A caution – Carrier 38E User Manual
Page 13
Attention! The text in this document has been recognized automatically. To view the original document, you can use the "Original mode".
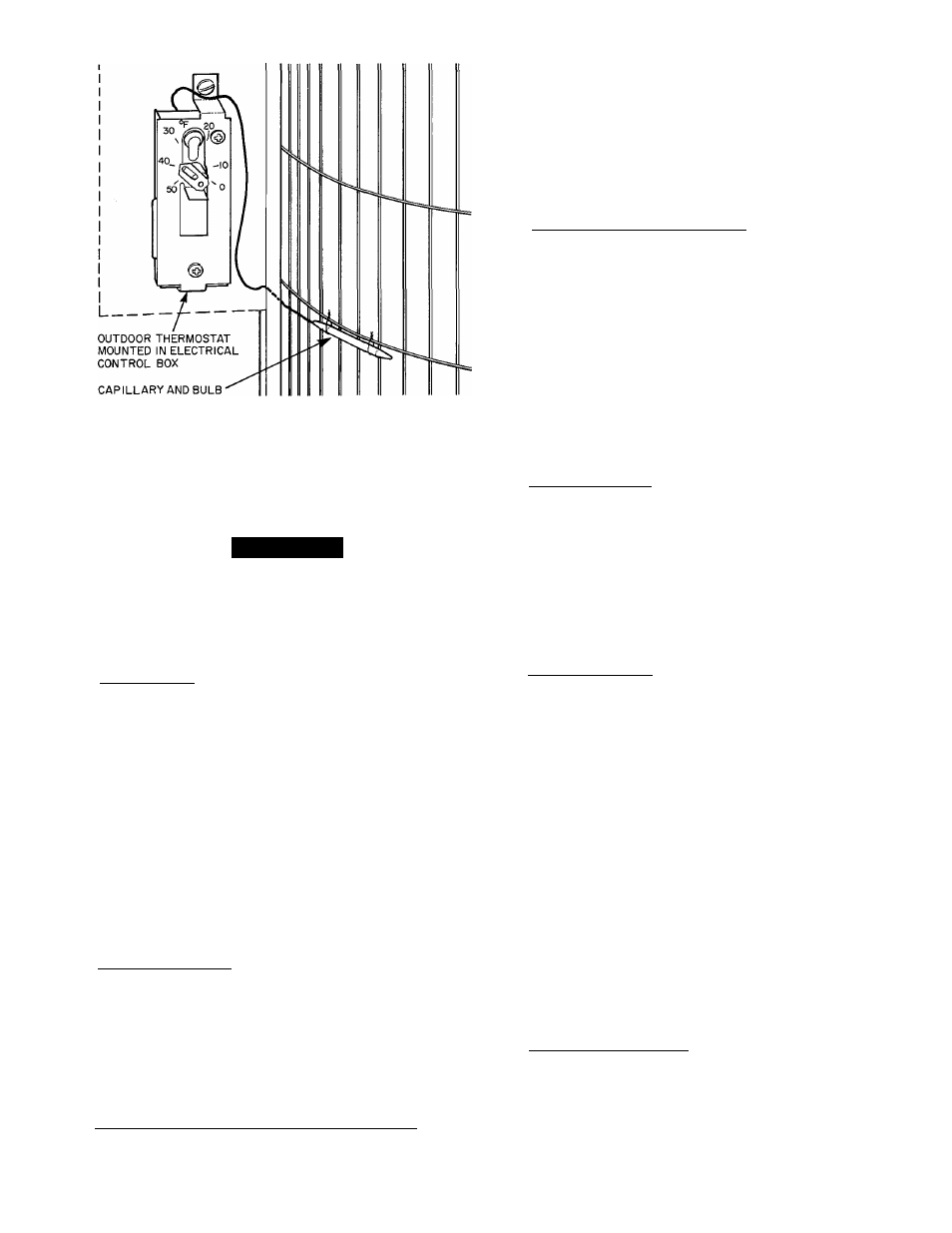
NOTES:
1. Affix capillary and bulb on outside of grille wire nearest control box.
2. Secure bulb to grille with wire ties or suitable fastener.
3. If necessary, shield bulb from direct sunlight using appropriate material.
Fig. 16 — Outdoor Thermostat Installation
A
CAUTION
Exercise extreme caution when reading compressor
currents, as high-voltage power is on. Correct any of
the problems described below before installing and
running a replacement compressor. Wear safety
glasses and gloves when handling refrigerants.
