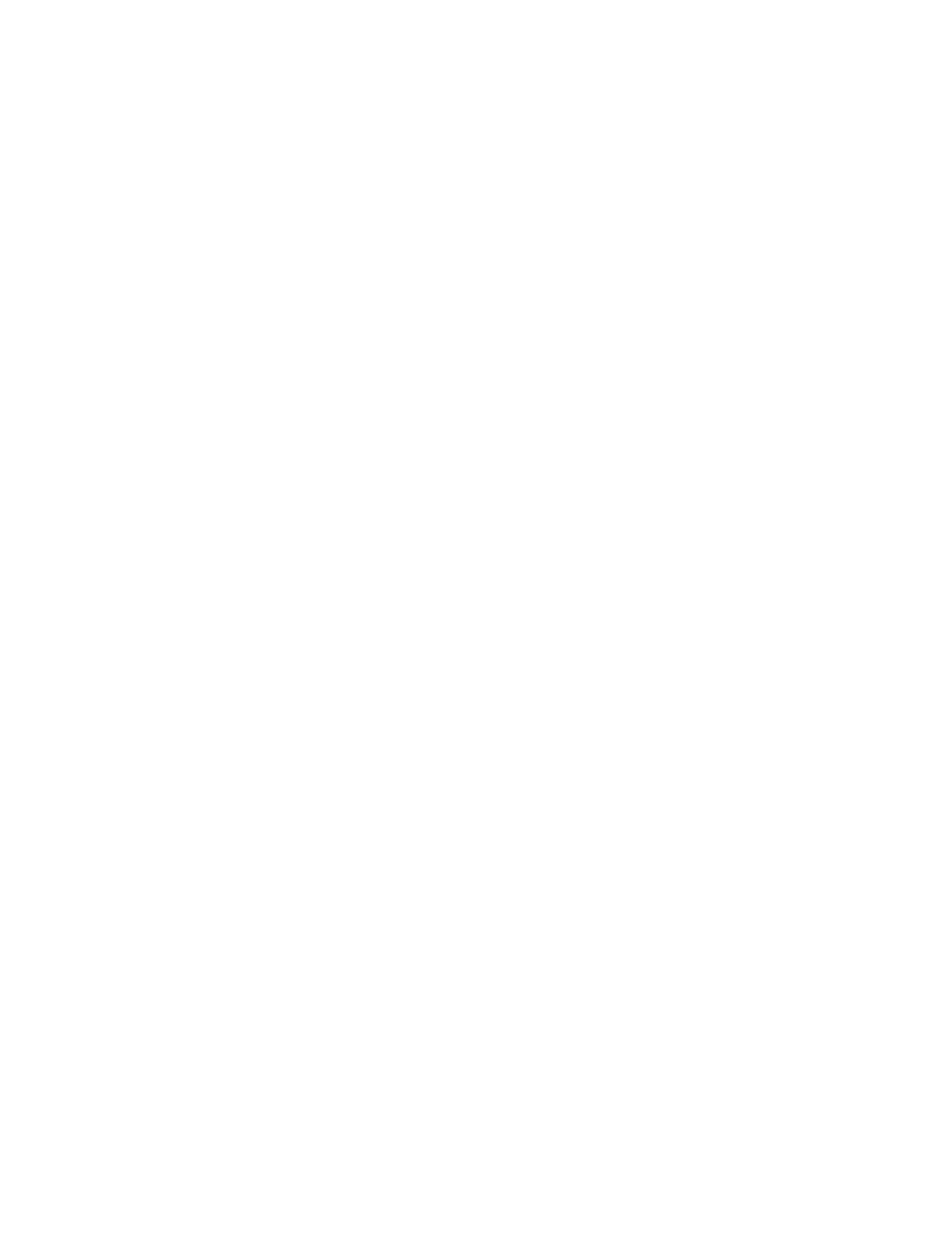
4
Aerovent IM-500
B. All installation of this equipment must be performed
by a qualified installation agency only defined in ANSI
Z223.1.
