Pegasus user’s guide – Orbital Pegasus User Manual
Page 72
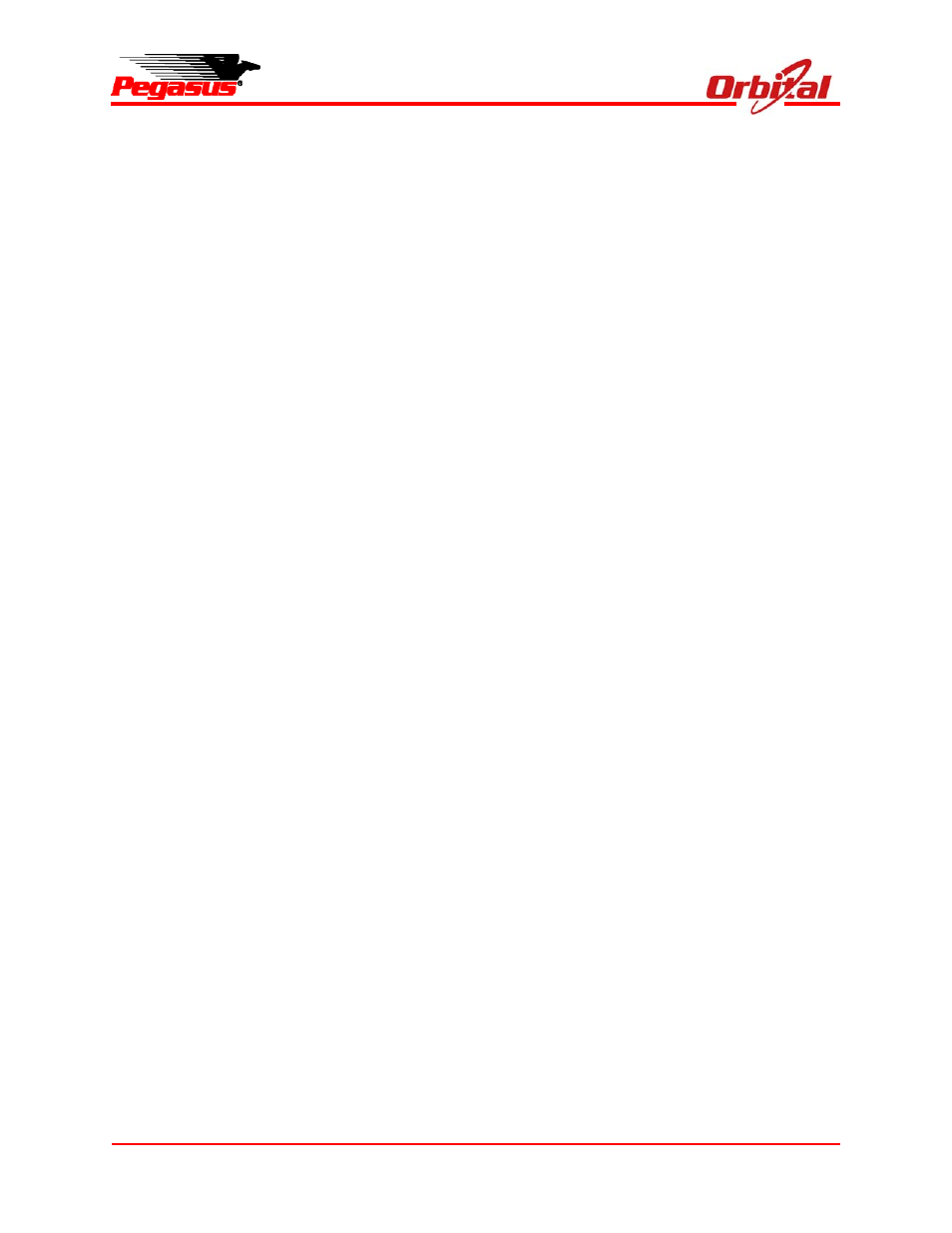
Release 7.0
Apr 2010
61
Pegasus User’s Guide
tube truck is disconnected. Ground nitrogen is
continually supplemented by a tube truck, so
capacity limitations are generally not a problem.
The payload purge can be routed directly to the
payload interior via a quick disconnect device as
an additional mission-unique optional service. The
quick disconnect exerts less than 50 lbf on the
payload fitting. Back pressure must be limited to
10 psig when the purge gas is plumbed directly
into a payload supplied device.
All fairing nitrogen systems receive nitrogen via a
manifold installed in fairing near the split line.
Fairing and/or payload purge lines can be installed
on the right or left half of the fairing. Nitrogen lines
can generally be routed to accommodate payload
requests, however, they cannot cross the fairing
split line.
10.10. Increased Capacity Payload-to-GSE
Interface
Authorize by: L-24 months
Orbital can incorporate 40 additional circuits (20
shielded twisted wire pairs) from the payload
interface to payload-provided ASE installed in the
carrier aircraft. This harnessing is routed to the LV
0º connector at the separation plane. This wiring
matches the specifications of the standard pass-
through pairs: 22 gauge wire, 90% shielding, 2.5
ohms resistance, and a maximum carrying
capability of 3.0 A per wire pair. The 40 circuits
replace the standard 3 separation loopback
circuits at this connector (if desired, the payload
may elect to retain the 3 separation loopback
circuits in this connector and use 34 circuits for
spacecraft to ASE connectivity). Because
additional harnesses are added to the launch
vehicle, there is an approximately 2.7 kg (6 lbm)
performance to orbit penalty associated with this
nonstandard service
The 40 circuits of the nonstandard service are
routed to the LPO Station or to a floor box
connector in the carrier aircraft. Orbital will
support the installation of a payload-provided
standalone ASE rack in the carrier aircraft as part
of this nonstandard service. This significantly
increases the ASE that may be installed on the
carrier aircraft. Orbital will assist the payload in
securing FAA certification of the ASE rack.
The added pass-through circuits and payload ASE
will be documented on the mission-specific EICD.
10.11. Improved Insertion Accuracy Options
Authorize by: ATP
As a nonstandard service, an integral liquid fourth
stage called the Hydrazine Auxiliary Propulsion
System (HAPS), shown in Figure 10-1, can be
provided on Pegasus.
Located inside an extended Pegasus avionics
structure, HAPS is a monopropellant hydrazine
propulsive system, which functions in blowdown
mode. HAPS consists of a flight proven and
EWR-127-1 qualified titanium propellant tank,
three 45 lbf nominal Rocket Engine Assemblies
(REA), and a redundantly initiated pyrotechnic
isolation valve.
Being a liquid stage, the accuracy achievable by
HAPS is limited only by the accumulated
navigation errors during flight, which are
dependent on the mission time line and trajectory
chosen. In addition to improving accuracy, HAPS
will also improve performance to altitudes above
approximately 550 km (highly dependent on orbital
requirements).
The additional length of the HAPS avionics section
moves the payload interface plane forward by
10.45" relative to the standard 38" or 23" payload
adapters. This reduces the available payload
volume and increases the payload random
vibration and acceleration levels. The addition of
a separation system between the Stage 3 motor