Backplane data transfer – ProSoft Technology MVI56-PDPS User Manual
Page 60
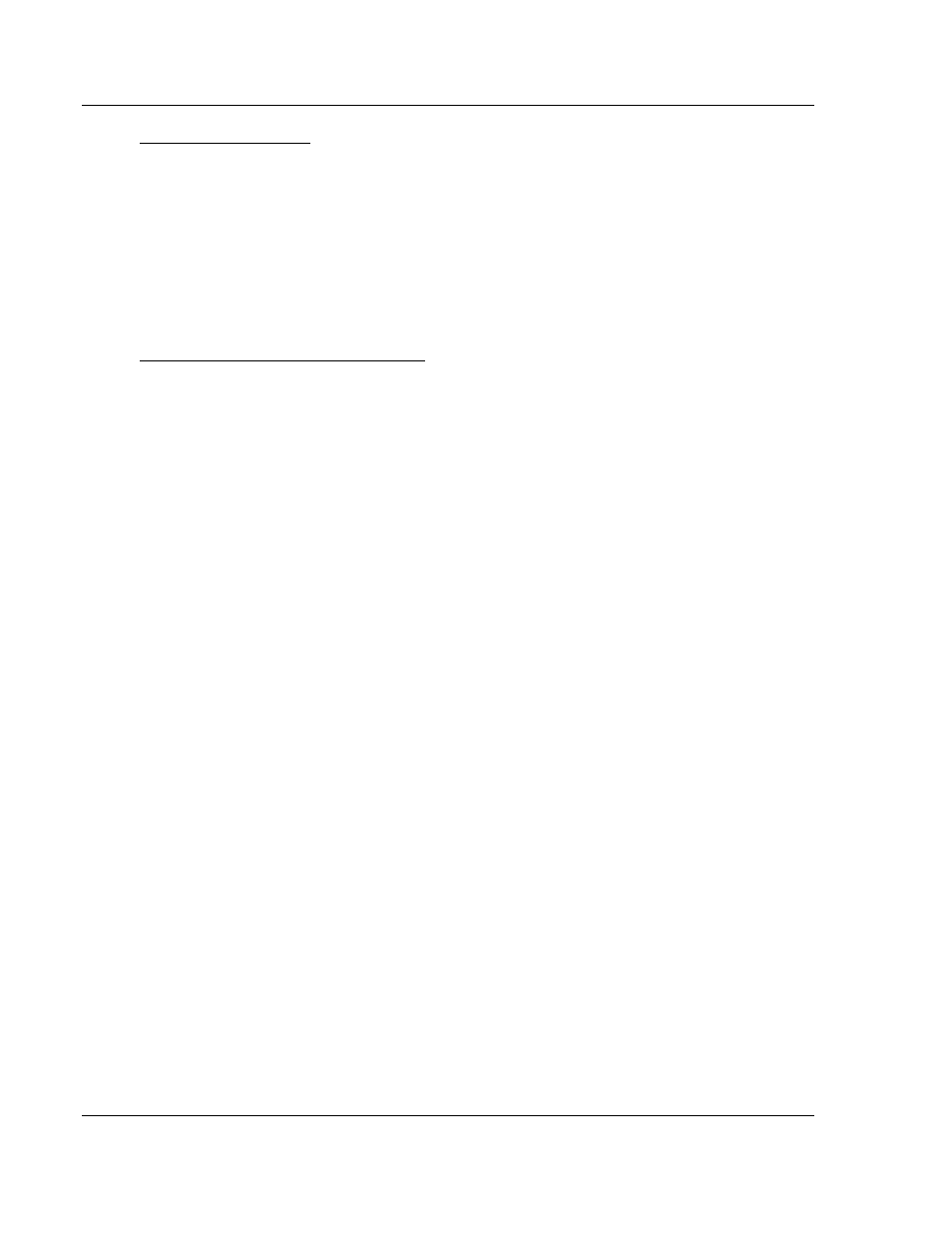
MVI56-PDPS ♦ ControlLogix Platform
Reference
Profibus DP Slave Communication Module
Page 60 of 88
ProSoft Technology, Inc.
April 22, 2008
Communication Types
In addition to point-to-point data transfer, the PROFIBUS protocol can also
handle the following types of communication:
Broadcast
communication:
An active node sends an unacknowledged message to all other nodes
(master and slaves)
Multicast communication (control instructions)
An active node sends an unacknowledged message to a group of nodes
(Master and Slaves).
Master/Slave Communication Phases
The communication between the Master and the Slaves takes place in the
following phases:
Parameterization and configuration phase
Usable data transfer phase
Before a DP Slave can be integrated into the usable data transfer phase, the
parameterization and configuration phase runs a device identification test that
verifies that the planned configuration matches the actual device configuration for
each slave in the PROFIBUS network. The test verifies that:
the device is actually there
it is the right type of device
the address, which is set on the device, matches the station address on the
bus
the formats, telegram length information, and bus parameters are correct
and
the number of configured inputs and outputs is correct.
5.2.4 Backplane Data Transfer
The MVI56-PDPS module communicates directly over the ControlLogix
backplane. Data is paged between the module and the ControlLogix processor
across the backplane using the module's input and output images. The update
frequency of the images is determined by the scheduled scan rate defined by the
user for the module and the communication load on the module. Typical updates
are in the range of 1 to 10 milliseconds.
This bi-directional transference of data is accomplished by the module filling in
data in the module's input image to send to the processor. Data in the input
image is placed in the Controller Tags in the processor by the ladder logic. The
input image for the module is set to 250 words. This large data area permits fast
throughput of data between the module and the processor.
The processor inserts data into the module's output image to transfer to the
module. The module's program extracts the data and places it in the module's
internal database. The output image for the module is set to 248 words. This
large data area permits fast throughput of data from the processor to the module