Appendix c - transducer electronic data sheets, Appendix c, Transducer electronic data sheets – Measurement Computing IOtech 640 Series User Manual
Page 93: Teds), Smart sensors
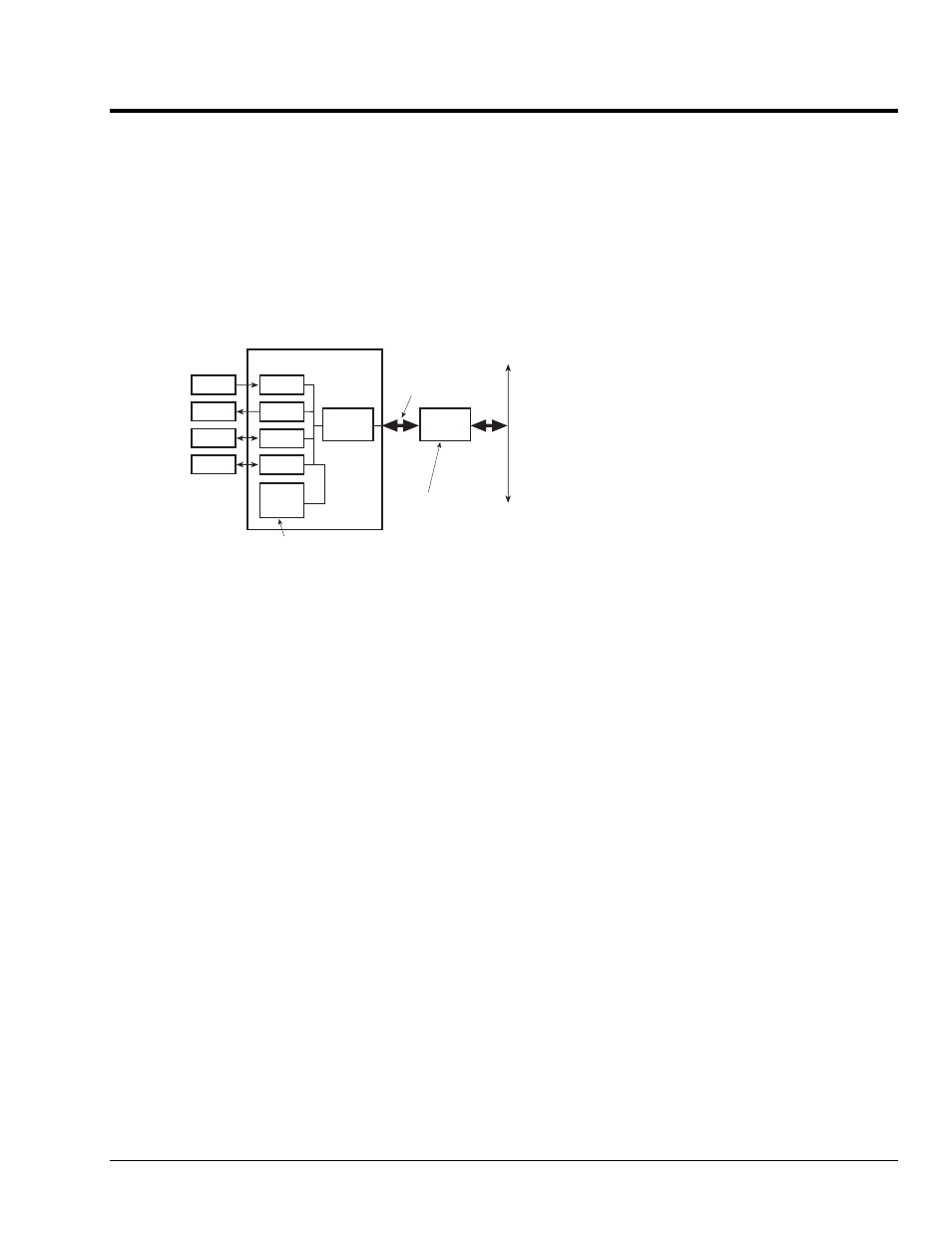
Appendix C
928693
TEDS C-1
Appendix C –
Transducer Electronic Data Sheets
(TEDS)
C
Smart Sensors
Certain types of transducers are classified as smart sensors. They contain a Smart Transducer Interface Module
(STIM), which in turn, contains an onboard EEPROM memory IC, called TEDS, Transducer Electronic Data Sheet.
(See Figure C.01.) The TEDS electronically stores information regarding the transducer’s characteristics and
parameters such as type of device, manufacturer, model number, serial number, calibration date, sensitivity,
reference frequency, and other data. The TEDS also stores the calibration coefficients and frequency response for a
transducer in terms of a table or an algorithm.
STIM
Transducer Electronic Data Sheet
XDCR
XDCR
XDCR
XDCR
ADC
DAC
DI/O
?
TEDS
(part 2)
Address
logic
NCAP
(part 1)
Network
Network-Capable
Application Processor
TII
Transducer
Independent
I/F
Fig. C.01. Three principal parts comprise smart sensor
systems: the Smart Transducer Interface Module STIM,
the Transducer Electronic Data Sheet TEDS, and the
Network-Capable Application Processor NCAP.
Not all sensor manufacturers provide this feature, but those that do are encouraged to follow an evolving standard,
IEEE 1451.0. One part of the standard, 1451.4, defines the TEDS format, channel identification formats, electrical
interface, and read and write functions for accessing the TEDS and transducer data. The specification also defines
the data set, that is, the number of samples acquired for one command that varies from 0 to 65,535 samples per set.
The standard does not specify requirements for signal conditioning, signal conversion, or how applications can use
the TEDS data. However, the signal conditioners and other interface hardware used with these smart sensors must
provide for an option or include circuits for TEDS communications under the direction of a software module
specifically intended for this purpose. Another special module that works with TEDS is usually part of the data
acquisition system’s application software package that collects, stores, and displays the measured variables. The
hardware automatically scales the readings and sets the range according to the data stored in the sensor. This is
typically done for each TEDS-associated channel.
TEDS capability was originally intended for piezoelectric sensors such as accelerometers and pressure sensors, but
it now includes all common analog sensors and actuators, such as MEMS (micro-electromechanical sensors),
accelerometers, pressure transducers, and temperature sensors with two-wire and mixed-mode (analog and digital)
input/output.
For two-wire analog sensors and actuators (called Class 1), the output signal is generally coupled to the signal
conditioner or driver while the TEDS data are enabled and read out with a dc bias voltage applied to the same two
wires. (See Figure C.02.) The transducers with mixed-mode capability (called Class 2) also communicate digitally
with the TEDS memory. (See Figure C.03.) The analog part is the signal representing the measured variable, and the
digital interface communicates with the embedded EEPROM. The TEDS architecture contains standard templates
for common transducers, and custom sub-templates that manufacturers can use for defining special parameters and
custom requirements.