Rainbow Electronics MAX17480 User Manual
Page 46
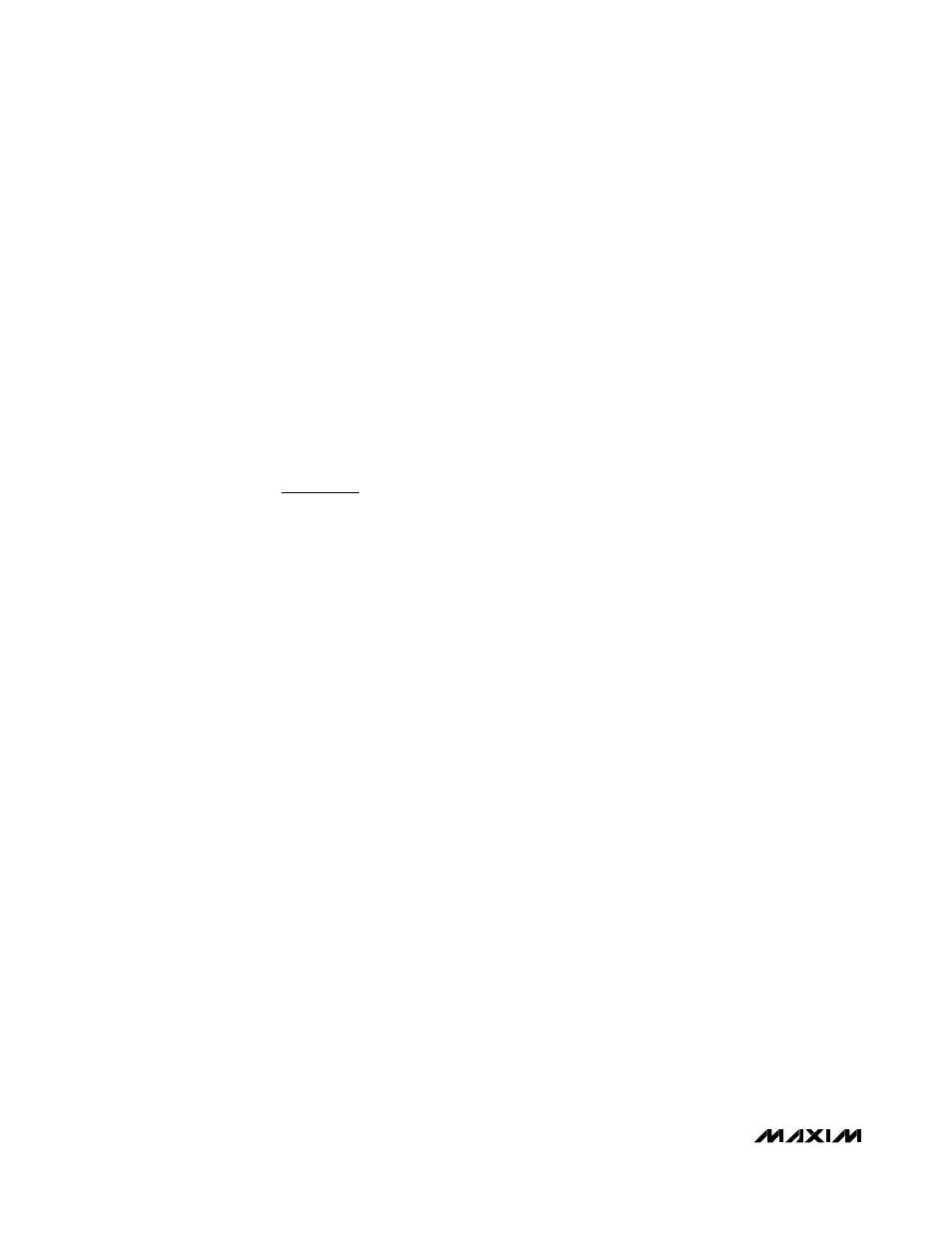
MAX17480
AMD 2-/3-Output Mobile Serial
VID Controller
46
______________________________________________________________________________________
Maximum Input Voltage
The MAX17480 controller has a minimum on-time,
which determines the maximum input operating voltage
that maintains the selected switching frequency. With
higher input voltages, each pulse delivers more energy
than the output is sourcing to the load. At the beginning
of each cycle, if the output voltage is still above
the feedback threshold voltage, the controller does not
trigger an on-time pulse, resulting in pulse-skipping
operation regardless of the operating mode selected by
PSI_L. This allows the controller to maintain regulation
above the maximum input voltage, but forces the con-
troller to effectively operate with a lower switching fre-
quency. This results in an input threshold voltage at
which the controller begins to skip pulses (V
IN(SKIP)
):
:
where f
SW
is the per-phase switching frequency set by
the OSC resistor, and t
ON(MIN)
is 150ns (max) minus the
driver’s turn-on delay (DL low to DH high). For the best
high-voltage performance, use the slowest switching
frequency setting (100kHz per phase, R
OSC
= 432k
Ω).
