Section 6 - calibration and diagnostic menus, 2 calibration procedures, 1 stepper feedback calibration – AERCO C-More Controls User Manual
Page 37: 2 pwm in adjustment, 3 analog in adjustment, C-more control panel operation
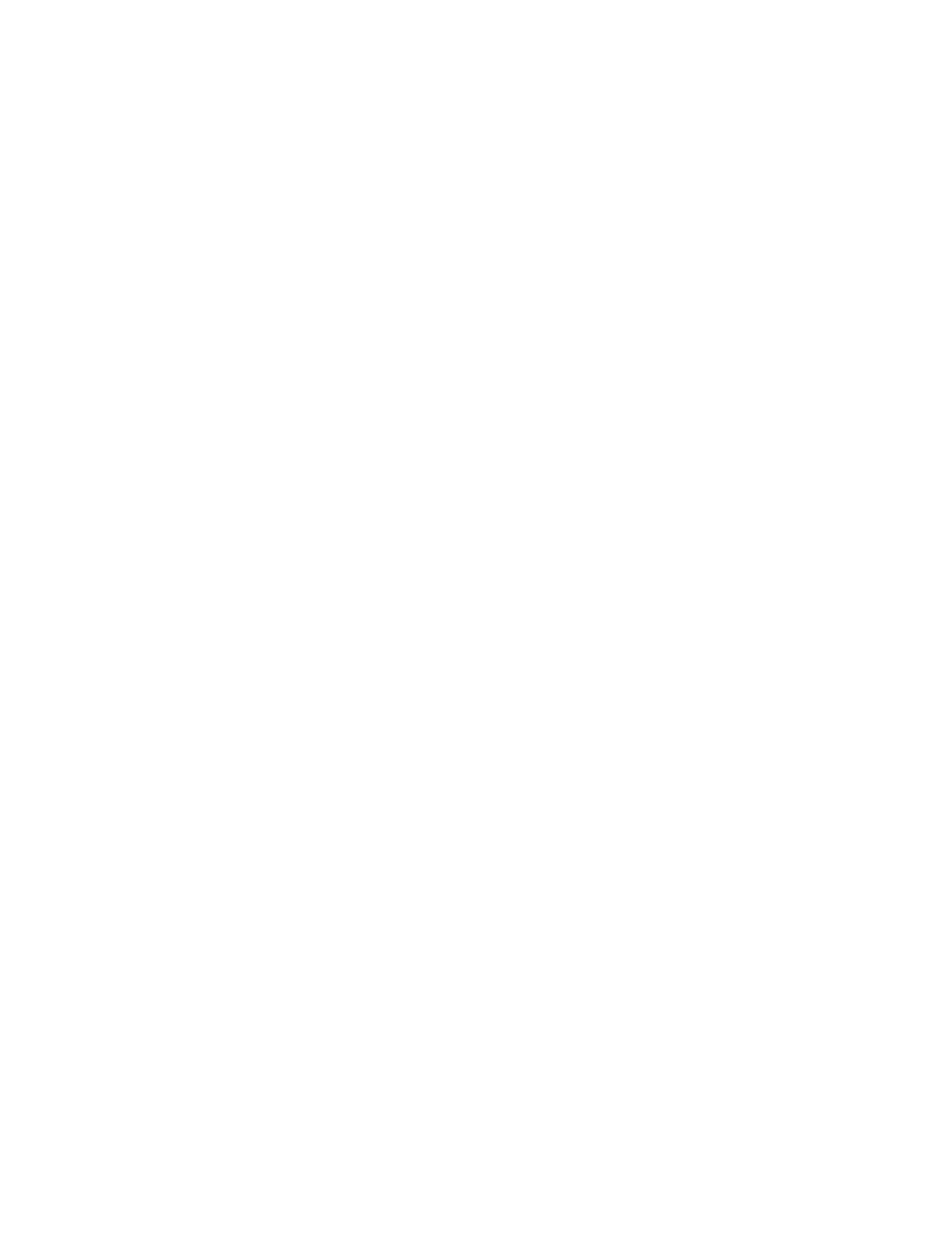
C-MORE CONTROL PANEL OPERATION
SECTION 6 -
CALIBRATION AND DIAGNOSTIC MENUS
6.1 INTRODUCTION
The Level 2 Password (6817) must be entered
to access the Calibration and Diagnostic
procedures describe in this Section.
