Airplane model function descriptions – HITEC Optic 6 User Manual
Page 15
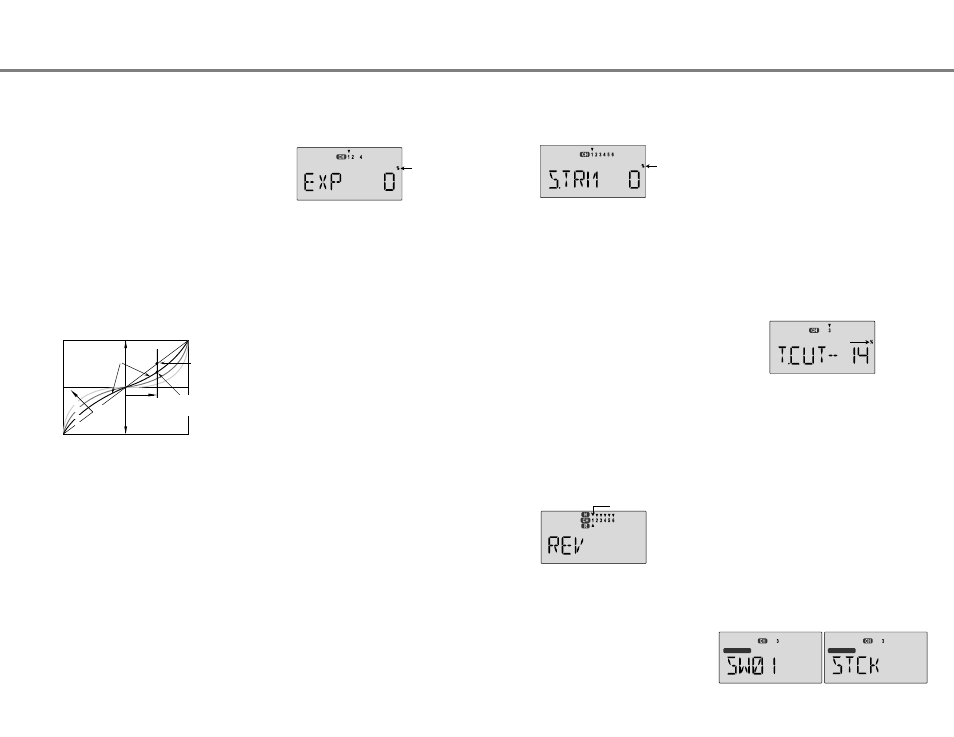
Airplane Model Function Descriptions
Airplane Model Function Descriptions
EXP - Exponential
S.TRM - Subtrim Settings
REV - Servo Reversing
STCK - Throttle Location
T.CUT - Throttle Cut (Engine Kill) Function
Setting Exponentials
3. Use the Data +Increase or -Decrease key to choose the
amount of dual rate for that switch position. You may set
the travel for both sides of the switch simply by flipping the
switch to the other position (the arrow will also switch sides).
If you wish to return to the original 100% value, press the
Active/Inhibit (Clear) key.
4. Press the Cursor Right key to move to another channel you
wish to input dual rate settings.
5. Repeat the first three steps for the dual rate settings on the
remaining channels. Note that you can leave one side of
the dual rate switches alone. This can be used for
exponential settings (see next function).
6. Return to the regular operating mode by pressing the two
Edit Up Down keys simultaneously.
1. Enter the programming mode by pressing the two Edit Up
Down keys (the two keys on the far left) at the same time.
Press either Edit Up Down key until the EXP menu appears,
as shown.
Setting Subtrims
Setting up the Throttle Cut function
1. Use the Edit Up Down keys to call up the STRM window.
Reversing Servos
The servo reverse function may be used when you need to
change the direction that a servo responds to a control stick
motion. When you use this function, BE SURE THAT YOUR
CONTROL IS MOVING THE CORRECT DIRECTION. If you
are using any preprogrammed mixers such as flaperon, be
sure to set correct travels in the REV menu setting up the
preprogrammed function.
1. Get to the REV screen with the Edit Up Down keys.
2. Use the Data +Increase or -Decrease key to select the
channel you wish to reverse. The active channel number
will flash.
Setting the Throttle Location
1. Use the Edit Up Down arrow keys to select the STCK window.
The window will either display the STCK display, indicating
the throttle stick controls channel 3, or the SW01 display,
indicating the switch controls it.
3. Toggle between normal (N) and reverse (R) with the Active/
Inhibit (Clear) key. The arrow above the number indicates
normal travel, while the arrow below indicates reversed
travel (the figure shows all channels normal, none reversed).
4. Repeat this procedure for each channel needing to be
reversed.
5. Return to the regular operating mode by pressing the two
Edit Up Down keys simultaneously.
Your Optic system has a unique feature that allows you to
choose whether the throttle control plugged into channel 3 is
activated by the throttle stick or by Switch SW01(the switch
labeled "Elev Rudd D/R" on the top left of the front of the
transmitter). If you are flying an electric-powered model or
some other model that only needs the throttle to be on or off,
you can use this function.
