Rockwell Automation 1746-QS,D17466.19 SYNCHRONIZED AXES MODULE User Manual
Page 24
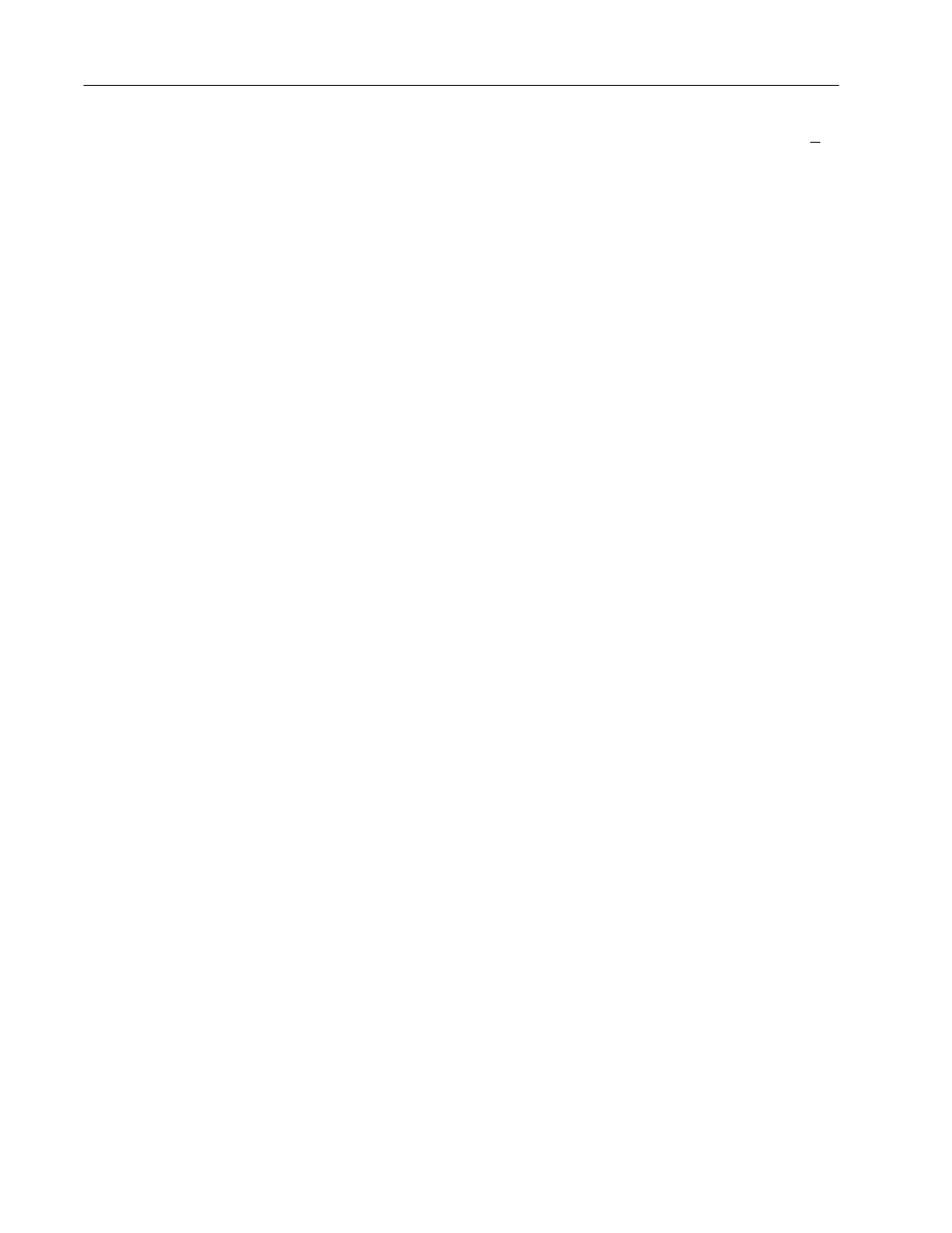
4–8
Publication 1746-6.19 March 1998
Important: When tuning the Feedforward term with command “F”,
plot sequential axis moves and compare plots of target position and
actual position until the two plots coincide.
Another way to adjust these parameters is to set the
DIFFERENTIAL
GAIN
and
INTEGRAL GAIN
to zero and the
PROPORTIONAL GAIN
to a small value (between 1 and 5), then make long slow moves in
both directions.
Adjust the
EXT FEEDFORWARD
and
RET FEEDFORWARD
until the
axis tracks within 10% in both directions. In hydraulic systems, the
EXTEND
and
RETRACT FEEDFORWARD
terms typically differ by
the ratio of the extend and retract piston areas.
Alternately, you can find the appropriate value for the
FEEDFORWARD
terms by making moves with the axis at a SPEED of 1,000. The
amount of output drive required to maintain this
SPEED
is the correct
value for the
FEEDFORWARD
parameter.
Using Acceleration Feedforwards
The
ACCELERATION FEEDFORWARD
terms are particularly useful for
axes which move large masses with relatively small cylinders. This
combination delays the start of movement, and the
ACCELERATION
FEEDFORWARD
terms can help compensate for this delay.
ACCELERATION FEEDFORWARDS
are easiest to adjust with the PID
gains set low. After commanding a move, plot it using Hydraulic
Configurator and look for a following error during the acceleration.
Increase the
ACCELERATION FEEDFORWARD
until the error is
minimized. For large masses the
ACCELERATION FEEDFORWARD
can
be in the tens of thousands.
Important: When tuning acceleration feedforward terms, you can
plot multiple axis moves and observe the Sum-Error
2
value found in
the window on the plot screen. Repeat axis moves and adjust this
term until the Sum-Error
2
value reaches a minimum.
Adjusting P-I-D Gains
PROPORTIONAL GAIN
affects the responsiveness of the system.
Low gains make the system sluggish and unresponsive. Gains that
are too high make the axis oscillate or vibrate. You can adjust the
PROPORTIONAL GAIN
by slowly increasing it and moving the axis.
When you see a tendency to oscillate as the axis moves or stops,
reduce the gain by 10 to 30 percent.