6.2 CALIBRATION PROCEDURES
The items contained in the Calibration Menu
shown in Table 2-5 permit the user to set or
adjust a number of functions in the KC and
Benchmark Series units. The descriptions and
procedures necessary to implement each of
these Calibration Items are provided in the
following paragraphs.
6.2.1 Stepper Feedback Calibration.
The Stepper Feedback (Fbk) function checks
the calibration of the Air/Fuel Valve Stepper
Motor feedback current. This is accomplished by
positioning the Air/Fuel Valve stepper motor at
the 0% (fully closed) and 100% (fully open)
positions and storing the feedback potentiometer
readings at these settings. It also permits
verification of the Stepper Motor Feedback at
the 50% position. The position of the Stepper
Motor is verified by visually checking the dial on
the Air/Fuel Valve. In addition, the FIRE RATE
bargraph segments will light to indicate motor
position. To initiate this calibration procedure,
proceed as follows:
1. Press the ▲ or ▼ arrow key until Stepper
Fbk
Cal 0% is displayed.
2. Press the CHANGE key. Stepper Fbk will
begin to flash.
3. Press and hold the ▼ arrow key and monitor
the dial on the Air/Fuel Valve.
4. Release the ▼ arrow key when the Air/Fuel
Valve reaches the 0% (fully closed) position,
but is not pressing against the stop.
Momentarily tap the ▲ arrow key a few times
to ensure it is not contacting the stop.
5. Press the ENTER key. Cal 100% will be
displayed.
6. Press and hold the ▲ arrow key and monitor
the dial on the Air/Fuel Valve.
7. Release the ▲ arrow key when the Air/Fuel
Valve reaches the 100% (fully open) position,
but is not pressing against the stop.
Momentarily tap the ▼ arrow key a few times
to ensure it is not contacting the stop.
8. Press the ENTER key. Verify 50% will be
displayed and the Air/Fuel Valve will rotate to
the 50% position.
9. Verify that the dial on the Air/Fuel Valve
indicates approximately 50%. Press ENTER
to confirm.
10. Press BACK to exit the Stepper Fbk
Calibration.
6.2.2 PWM In Adjustment.
The Pulse Width Modulation (PWM) Input
Adjustment is used when the unit is being
controlled by a Boiler Management System
(BMS). This Calibration procedure allows the
PWM duty cycle to be varied ±5.0% in 0.1%
increments. The nominal PWM duty cycle is 12
milliseconds where: a 5% pulse ON time = a 0%
firing rate and a 95% pulse ON time represents
a 100% firing rate. To adjust the overall PWM
duty cycle, proceed as follows:
1. Press the ▲ or ▼ arrow key until PWM In
Adj
is displayed along with the currently
entered adjustment percentage.
2. If the desired percentage is not displayed,
press the CHANGE key. PWM In Adj will
begin to flash.
3. Press the ▲ or ▼ arrow key to increment or
decrement the display until the desired
adjustment percentage is displayed.
4. Press ENTER to store the selection.
5. Pres BACK to exit the adjustment procedure.
6.2.3 Analog In Adjustment
The Analog Input Adjustment may be utilized
when an external signal is used to change the
setpoint (Remote Setpoint Mode – Boiler or
Heater), or drive the firing rate Direct Drive
Mode – Boiler Only). This adjustment allows the
0 to 20 mA or 1 to 5 Vdc input to be changed
±5.0% in 0.1 % increments. The default setting
is 0.0%. To view or change this adjustment,
proceed as follows:
33