PCB Layout Guidelines
Careful PCB layout is critical to achieve low switching
losses and clean, stable operation. The switching
power stage requires particular attention (Figure 15). If
possible, mount all the power components on the top
side of the board with their ground terminals flush
against one another, and mount the controller and ana-
log components on the bottom layer so the internal
ground layers shield the analog components from any
noise generated by the power components. Follow
these guidelines for good PCB layout:
• Keep the high-current paths short, especially at the
ground terminals. This is essential for stable, jitter-
free operation.
• Connect all analog grounds to a separate solid cop-
per plane; then connect the analog ground to the
GND pins of the controller. The following sensitive
components connect to analog ground: V
CC
and
V
DDIO
bypass capacitors, remote sense and GNDS
bypass capacitors, and the resistive connections
(ILIM12, OSC, TIME).
• Keep the power traces and load connections short.
This is essential for high efficiency. The use of thick
copper PCB (2oz vs. 1oz) can enhance full-load effi-
ciency by 1% or more. Correctly routing PCB traces
is a difficult task that must be approached in terms of
fractions of centimeters, where a single m
Ω of
excess trace resistance causes a measurable effi-
ciency penalty.
• Connections for current limiting (CSP, CSN) and volt-
age positioning (FBS, GNDS) must be made using
Kelvin-sense connections to guarantee the current-
sense accuracy. Place current-sense filter capacitors
and voltage-positioning filter capacitors as close as
possible to the IC.
• Route high-speed switching nodes and driver traces
away from sensitive analog areas (REF, V
CC
, FBAC,
FBDC, OUT3, etc.). Make all pin-strap control input
connections (SHDN, PGD_IN, OPTION) to analog
ground or V
CC
rather than power ground or V
DD
.
• Route the high-speed serial-interface signals (SVC,
SVD) in parallel, keeping the trace lengths identical.
Keep the SVC and SVD away from the high-current
switching paths.
• Keep the drivers close to the MOSFET, with the gate-
drive traces (DL, DH, LX, and BST) short and wide to
minimize trace resistance and inductance. This is
essential for high-power MOSFETs that require low-
impedance gate drivers to avoid shoot-through cur-
rents.
• When trade-offs in trace lengths must be made, it is
preferable to allow the inductor charging path to be
made longer than the discharge path. For example, it
is better to allow some extra distance between the
input capacitors and the high-side MOSFET rather than
to allow distance between the inductor and the low-
side MOSFET or between the inductor and the output
filter capacitor.
Layout Procedure
1) Place the power components first, with ground ter-
minals adjacent (low-side MOSFET source, C
IN
,
C
OUT
, and DL anode). If possible, make all these
connections on the top layer with wide, copper-
filled areas. For the NB SMPS, place CIN3 and L3
as near as possible to the MAX17480, using multi-
ple vias to reduce inductance when connecting the
different layers.
2) Use multiple vias to connect the exposed backside to
the power ground plane (PGND) to allow for a low-
impedance path for the SMPS3 internal low-side
MOSFET.
3) Mount the MAX17480 close to the low-side
MOSFETs. The DL gate traces must be short and
wide (50 mils to 100 mils wide if the MOSFET is 1in
from the driver IC).
4) Group the gate-drive components (BST capacitors,
V
DD
bypass capacitor) together near the
MAX17480.
V
V
f
t
IN SKIP
OUT
SW ON MIN
(
)
(
)
=
⎛
⎝
⎜⎜
⎞
⎠
⎟⎟
1