Locked Rotor — In this type of failure, compressor
motor and all starting components are normal. When
compressor attempts to start, it draws locked rotor
current and cycles off on the internal protection. Locked
rotor current is measured by applying a clamp-on
ammeter around common lead of the compressor on a
single-phase compressor, or any one of the leads on a
3-phase compressor. Then measure current it draws when
it attempts to start. LRA (locked rotor amp value) is
stamped on compressor nameplate.
If compressor draws locked rotor amps, and all other
external sources of problems have been eliminated,
compressor must be changed. Because compressor is a
sealed unit, it is impossible to determine exact mechanical
failure. However, complete system should be checked for
abnormalities such as incorrect refrigerant charge,
restrictions, insufficient airflow across indoor or outdoor
coil, etc., which could be contributing to the failure.
Runs, Doesn't Pump — In this type of failure, compres
sor motor runs and turns compressor, but compressor
does not pump the refrigerant. A clamp-on ammeter on
common leg of a single-phase compressor, or any one
lead of a 3-phase compressor, shows a very low current
draw, much lower than RLA (rated load amps) value
stamped on compressor nameplate. Because no refrig
erant is being pumped, there is no return gas to cool
compressor motor. It eventually overheats and shuts off
on its internal protection.
Runs — Doesn’t Pump, High-To-Low Side Leak — This
failure is similar to previous one except compressor is
pumping. Usually, an internal problem such as blown
head gasket or broken internal discharge line causes
compressor to pump hot discharge gas back into its own
shell rather than through system.
Using pressure gages on service valves shows high
suction and low discharge pressure readings. Motor
currents are lower than normal. Because hot gas is being
discharged into shell, the shell becomes hot. The hot
gas causes compressor motor to cycle off on its internal
protection.
Runs and Pumps, Low Capacity — This failure type is
difficult to pinpoint because extent of damage varies.
Compressor is a pump with internal valves that enable
compressor to pump properly. On multicylinder com
pressors, each cylinder has a complete set of suction and
discharge valves. Any of these parts may become
damaged or broken causing loss in pumping capacity.
Severity of damage determines amount of capacity loss.
Use pressure gages to find any abnormal system pressures
if system charge and other conditions are normal.
An owner may complain that a unit is not handling the
building’s heating or cooling load. The compressor
current draw may be abnormally low or high. Although
this type of failure does occur, all other possible causes of
capacity loss must be eliminated before condemning
compressor.
Noisy Compressor— May be caused by variety of inter-
nal problems such as loosened hardware, broken
mounting springs, etc. May also be caused by system
problems. Overcharging a compressor causes operating
noise, particularly at start-up. Certain single-cylinder
compressors are noisy at start-up and may operate
noisily. Too much oil in compressor may cause noise.
Normally this problem is encountered only after a
replacement compressor has been added, without purging
oil from previous compressor. As new compressor
pumps, excess oil in system returns and adds to volume
already present, causing noise.
Compressor Leaks — Sometimes a leak is detected at
weld seam around girth of compressor, or a fitting that
joins compressor shell. Many of these leaks can be re
paired and the compressor saved if correct procedure is
followed. Turn off all power to unit. Remove all refrig
erant from system so that gage pressure is 0 psi. Use safety
glasses and gloves when handling refrigerants. Clean area
around leak to bare metal. Apply flux and repair joint
with silver solder. Do not use low-temperature solder
such as 50-50. Clean off excess flux, check for leaks, and
apply paint over repaired area to prevent corrosion.
Do not use this method to repair a compressor leak due
to severe corrosion. Never attempt to repair a compressor
leaking at electric terminals. This type of failure requires
compressor replacement.
ELECTRICAL FAILURES — The compressor me
chanical pump is driven by an electric motor within
hermetic shell. In electrical failures, compressor does not
run although external electrical and mechanical systems
appear normal. Compressor must be checked electrically
for abnormalities.
Before troubleshooting compressor motor, review this
description of compressor motor terminal identification.
Single-Phase Motors — See Fig. 17. To determine ter
minals C, S, and R: Turn off all unit power. Short the run
(and start) capacitor to prevent shock. Remove all
wires from motor terminals. Using an ohmmeter on
0-10 ohm scale, read resistance between all pairs of
terminals. Determine 2 terminals that provide greatest
resistance reading. Through elimination, remaining
13