2 remote control, 3 analog programming, 4 digital calibration – KEPCO EL Series Electronic Load Operator Manual P/N 243-1295 Firmware Version 3.63 through 3.86 User Manual
Page 14: 5 damping, 6 built-in protection, 7 master/slave control, Remote control -4, Analog programming -4, Digital calibration -4, Damping -4
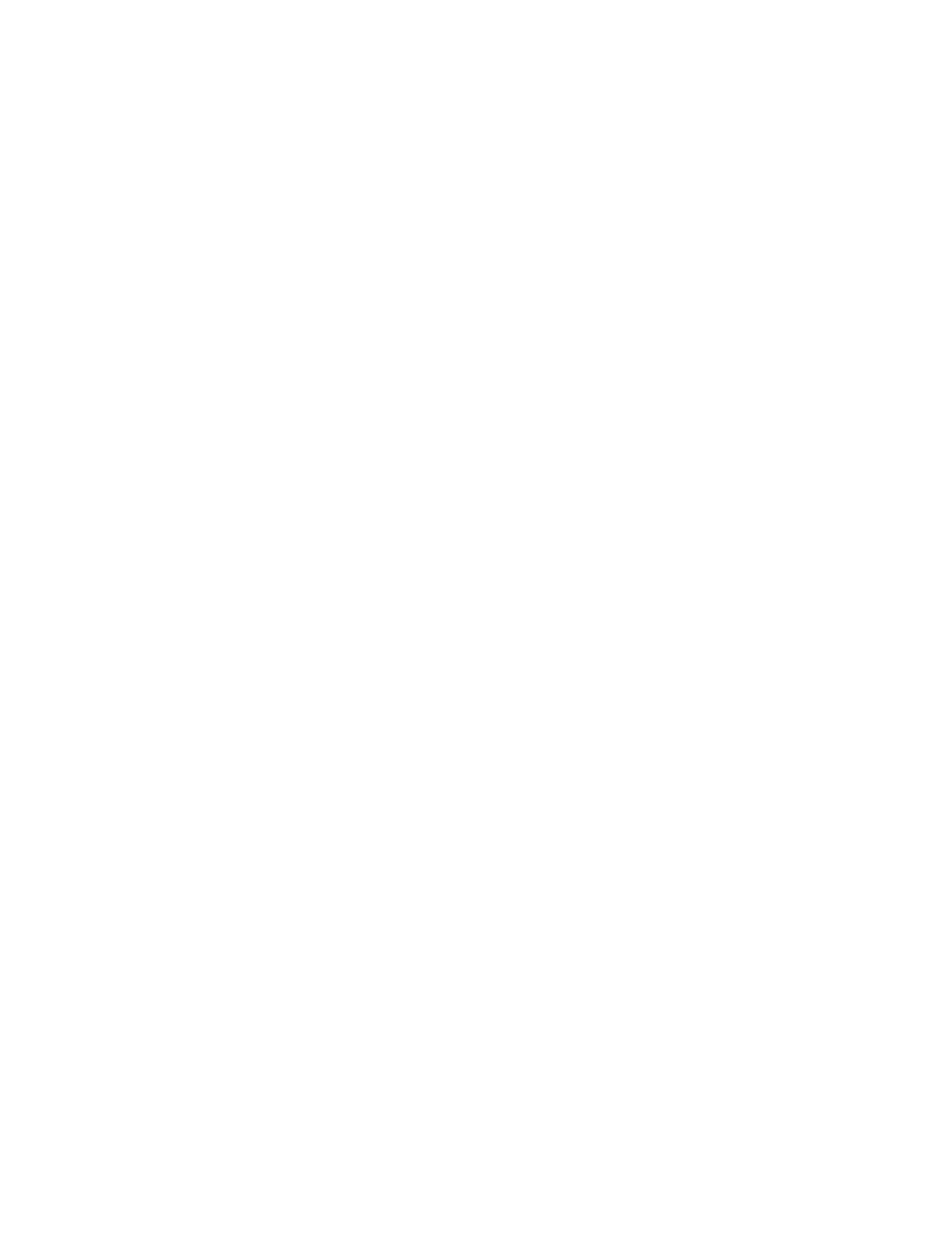
1-4
SERIES EL 070312
1.5.2
REMOTE CONTROL
Remote control of the Series EL Electronic Load is accomplished from a remote device using
SCPI commands and either RS 232 or USB protocols. GPIB (G suffix) or LAN (E suffix) proto-
cols are available as an option. The RS 232 and USB ports cannot be turned off, therefore the
Series EL can always be controlled via these ports. Digital commands expand the control avail-
able from the front panel, and include damping when required for square wave or pulse type
requirements, overvoltage, undervoltage, overcurrent and overpower protections.
1.5.3
ANALOG PROGRAMMING
An analog input is provided via the 15-pin ANALOG CONTROL connector at the rear that allows
the user to use a 10V analog signal to control the voltage, current or power, depending on the
mode selected. See PAR 3.15 for details.
1.5.4
DIGITAL CALIBRATION
Internal adjustments of the Series EL Electronic Load are automatic. Calibration can be per-
formed remotely via one of the remote interfaces.
1.5.5
DAMPING
Typical operation for an electronic load involves the flow of high currents. The combination of
high, rapidly changing currents and the inductance associated with connections to the load via
lead wires can cause unexpected results, such as very high voltage spikes, oscillation or severe
ringing (damped oscillations) at the source. To help reduce these issues, the Series EL offers
multiple forms and degrees of damping, allowing the best measurements possible. See PAR.
3.14 for details.
1.5.6
BUILT-IN PROTECTION
• Overtemperature. Thermal management of the EL Series is accomplished by continually
monitoring the temperature of each individual power-dissipating MOSFET. If the temper-
ature of a MOSFET begins to approach a dangerous level, then its power will be
reduced and the other MOSFETs will naturally increase their share via the control loops.
If the temperature of one or more of the MOSFETs exceeds safe operating limits, this
may cause either a reduction of the load maximum current/power handling ability or a
complete inability to use the load depending on the degree of overheating.
• The user can establish limits for overvoltage or undervoltage, overcurrent, or power
which can not be exceeded at the input. If the limits are exceeded, the unit disengages
from the UUT and a fault indication is displayed (see PAR. 3.3.1 for details).
1.5.7
MASTER/SLAVE CONTROL
For configurations that require power or current in excess of the maximum available from a sin-
gle unit, additional units can be added to the system to increase power/current capability, up to a
maximum of 14 additional units.