Brooks Instrument XacTorr CMX160 User Manual
Page 10
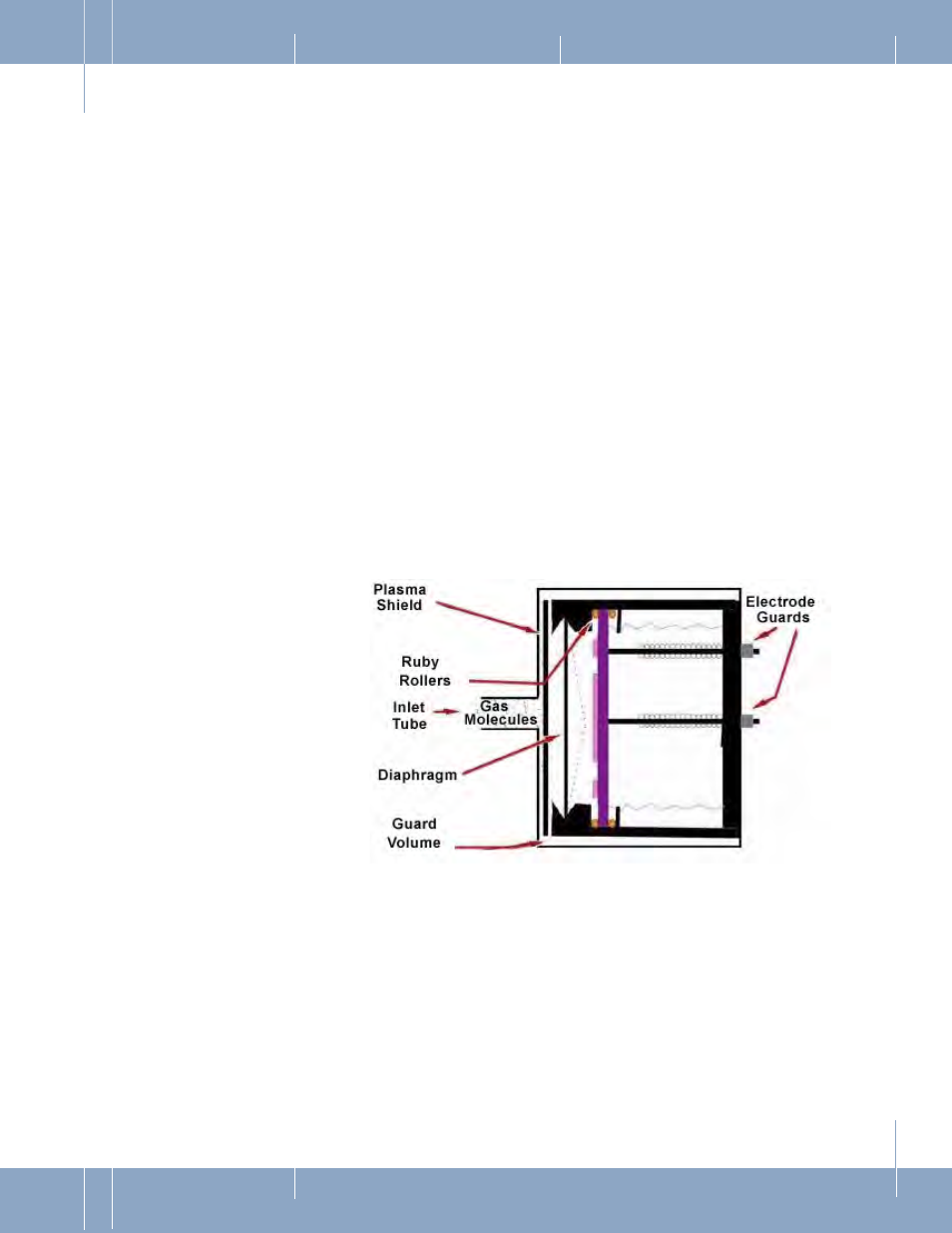
p.4
2.2 HISTORICAL DESIGN
Unfortunately the simple sensor design described previously, has a number of
drawbacks.
• The single large diaphragm is more sensitive to shock and vibration.
• A single electrode cannot distinguish between a true pressure change and
capacitance change due to thermal expansion or contraction of the sensor
housing.
• The diaphragm is exposed directly to the process environment, where thermal
radiation (from RF power) and condensable by-products (from the process)
contaminate it. This may even physically damage the diaphragm, changing its
characteristics of deflection.
• Internal frictional and stress forces (as an example: due to thermal expansion
and vibrations) can distort the pressure readings.
2.3 BROOKS CMX DESIGN
Brooks has created several patented solutions to remedy the above mentioned
drawbacks of the simple design described previously: (refer to Figure 2)
1. Use of a diaphragm that is smaller in diameter than in conventional CMs. A
smaller diaphragm has less mass, which makes it less sensitive to shock and
vibration.
Figure 2: Brooks CMX
2. Brooks uses a dual electrode system which incorporates a reference
electrode into the design. Pressure is determined by a change in the
measurement electrode relative to a change in the reference electrode. If the
spacing between the diaphragm and electrode changes due to thermal
expansion of the sensor’s chassis, both capacitances will change equally,
thus false capacitance changes brought about by thermal effects can be
distinguished from true pressure readings.
3. Brooks places a Plasma Shield in front of the diaphragm to protect the
diaphragm from the process environment. It is an Inconel
®
plate that covers
the entire front face of the diaphragm that traps condensable materials before
2.0
_DESCRIPTION