2. Press the Cursor Right or Left key until the small arrow is
above the channel you wish to adjust (the figure shows
subtrim adjustment for CH1).
3. Adjust the neutral position using the Data +Increase or
-Decrease keys. You may adjust between -100% and
+100%. If you want to reset the value back to zero, press
the Active/Inhibit (Clear) key.
4. Repeat steps 2 and 3 for each channel to be adjusted in turn.
5. Return to the regular operating mode by pressing the two
Edit Up Down keys simultaneously.
1. Get to the T.CUT screen with the Edit Up Down keys.
2. Place the throtle stick at its idle position (towards bottom of
transmitter). Use the Data -Decrease key to select the
amount of motion of the throttle servo you wish - normally
you want to completely close the carburetor, but be careful
not to choose too much travel that might stall the servo. You
may see the servo move when you press the Active/Inhibit
(Clear) button. A maximum of 50% may be chosen, but
only use the amount you need to fully close the carburetor
without stalling the servo.
3. Return to the regular operating mode by pressing the two
Edit Up Down keys simultaneously.
Note: the throttle servo will be disabled for a 2-3 second period after
the throttle cut button is pressed.
Note: The throttle cut function does not operate if Switch 01 controls
the throttle (see below).
The Throttle Cut function provides you an easy way to stop the
engine by simply pressing a button with the throttle stick at idle,
which commands the throttle servo to move a prescribed
amount. The throttle servo moves to the selected cut position
when the Cut button is pressed and the throttle stick is below
50%. Above 50% throttle, the cut button has no effect.
The activation direction may be chosen by the owner.
2. To set exponential for channel 1, move the arrow by pressing
the Cursor Right or Left keys repeatedly until the arrow is
over the channel number you want. Now switch the
appropriate switch up or down, noticing the position of the
arrow. You can set two values of exponential, one for each
switch position. By pressing the Data +Increase or
-Decrease keys, you can add or subtract from the numerical
value displayed. Note that you may pick a value anywhere
from -100% to +100%. If you quickly want to get back to the
default 0%, press the Active/Inhibit (Clear) key. You should
understand that you won't see changes in your model's servo
response unless you move the sticks. To get a feel for how
exponential works, just hold partial stick and switch the Expo
on and off (one side of the switch should be set to zero expo).
You'll see how it affects the servo travel.
3. The values you set for exponential are highly dependent on
both the model and pilot's preference. I normally recommend
a start value of about -10% to -20%, and many test flights,
slowly increasing the number until things are "right".
Obviously this depends on the pilot and model so go ahead
and fly it with Expo only on one side of the switch, turn it on
and off during flight, and change things to suit yourself. Or
don't use it at all if you don't like it - it's not for everyone.
4. Repeat this procedure for the expo settings on the other
remaining channels.
5. Return to the regular operating mode by pressing the two
Edit Up Down keys simultaneously.
The Subtrim window is used to make small adjustments or
corrections in the neutral position of each servo, independent of
the digital trim buttons. The recommended procedure is to zero
out both the trims (see settings menu) and the subtrims (this
menu). Then, one mounts the servo arms and sets up linkages
so that the neutral position of each control surface is as close to
where it should be as possible, with the arm 90° to the
pushrod. Finally, small amounts of subtrim are used to make
fine corrections. We recommend that you try to keep all of the
subtrim values of as small as possible. Otherwise, when the
You may be new to exponential settings. "Exponential" refers
to a mathematical function where the curve grows steeper the
further away from center it gets. Expo is a way to get the
effect of dual rates without having to flip a switch. The figure
below will help explain this concept.
You will notice that exponential has a smooth curve. For this
reason it is possible to have low sensitivity at low stick angles
(like dual rates), and yet have full motion at full stick deflection.
The Optic allows you to have two different values of
exponential, chosen by the same dual rate toggle switches on
the transmitter, described earlier. You might want to set a dual
rate at one switch position with zero exponential, and an
exponential value with 100% dual rate at the other. Then you
can switch between them in flight and decide which you like
better. Later, you can combine both dual rate settings and
exponential on a single switch setting.
There are really two kinds of exponential, "positive" and
"negative." Negative exponential is the one shown above, and
the type of expo most commonly used, where servo movement
is softer around neutral. Positive exponential is where the
servos are very sensitive around neutral and soft at extremes.
It is sometimes used for helicopter tail rotors.
The Optic allows you to set exponential for ailerons, elevator,
and rudder.
Servo
Response
Stick Motion
Exponential gives
smaller response for
same stick motion
around neutral
Normal
linear
response
Increasing
exponential
(shallower around
neutral)
0%
(Linear)
25%
50%
75%
Much less response
around neutral(compare
with Normal line)
subtrims are large values, the servo's full range of travel may
be restricted.
Flashing
Airplane Model Function Descriptions - Page 29
Airplane Model Function Descriptions - Page 28
INPUT SEL
INPUT SEL
Flashing
Flashing
Flashing "1"