C. Electrical ANSI/INFPA #70-1987.
D. Aircraft hangar NFPA 409.
E. National Fuel Gas Code NFPA 54.
F. Installation of air conditioning and ventilating systems
NFPA 90A.
G. Parking Structures and Repair Garages NFPA 54.1.
Unit Location Restrictions and
Considerations
CAUTION
Units must not be installed where they may be exposed
to explosive or flammable atmospheres. In Canada, only
100% make-up air direct-fired units may be installed and
they must be applied solely for replacing exhausted inside
air with heated outside air.
1. Do not locate any gas-fired equipment where chlori-
nated or acid vapors are present in the combustion air
atmosphere.
2. When locating units, consider general space and heat-
ing requirements and availability of gas and electrical
supply.
3. Maintain minimum clearances to combustibles. The
minimum clearances are, 12" from the top, 12" from
the bottom, 12" from the sides, and 12" from the
ends.
4. Where necessary to provide working clearance beneath
the unit, the unit shall be installed at a suitable height
above the floor or otherwise adequately protected.
5. Allow 36" clearance on both sides of the unit for ser-
vice access.
6. Do not modify or block combustion or ventilation
openings. Do not modify burner profile opening.
7. Do not install direct-fired units down stream from any
cooling system that utilizes refrigerants for cooling.
8. Be sure the structural support at the unit location is
adequate to support the weight of the unit.
9. Units require field support of the accessory filters and
inlet hood.
10. Some models may be split shipped to accommodate
maximum shipping widths. When assembling unit sec-
tions, make sure that the sections are properly caulked
and secured before operating the equipment.
11. Provide sufficient airflow across the burner. Refer to
unit data sheet for required airflow (cfm).
12. Units with motor horsepower below 7.5 hp are sup-
plied with an adjustable motor sheave. Units with 7.5
hp motors and above are supplied as standard with
fixed motor and blower drives. Units are supplied from
the factory with drives set for static pressure conditions
provided at the time of order. Check to make sure the
actual job site conditions match the conditions for
which the unit was ordered. If proper airflow cannot
be established with the drives furnished with the unit,
contact the factory for information on drive changes.
13. For economical installation and operation, locate each
unit close to the space it will serve, and close to the
utilities that will serve the unit.
Site Preparation
Before attempting to install the unit, be sure the site is
properly prepared.
1. Make sure there is enough clearance around the instal-
lation site to properly and safely rig and lift the equip-
ment.
2. Watch for overhead power lines, or nearby utilities to
prevent accidental contact and damage.
3. Make sure the unit supports are adequate to support
the equipment.
Sound and Vibration Levels
All mechanical equipment generates some sound and vibra-
tion that may require attenuation. Locate the equipment
away from critical areas whenever possible. Frequently units
can be mounted above utility areas, corridors, restrooms,
and other non-critical areas. Generally a unit should be
located within 15 feet of a primary support beam. Smaller
deflections mean less vibration and noise transmission.
Field installed, factory supplied vibration iso-
lators are available for suspended or rail/slab
mounted units. Internal, factory mounted blow-
er and motor isolation may be ordered as an
option at the time the unit is ordered.
Installation
Duct Connections
To assure proper airflow from the discharge of the unit
follow these recommendations:
1. Be sure properly sized and designed discharge ducts
are installed. Velocities should be selected from 2,000
ft/min to no more than 3,000 ft/min for optimum effi-
ciency of operation.
2. Units should have a common discharge plenum of at
least three (3) hydraulic duct diameters.
3. As a general rule, all discharge ducts should have a
straight run of at least three (3) hydraulic duct diameters
before making turns in the ductwork.
Hydraulic Duct Diameter for Rectangular Ducts
= Dh = 4A/P
Hydraulic Duct Diameter for Circular Ducts
= Dh = D
Where:
Dh = Hydraulic Diameter
A = Cross Sectional Area of Rect. Duct
P = Perimeter of Rectangular Duct
D = Diameter of Round Cut