0 calibration – Cooper Instruments & Systems ELF 4200 Flexiforce Paper Thin Sensor User Manual
Page 34
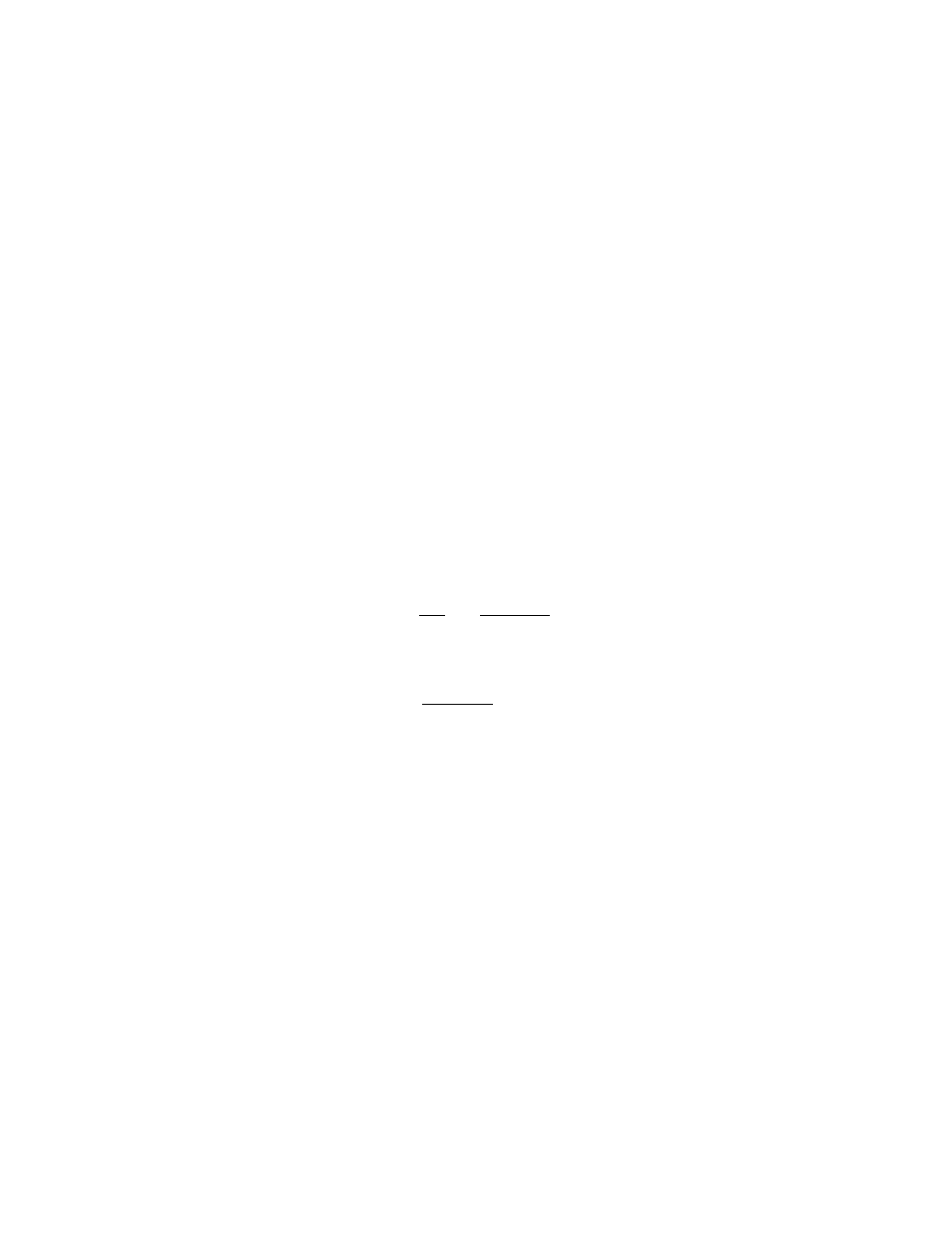
CF10
31
6/24/08 Rev. H
load path goes through this area. The puck must not touch any of the edges of the sensing area, or these edges
may support some of the load and give an erroneous reading.
The FlexiForce sensor reads forces that are perpendicular to the sensor plane. Applications that impart "shear"
forces could reduce the life of the sensor. If the application will place a "shear" force on the sensor, it should be
protected by covering it with a more resilient material.
If it is necessary to mount the sensor to a surface, it is recommended that you use tape, when possible. Adhesives
may also be used, but make sure that the adhesive will not degrade the substrate (polyester) material of the sensor
before using it in an application. Adhesives should not be applied to the sensing area; however, if it is necessary,
ensure that the adhesive is spread evenly. Otherwise, any high spots may appear as load on the sensor.
5.2 SATURATION
The Saturation force is the point at which device output no longer varies with applied force. The saturation force of
each sensor is based on the maximum recommended force specified by Cooper Instruments, which is printed on
system packaging or the actual sensor, along with the "Sensitivity".
Sensors are available in three force ranges (Low, Medium, and High), which have specified maximum forces of
25, 150, and 1000 lbf, respectively. The sensor’s effective force range (up to the specified maximum) can be
altered by adjusting the system sensitivity (refer to the Calibration section). Decreasing the sensitivity setting (1 to
20 possible) will increase the force range (displayed as "Approx Max Range"), and "saturation" force, of the sensor,
and vice versa.
It is essential that the sensor(s) do not become saturated during testing.
5.3 CONDITIONING SENSORS
Exercising, or Conditioning a sensor before calibration and testing is essential in achieving accurate results from
your ELF system. It helps to lessen the effects of drift and hysteresis. Conditioning is required for new sensors, and
for sensors that have not been used for a length of time.
To condition a sensor, place 110% of the test weight on the sensor, allow the sensor to stabilize, and then remove
the weight. Repeat this process four or five times. The interface between the sensor and the test subject material
should be the same during conditioning as during calibration and actual testing.
IMPORTANT! Sensors must be properly conditioned prior to calibration and use.
6.0 CALIBRATION
The ELF system sensor acts as a variable resistor in a circuit. This circuit produces a digital output value (between
0-255 Raw) based on the sensor resistance and the system handle’s adjustable gain (sensitivity). Calibration is
the method by which this digital output is related to an actual engineering unit, such as pounds or Newtons. If you
are using the Multi-Handle ELF system, all selected COM ports must be calibrated with at least one point before
Calibration can be completed.
To calibrate, apply a known force to the sensor. The software then equates this applied force to the digital output
that it reads, and performs a linear interpolation between zero load and the known calibration load. In this way, the
software determines the actual force range that matches the digital output range of 0-255 Raw.
To perform a multi-point calibration, apply at least two known forces to a sensor. The software then equates this
applied force to the digital output that it reads, and performs one of two types of interpolation between zero load
and the known calibration loads. In this way, the software determines the actual force range that matches the digital
output range of 0-255 Raw.
• Best Fit Linear Calibration: This calibration creates a best-fit curve through two known force values. After a
known load is added as a calibration point, select the Params button for details about the calibration, including
slope, offset and Correlation Coefficient (r2).