Brooks – Brooks Instrument 5850EM User Manual
Page 40
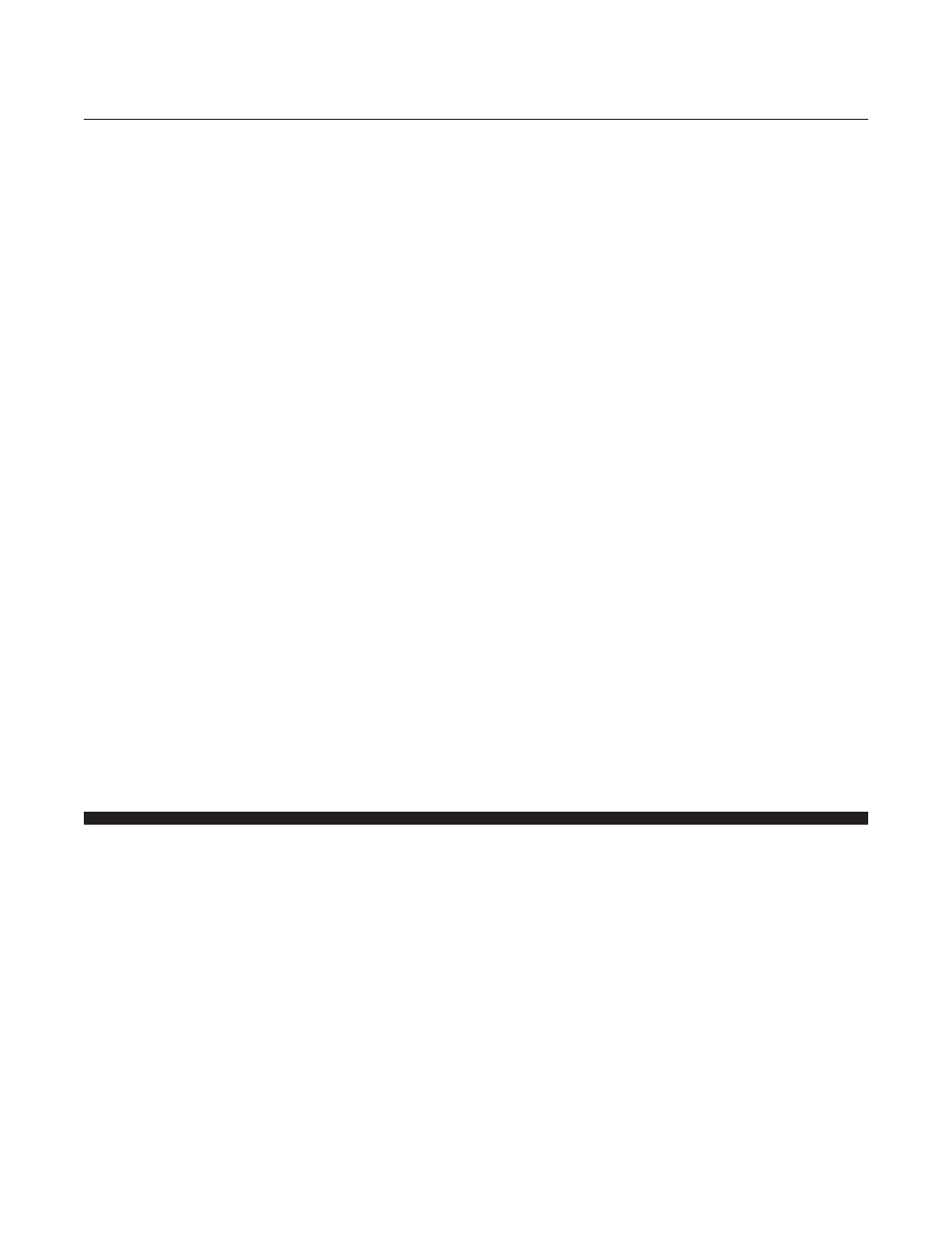
3-16
Brooks
®
Models 5964, 5850EM
Section 3 Operation
Installation and Operation Manual
X-TMF-5964-5850EM-MFC-eng
Part Number: 541B121AHG
November, 2008
Linearity
The linearity potentiometer is used to linearize the flow calibration due to
subtle non-linearities in various bypass elements. The linearity signal can
be viewed between TP2 and TP4 (circuit common). The value of the signal
is flow rate and gas dependent. On enhanced response PC boards
adjusting the potentiometer clockwise will increase the absolute value of
this number. On standard response and Current I/O PC boards adjusting
the potentiometer clockwise will increase this number. Adjusting this
potentiometer will alter the calibration and is therefore not recommended
unless calibrating the device.
Anticipate
The anticipate potentiometer is used to adjust the response of the sensor
for steps in flow. Adjusting this potentiometer in the clockwise direction will
slow the response of flow signal and cause a controller to overshoot
more. Adjusting this potentiometer will alter the response of the mass flow
controller and is therefore not recommended unless adjusting the response
of the device.
Zero
The zero potentiometer is used to balance the thermal sensor at a no flow
condition. This potentiometer is adjusted at the time of calibration and
minor adjustments may be done in the field. See the "Zero Adjustment"
section below for details.
Response
The response potentiometer is used to adjust the response of the sensor
for steps in flow. Adjusting this potentiometer in the clockwise direction will
increase actual flow overshoot. Adjusting this potentiometer will alter the
response of the mass flow controller and is therefore not recommended
unless adjusting the response of the device.
Note: Only enhanced response printed circuit boards are equipped with a
response potentiometer.
3-6 Zero Adjustment
Each Model 5964/5850EM is factory adjusted to provide a zero ±10 mVdc
at zero flow. The adjustment is made in our calibration laboratory which is
temperature controlled to 20°C (68°F ±3°F). After initial installation and
warm-up in the gas system, the zero flow indication may be other than the
factory setting. This is primarily caused by changes in temperature
between our calibration laboratory and the final installation. The zero flow
reading can also be affected, to a small degree, by changes in line
pressure and mounting attitude.
To check zero, always mount the controller in its final configuration and
allow a minimum of twenty minutes for the temperature of the controller
and its environment to stabilize. If an upstream shut-off valve is installed it
should be closed. Verify that the gas system is not pressurized. Using a
suitable voltmeter, check the controller output signal. If it differs from the
factory setting, adjust it by removing the lower pot hole plug (refer to Figure
3-2) which is located closest to the controller body. Adjust the zero
potentiometer until the desired output signal is obtained.