Installation/start up, 1 locating the polyfeeder system, 2 piping system – Pulsafeeder Polyfeeder EN User Manual
Page 9: 3 inlet water pressure and flow requirements
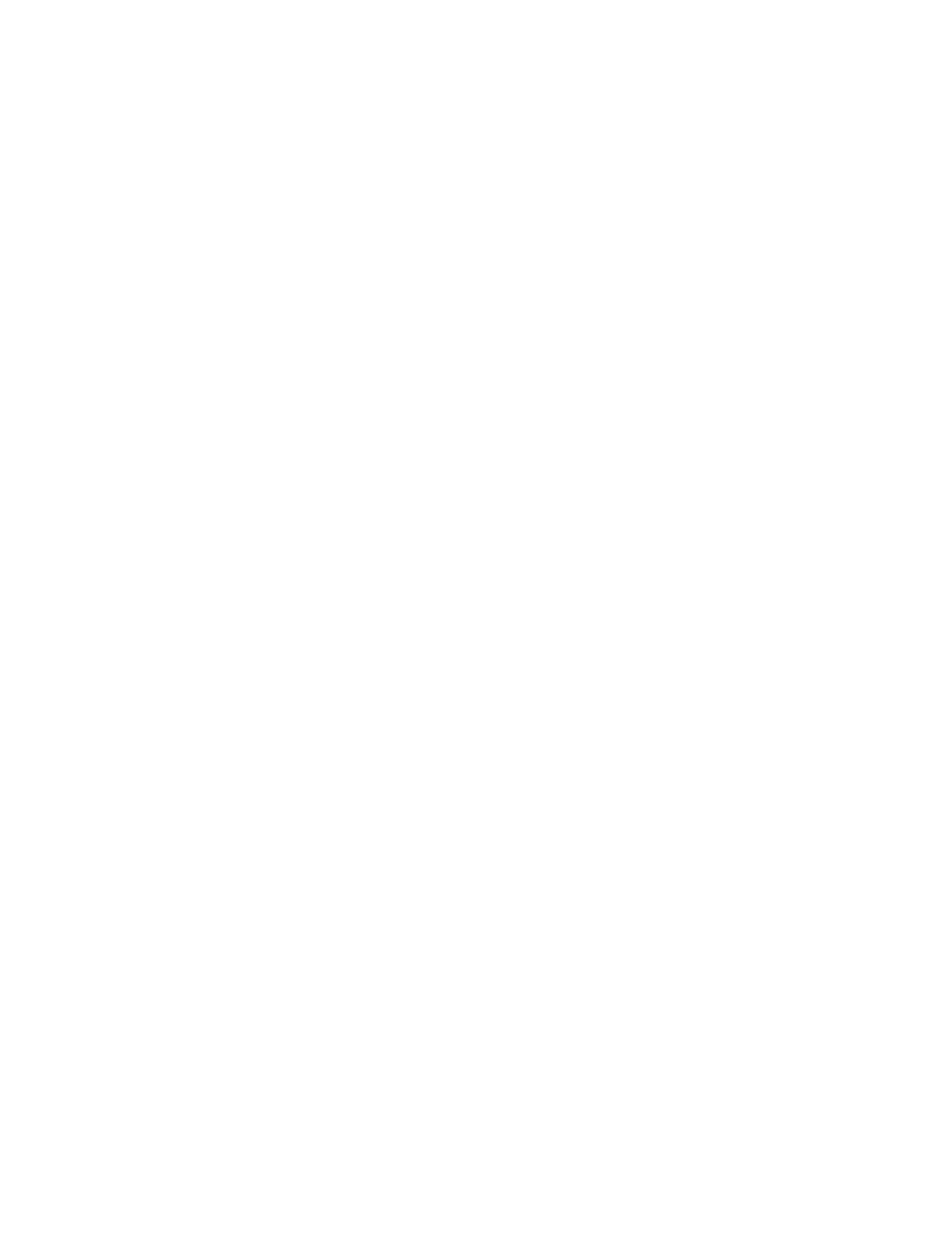
9
6.
Installation/Start
Up
6.1 Locating the Polyfeeder System
When selecting an installation site or designing a chemical feed system, consideration should be given
to access for routine maintenance.
The PolyFeeder system is designed to operate indoors and outdoors, but it is desirable to provide a hood
or covering for outdoor service. External heating is required if ambient temperatures below 0
C (32
F) are anticipated, especially if system will not be in continuous duty. Check with the factory if
concerned with the suitability of the operating environment.
The system must be rigidly bolted to a solid and flat foundation to minimize vibration, which can loosen
connections. When the system is bolted down, care must be taken to avoid distorting the base and
affecting alignments. The PolyFeeder must be level within 5
. This will assure that all of the
components can operate properly.
6.2 Piping
System
1. Shutoff valves on suction and discharge piping are recommended. These valves will permit system
inspection and maintenance without draining long runs of piping, making periodic maintenance and
inspection easier.
Shutoff valves should be of the same size as connecting pipe. Ball valves are preferred since they
offer minimum flow restriction. All ball valves shall be of the “full port” design.
2. Suction systems should include an inlet strainer for the water to prevent solids and debris from entering
and damaging the pump or mix chamber. The strainer should be located between the suction shutoff
valve and the system inlet. It must be sized to accommodate the flow rate and the anticipated level of
contamination. A 100 mesh screen size is generally recommended.
3. Vacuum/pressure gauges in the suction and discharge lines are helpful in order to check system
operation. Gauges should be fitted with protective shutoff valves for isolation while not in use.
4. Piping weight must not be supported by the piping connections or other portions of the system, as the
resulting stresses can cause leaks. If appropriate, provide for thermal expansion and contraction so
that no excess force or moments are applied to the system fittings.
5. In piping assembly, use a sealing compound chemically compatible with the process material. Users of
sealing tape are cautioned to ensure that the entering pipe thread ends are not taped, and that tape is
removed from previously-used threads to the maximum practical extent prior to re-use.
6. Both new and existing piping should be cleaned, preferably by flushing with a clean liquid
(compatible with process material) and blown out with air, prior to connection to the pump. Debris
from the piping system that prevents proper check valve operation is a common startup issue.
7. Ensure that no water is present in any of the neat polymer piping prior to the connection of the neat
polymer supply. Water mixing with the neat polymer solution prior to the membrane regulator and
mix chamber will cause coagulation and clogging.
6.3
Inlet Water Pressure and Flow Requirements
The system has been designed to have a minimum of 30 psig water pressure (maximum of 80 psig) in
order to operate correctly. If plant water pressure is higher, but fluctuates, it may be necessary to add a
water pressure regulating valve to the suction of the system. If water pressure is not steady, the pressure
fluctuations will cause water flow increases and decreases, which will cause concentration variations in
manual systems.