0 uncrating and preparation (cont'd), 2 preparing the furnace for installation (cont'd) – Reznor EEDU Unit Installation Manual User Manual
Page 6
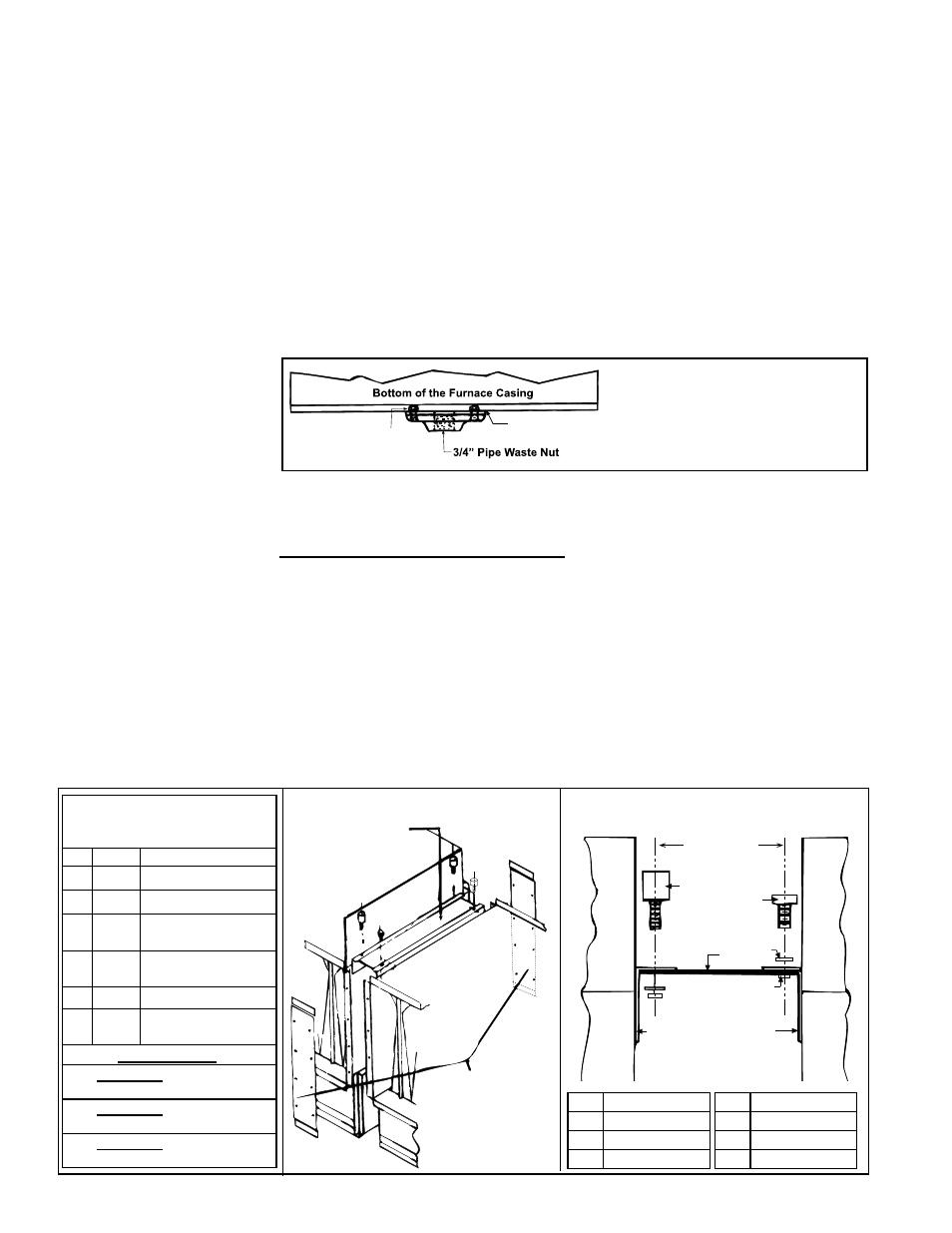
Form I-EEDU, Page 6
3.0 Uncrating and
Preparation
(cont'd)
3.2 Preparing the
Furnace for
Installation
(cont'd)
FIGURE 3 - Condensate
Drain, Option CS1
(P/N 31765)
Seal holes in bottom pan with RTV
sealant. Terminate drain outside of
building. Periodic cleaning of the
condensate collector and disposal
system is required.
3.2.3 Install Condensate
Drain, Option CS1
RTV Sealant
#10-32 x 1”Lg
Machine Screw
& Nut
Condensate can form in the heat exchanger of furnaces installed as makeup air units
or when installed downstream from a cooling coil. Under these conditions, a drain
flange, Option CS1, may be installed on the furnace bottom as shown in
FIGURE 3.
When using Option CS1, seal all corners and the four square holes in the bottom pan
edge.
NOTE: A 4-inch (102mm) minimum clearance is required under the furnace if a
90° street elbow is used.
3.2.4 Coupling Two,
Three, Four, or Five
Furnaces
Coupling of furnaces is done using optional coupling kits -- Option CR1 for two units,
Option CR2 for three units, Option CR3 for four units, or Option CR4 for five units.
Refer to the illustrations and follow the instructions.
Instructions for Coupling Furnaces (Refer to FIGURES 4A, 4B, 4C, 4D)
1. Position tie plate below hanger angle. Attach the tie plate to the first furnace
using threaded socket assemblies. Secure fasteners firmly.
2. Move the second furnace next to the first furnace. Position so that the tie plate
is below the hanger angle. Secure the tie plate to the hanger angle using the
3/8-16 bolts, the washers, and the spotweld nuts on the tie plate.
3. Position the filler plates to furnaces as shown in FIGURE 4A. Using a filler plate
as a template, drill 1/8" diameter holes. Attach filler plates using the sheetmetal
screws provided. Offset of filler plate allows alignment with unit duct flanges. See
FIGURE 4C.
4. Coupled units require access panels in the top or bottom of the outlet duct for limit
control service. See
FIGURE 4D and Paragraph 6.3.4.
Filler
Plates
Tie-Plate must
be below the
hanger angles.
See FIGURE 4B.
FIGURE 4A - Coupling Furnaces
1
2
3
5
6
7
4 (102mm)
7
Unit
1
Unit
2
FIGURE 4B - Installing Coupling Kit
Tie Plate
Coupling Kit Components,
Option CR1 (P/N 57963), for
Two Furnaces
Qty
P/N
Description
2
57964 Filler Plate
1
57965 Tie Plate
2
9557 Threaded Socket
Assembly
2
5095 3/8-16 x 1-1/4" lg Hex
Head Bolts
2
5197 Split Ring Lock Washer
20
11813 #10 x 1/2" lg
Sheetmetal Screws
Additional Kits:
3 Furnaces - Option CR2
(P/N 82654)
4 Furnaces - Option CR3
(P/N 82655)
5 Furnaces - Option CR4
(P/N 82656)
Item Description
1 Socket Assembly
2 Bolt
3 Lockwasher
Item Description
5 Spotweld Nut
6 Tie Plate
7 Hanger Angles
Tie plate (6)
MUST
be under
both hanger
angles (7).
b) With the limit control on the heat exchanger side of the bracket, slide the limit
control/bracket assembly into the hole. Attach the bracket with two sheetmetal
screws.
c) Cover all of the original factory-made limit control holes with a field-supplied
sheetmetal plate. Do not leave any open holes in the side panel or the heat
exchanger bottom.
4. The furnace is now ready for installation with the airflow from front to rear (gas valve
side).
3.2.2 Instructions for Reversing Airflow (cont'd)