Parr Instrument 6400 User Manual
Page 71
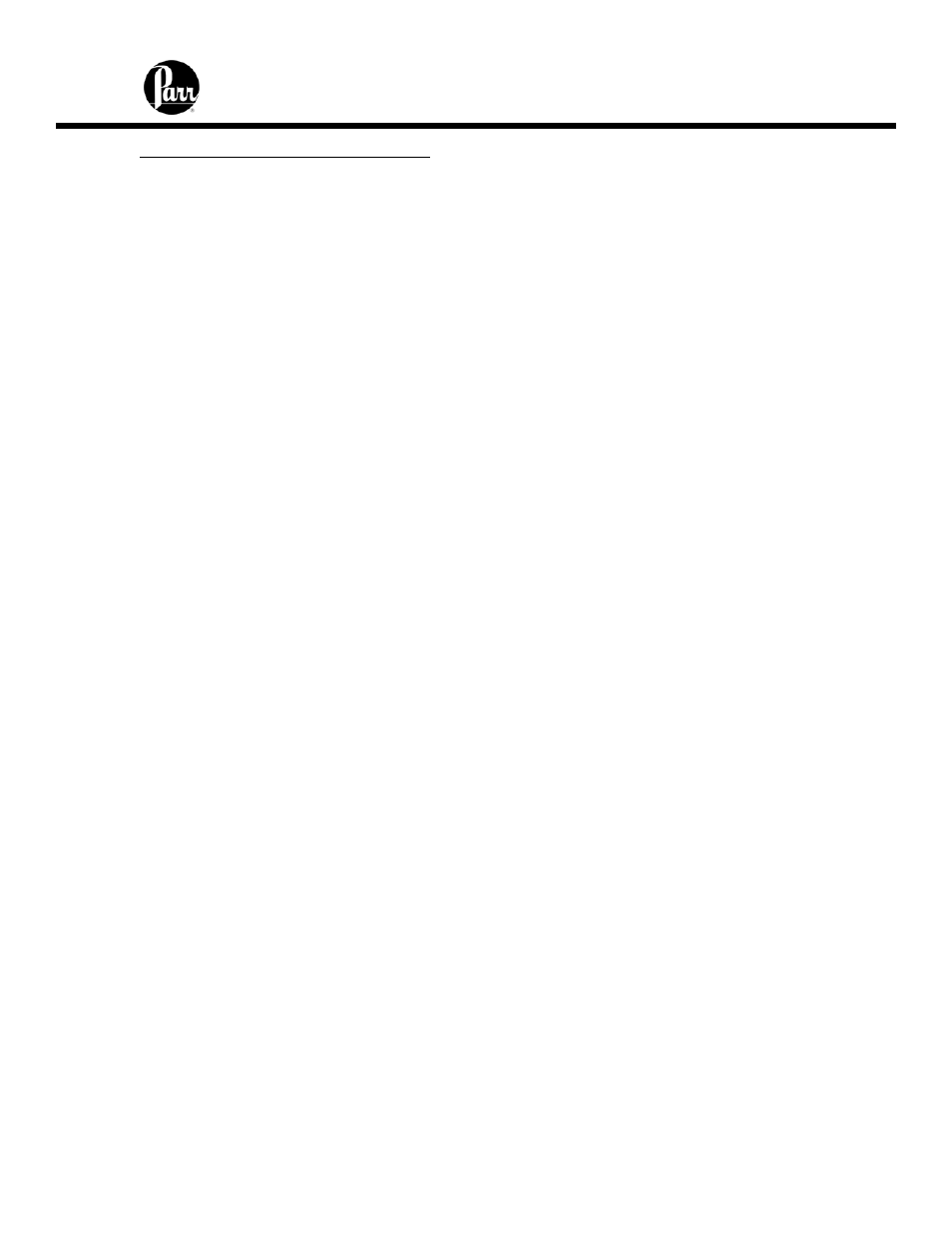
6400
Calorimeter Instruction Manual
10-2
Confirm function of the 966DD2 piston
In order to reduce the amount of time it takes to duplicate and troubleshoot this type of
situation, the I/O diagnostics can be used to pressurize and exhaust the bomb without
having to run lengthy combustion or pre-tests.
WARNING: This screen allows unconditional and arbitrary output control
for testing purposes. Be aware that all user and instrument protection is
disconnected while on this screen. This is very important and you should
take proper pre-caution.
1. Make sure the 668DD check valve is installed at the bottom of the cylinder.
2. Lock the head into the cylinder and close the calorimeter lid.
3. Confirm bomb release is off.
4. Turn bomb seal on then off to retract the 966DD2 piston.
5. Turn on O
2
fill to begin filling the bomb. The bomb will be completely filled in one
minute, at which time O
2
fill should be turned off. This seats the check valve in the
head which in turn seals the contents of the bomb.
6. The calorimeter lid can be unlocked at this time.
7. Activating bomb release should initiate a bomb exhaust within two seconds. If it takes
much longer than two seconds before the bomb begins to vent, then at least one of the
two following conditions outlined below exist.
8. If the bomb exhaust is initiated in a timely manner but fails to complete in 10
seconds, a blockage or restriction in the bomb exhaust circuit is indicated. This must
be investigated and corrected.
If the bomb fails to exhaust, the 1454DD funnel and 1453DD bomb cap adapter can
slowly be removed to release the pressure in the bomb. See Figure 26.
If the piston moves properly with no applied bomb pressure, but still fails to initiate an
exhaust of a pressurized bomb in a timely fashion, at least one of the following
conditions exist:
1. The 527VB restrictor is partially blocked.
2. The exhaust line is blocked.
3. There is a gas leak between the outlet of the solenoid and the 1140DD cylinder.
This also includes the 357HCJB o-ring seal on the piston inside of the cylinder.
The first condition can be eliminated by cleaning or replacing the 527VB restrictor.
The second condition can be eliminated by replacing the tubing and clearing all
connections.
The third condition can be eliminated by following the procedure outlined in the section
servicing the o-rings on the 966DD2 piston and carefully inspecting the 1/8 nylon
pressure hose and associated compression fittings for leaks while this circuit is
maintained at operating pressure, using the calorimeter I/O diagnostics. A minute leak
will result in a significant reduction in upward thrust.