Isplay, Arameter, Idden – Red Lion PXU User Manual
Page 10: Escriptions
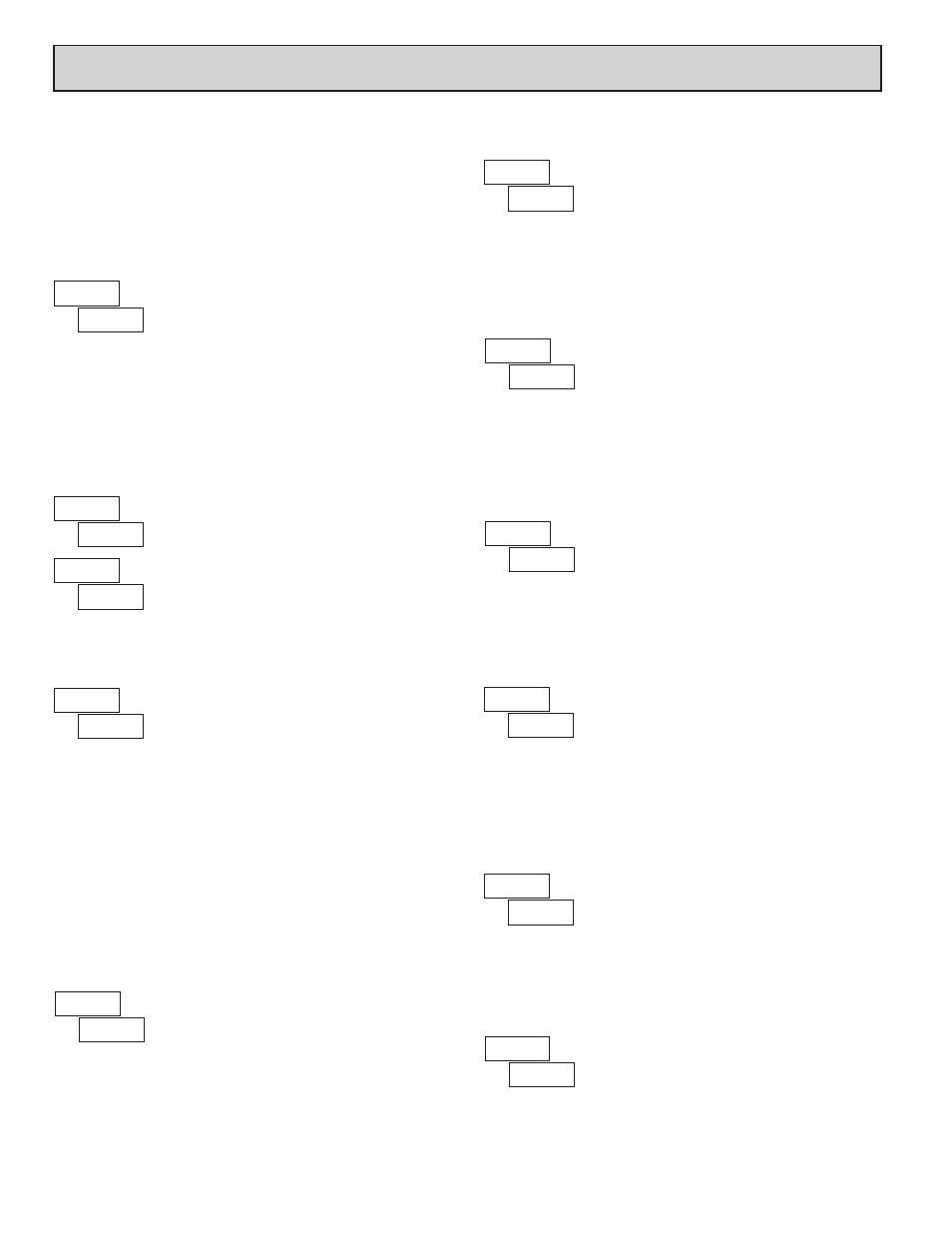
10
SETPOINT RAMP RATE
to
display units/minute *
By ramping the setpoint at a controlled rate, the setpoint ramp rate can reduce
sudden shock to the process and reduce overshoot on startup or after setpoint
changes. When viewing setpoint value, and the setpoint is ramping, the setpoint
will alternate between
rSP
x and the target setpoint value. The ramp rate is in least-
significant (display units) digits per minute. A value of 0 disables setpoint
ramping. Once the ramping setpoint reaches the target setpoint, the setpoint ramp
rate disengages until the setpoint is changed again. If the ramp value is changed
during ramping, the new ramp rate takes effect. If the setpoint is ramping prior to
starting Auto-Tune, the ramping will terminate when Auto-Tune starts. Deviation
and band alarms are relative to the target setpoint, not the ramping setpoint. A
slow process may not track the programmed setpoint rate. At power up, the
ramping setpoint is initialized to the current temperature/process value.
ACTIVE SETPOINT VALUE
to
display units *
CONTROL OUTPUT 1 or 2 % OUTPUT POWER
.
to
.
The parameter name indicates the active setpoint. The Setpoint value can be
changed by pressing the arrow keys. This parameter can be configured as read
only in the Display Loop, but read/write in the Hidden Loop (
dSPr
). Select the
second Setpoint value by using the 1 or 2 key, user input, or the
SPSL
parameter. Both Setpoint values are limited by the Setpoint Low and High
Limits in Input Module
1-IN
.
While the controller is in Automatic Mode, this value
is read only. When the controller is placed in Manual
Mode, the value can be changed by pressing the arrow
keys. For more details on % Output Power, see Control
Mode Explanations.
CONTROLLER STATUS
When in
rUN
mode, the control output(s) respond based on their corresponding
% output value. When in
StOP
mode, the control output(s) are disabled.
Integral wind-up can be reset by entering
StOP
and then going back to
rUN
mode.
I
PID GROUP
or
Select different PID parameters by choosing one of two different PID groups.
The following parameters may be locked from display or made available in
either the main Display Loop, the Parameter Loop or the Hidden Loop as
configured in programming module
3-LC
. Values configured for
dSPr
are read
only when in the main display loop, but are writable when in the Hidden Loop.
The value mnemonics are shown for each parameter, as well as the factory
setting for each of the values.
.
OUTPUT POWER OFFSET
When the Integral Time is set to zero, the power offset is used to shift the
proportional band to compensate for errors in the steady state. If Integral Action
is later invoked, the controller will re-calculate the internal integral value to
provide “bumpless” transfer and Output Power Offset will not be necessary.
.
to
.
% power
x
.
.
7
PROPORTIONAL BAND
to
display units *
The proportional band should be set to obtain the best response to a process
disturbance while minimizing overshoot. For more information, see Control
Mode and PID Tuning Explanations.
I
INTEGRAL TIME
to
seconds
Integral action shifts the center point position of the proportional band to
eliminate error in the steady state. The higher the integral time, the slower the
response. The optimal integral time is best determined during PID Tuning.
3
DERIVATIVE TIME
to
seconds per repeat
Derivative time helps to stabilize the response, but too high of a derivative
time, coupled with noisy signal processes, may cause the output to fluctuate too
greatly, yielding poor control. Setting the time to zero disables derivative action.
.
I
INTEGRATION DEFAULT
.
to
.
% output power
The Integration Default is the default integration value of integral control.
When the process value enters the proportional band, the PXU will take the
Integration Default as the default control output of integral control. The value is
determined at Auto-Tune.
d
isplay
/p
arameTer
/h
idden
l
OOp
p
arameTer
d
esCripTiOns
* Range/Decimal position is Programming dependent.