3 grounding, 3 parallel master/slave configurations, Grounding -11 – KEPCO EL Series Electronic Load Operator Manual P/N 243-1295 Firmware Version 3.63 through 3.86 User Manual
Page 29: Parallel master/slave configurations -11
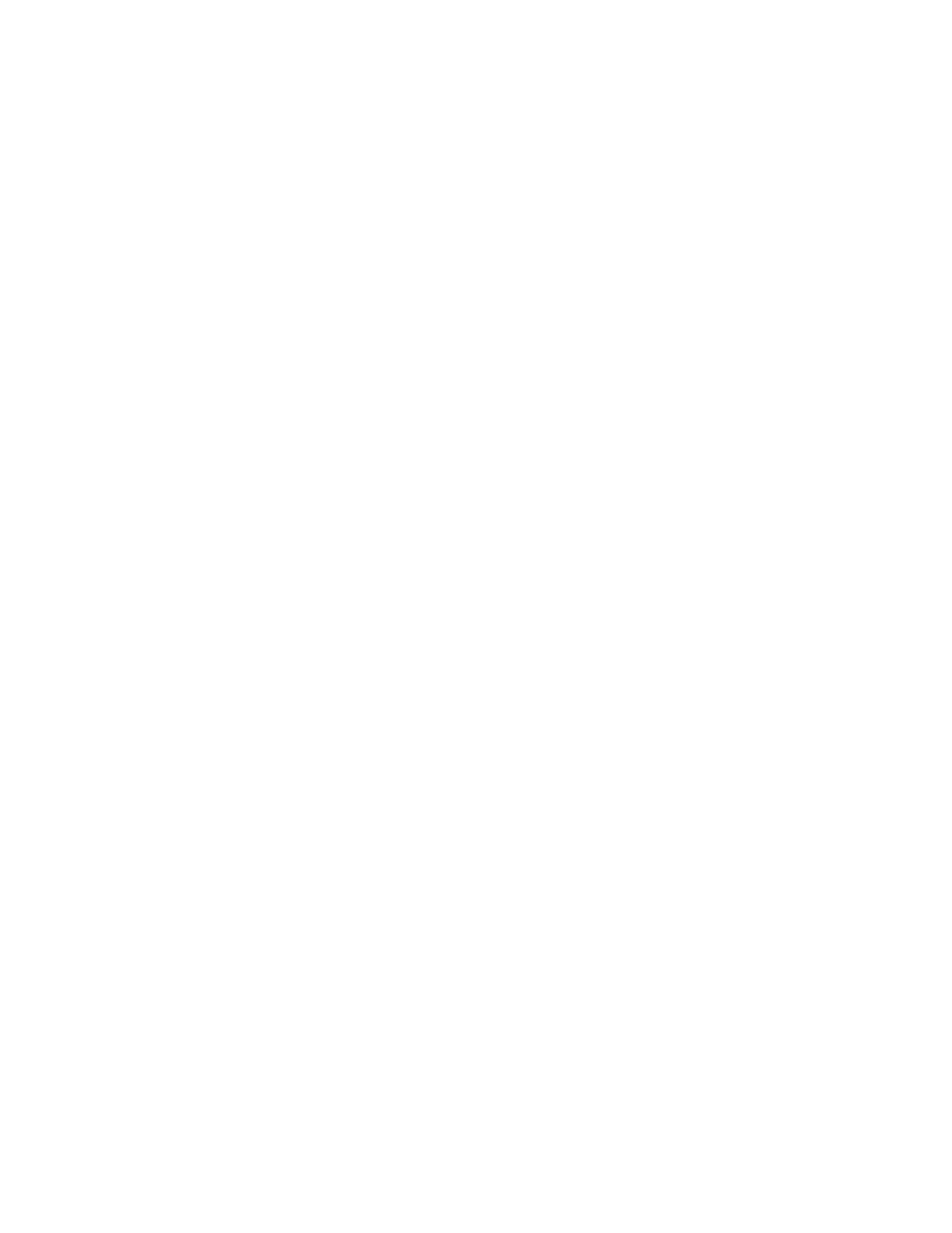
SERIES EL 070312
2-11
2.6.2.3
GROUNDING
It is recommended that the 1/4-inch bolt with wingnut and flat washers (supplied) at the top left
of the rear panel be connected to earth ground.
The LOAD Bus bars are isolated from the chassis and from the control circuits well into the 100s
of volts. The PGM (Program) input (ANALOG CONTROL connector, pin 1, pin 15 return) is iso-
lated from the control circuits (and are therefore doubly isolated from the LOAD Bus) up into the
100s of volts. The I-Load output (ANALOG CONTROL connector, pin 2, pin 13 return) is inde-
pendently isolated from the control circuits and therefore is double-isolated from all other exter-
nal connections. Lastly, all of the Remote Interface inputs (RS-232, USB 2.0, RS-522), optional
LAN and GPIB) are optically isolated from the control circuits and are therefore doubly isolated
from all other circuits.
2.6.3
PARALLEL MASTER/SLAVE CONFIGURATIONS
Up to 15 Series EL Electronic Loads may be paralleled for additional current and/or power han-
dling capability. All units must have the same voltage rating. One load is designated as the Mas-
ter, and the rest are designated as slaves. Master/slave communications are via proprietary
protocols using special cable(s) connected to the MSTR O (Master Out) and SLAVE I/O connec-
tors on the rear panel (see Table 1-5). Connections are from MSTR O to SLAVE I/O, then for
subsequent slaves, from SLAVE I/O to SLAVE I/O of the next unit. Computer/load communica-
tions are via either the RS 232 or USB (or optional LAN or GPIB) interfaces, and are applied to
the master only. Figure 2-9 illustrates connections for a typical master/slave system.
In a Master-Slave configuration, two or more Loads operate in parallel to increase the total cur-
rent and power capacity.
CAUTION: Loads in Master-Slave configuration are always operated in PARALLEL,
never in series. Each Load in the system must have exactly the same maxi-
mum voltage limit-otherwise the Load internal software will not allow the
Loads to configure as a Master-Slave system. Paralleling two Loads of
unequal voltage rating and applying a voltage greater than the limits of the
Load with the lower voltage rating can result in the destruction of the Load,
the connected source or both.
Typically Loads are stacked vertically to minimize the distance between the ± LOAD terminals. It
is essential to keep this cabling as short as possible due to the high currents flowing during
operation. One of the Loads is designated as the Master and the other as the Slave. Any Load
may be designated as the Master.
Master-Slave configuration is achieved by two interconnections at the Load rear panel (see Fig-
ure 2-9): First connect the ± LOAD terminals of master and all slaves in parallel using sufficiently
heavy cable to carry the maximum current expected to be drawn by any of the individual loads.
Next connect the UUT (Unit Under Test) to the ± LOAD terminals. Use of No. 6 (or larger) Weld-
ing Cable is recommended for flexibility, current carrying capacity and insulation.
For remote operation use the supplied RJ-22 Master-Slave communications bus cables (these
use miniature modular connectors - do not try to use conventional modular telephone cables).
Connect an RJ-22 bus cable from the MSTR O (Master Out) which is the upper most RJ-22
Jack, to the upper SLAVE I/O RJ-22 Jack on the slave. For more than one slave, connect lower
SLAVE I/O jack to the next unit’s upper SLAVE I/O jack, and so on. No terminations are needed
at the final slave in the daisy chain.