Ontrol, Xplanations, On/off control – Red Lion PXU User Manual
Page 22: Pid control
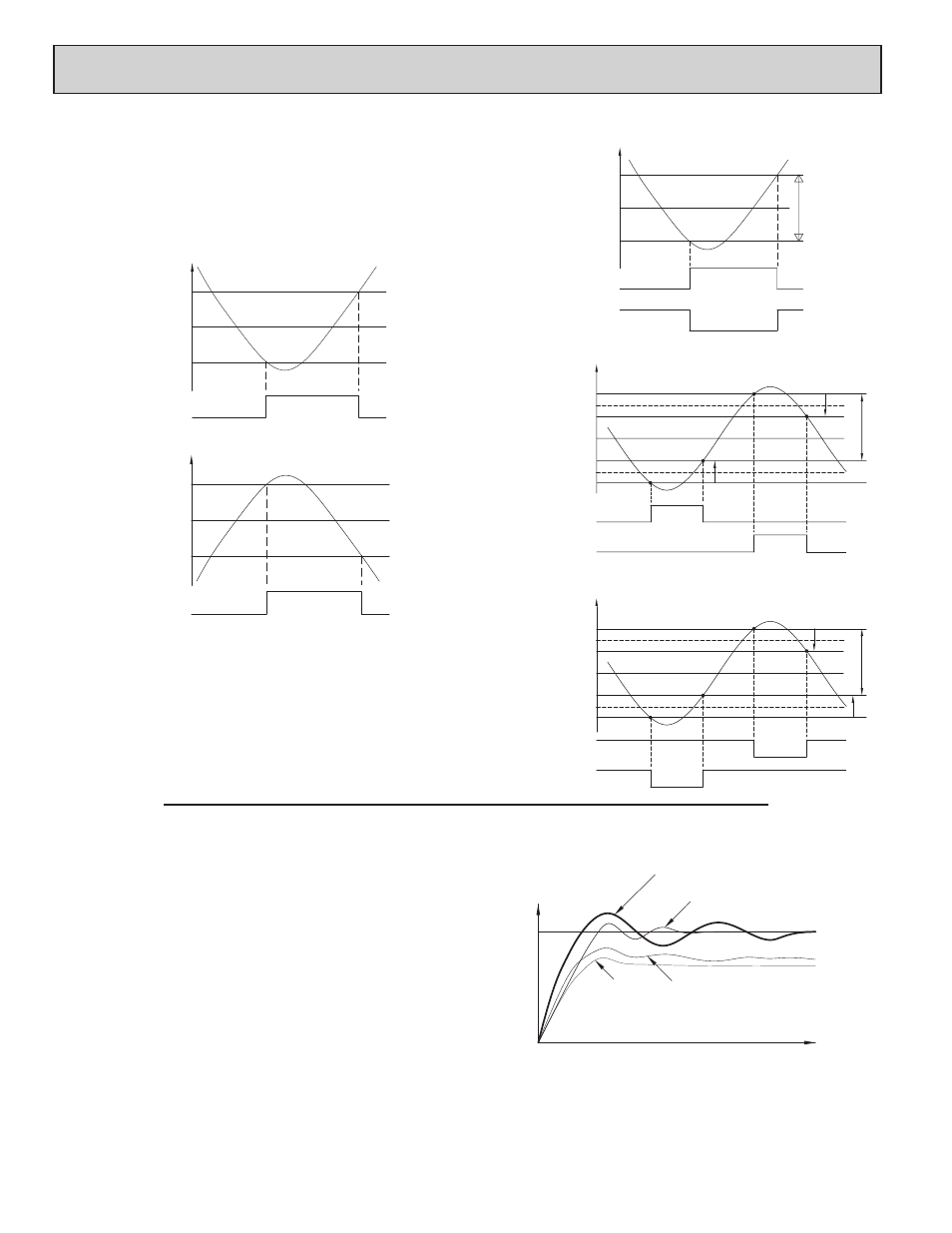
22
22
ON/OFF CONTROL
In this control mode, the process will constantly oscillate around the setpoint
value. The On/Off Control Hysteresis (balanced around the setpoint) can be
used to eliminate output chatter. Output Control Action can be set to reverse for
heating (output on when below the setpoint) or direct for cooling (output on
when above the setpoint) applications.
ON/OFF CONTROL -
REVERSE OR DIRECT ACTING FIGURES
Note: CHYS in the On/Off Control Figures refers to the On/Off Control
Hysteresis (
C
) in parameter Module 2.
For heat and cool systems, Control Action parameter is used to reverse (r) for
heating and direct (d) for cooling. The Deadband/Overlap in Cooling sets the
amount of operational deadband or overlap between the outputs. The setpoint
and the On/Off Control Hysteresis applies to both OP1 and OP2 outputs. The
hysteresis is balanced in relationship to the setpoint and deadband value.
C
OnTrOl
m
Ode
e
xplanaTiOns
ON
Output (d) :
ON
SP
OFF
INPUT
DEADBAND/OVERLAP
(db2) = 0
SP + 1/2 CHYS
SP - 1/2 CHYS
OFF
OFF
Output (r) :
ON
CHYS
SP
SP + 1/2 (db-2) - 1/2 CHYS
SP + 1/2 (db-2) + 1/2 CHYS
SP - 1/2 (db-2) + 1/2 CHYS
SP - 1/2 (db-2) - 1/2 CHYS
DEADBAND/OVERLAP (db-2) < 0
db-2
CHYS
CHYS
ON
OFF
OFF
ON
Output (r) :
Output (d) :
db-2
Output (r) :
Output (d) :
SP - 1/2 (db-2) + 1/2 CHYS
SP - 1/2 (db-2) - 1/2 CHYS
OFF
SP
ON
OFF
OFF
ON
CHYS
OFF
DEADBAND/OVERLAP (db-2) > 0
SP + 1/2 (db-2) - 1/2 CHYS
SP + 1/2 (db-2) + 1/2 CHYS
CHYS
ON
ON
INPUT
INPUT
SP + 1/2 (db-2)
SP - 1/2 (db-2)
SP + 1/2 (db-2)
SP - 1/2 (db-2)
ON/OFF CONTROL - HEAT/COOL OUTPUT FIGURES
PID CONTROL
In PID Control, the controller processes the input and then calculates a
control output power value by use of Proportional Band, Integral Time, and
Derivative Time control algorithm. The system is controlled with the new
output power value to keep the process at the setpoint. The Control Action for
PID Control can be set to reverse for heating (output on when below the
setpoint) or direct for cooling (output on when above the setpoint) applications.
For heat and cool systems, the heat and cool outputs are both used. The PID
parameters can be established by using Auto-Tune, or they can be Manually
tuned to the process.
SP
TIME
P & I
P & I & D
P only
P & D
INPUT
TYPICAL PID RESPONSE CURVE
OFF
Output (d) :
SP
OFF
INPUT
DIRECT ACTING
SP - 1/2 CHYS
SP + 1/2 CHYS
ON
OFF
Output (r) :
SP
OFF
INPUT
REVERSE ACTING
SP - 1/2 CHYS
SP + 1/2 CHYS
ON