Using analog output modules – Rockwell Automation 1794 FLEX I/O System with ControlLogix for SIL2 User Manual
Page 35
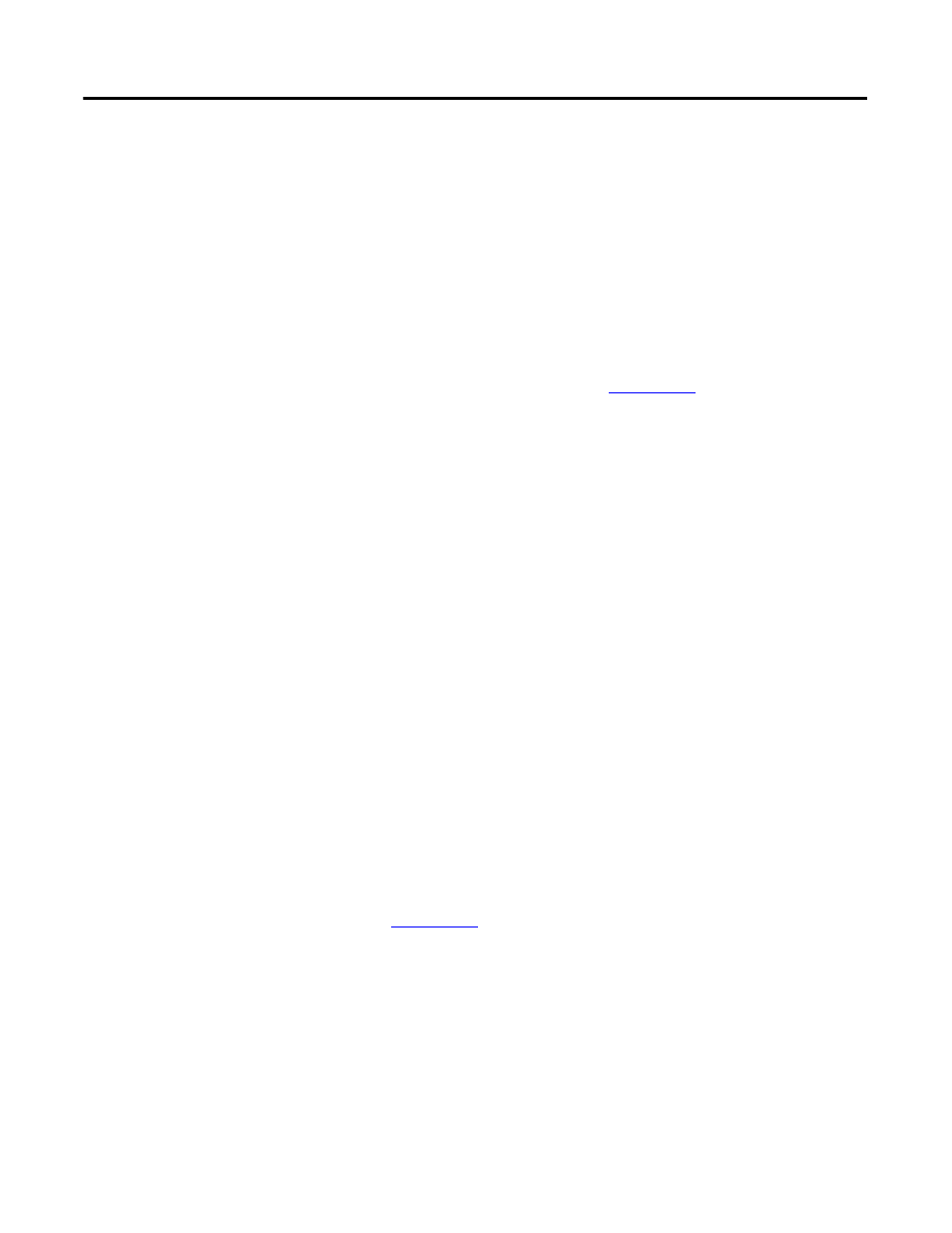
Publication 1794-RM001G-EN-P - December 2011
FLEX I/O Modules 3-13
Using Analog Output
Modules
General Considerations when using Any FLEX I/O Analog Output
Module
There are a number of general application considerations that you must follow
when applying the analog output modules in a SIL2 application:
•
Proof Tests - Periodically (for example, once every several years) a
System Validation test must be performed. Manually, or automatically,
test outputs to make sure that all outputs are operational. Channel data
should be varied over the full operating range to make sure that the
corresponding field signal levels vary accordingly. For additional
information
•
Calibrate Outputs Periodically, As Necessary: FLEX I/O modules
ship from the factory with a highly accurate level of calibration.
However, because each application is different, users are responsible for
making sure their FLEX I/O modules are properly calibrated for their
specific application.
Users can employ tests in application program logic to determine when
a module requires recalibration. For example, to determine whether an
output module needs to be recalibrated, a user can determine a tolerance
band of accuracy for a specific application. The user can then measure
output values on multiple channels and compare those values to
acceptable values within the tolerance band. Based on the differences in
the comparison, the user could then determine whether recalibration is
necessary.
Calibration (and subsequent recalibration) is not a safety issue.
However, we recommend that each analog output be calibrated at least
every 3 years to verify the accuracy of the input signal and avoid
nuisance application shutdowns.
•
For typical emergency shutdown (ESD) applications outputs must
be configured to De-energize: When configuring any FLEX I/O
output module, each output must be configured to de-energize in the
event of a fault and in the event of the controller going into program
mode. For exceptions to the typical ESD applications, see publication