Pegasus user’s guide – Orbital Pegasus User Manual
Page 32
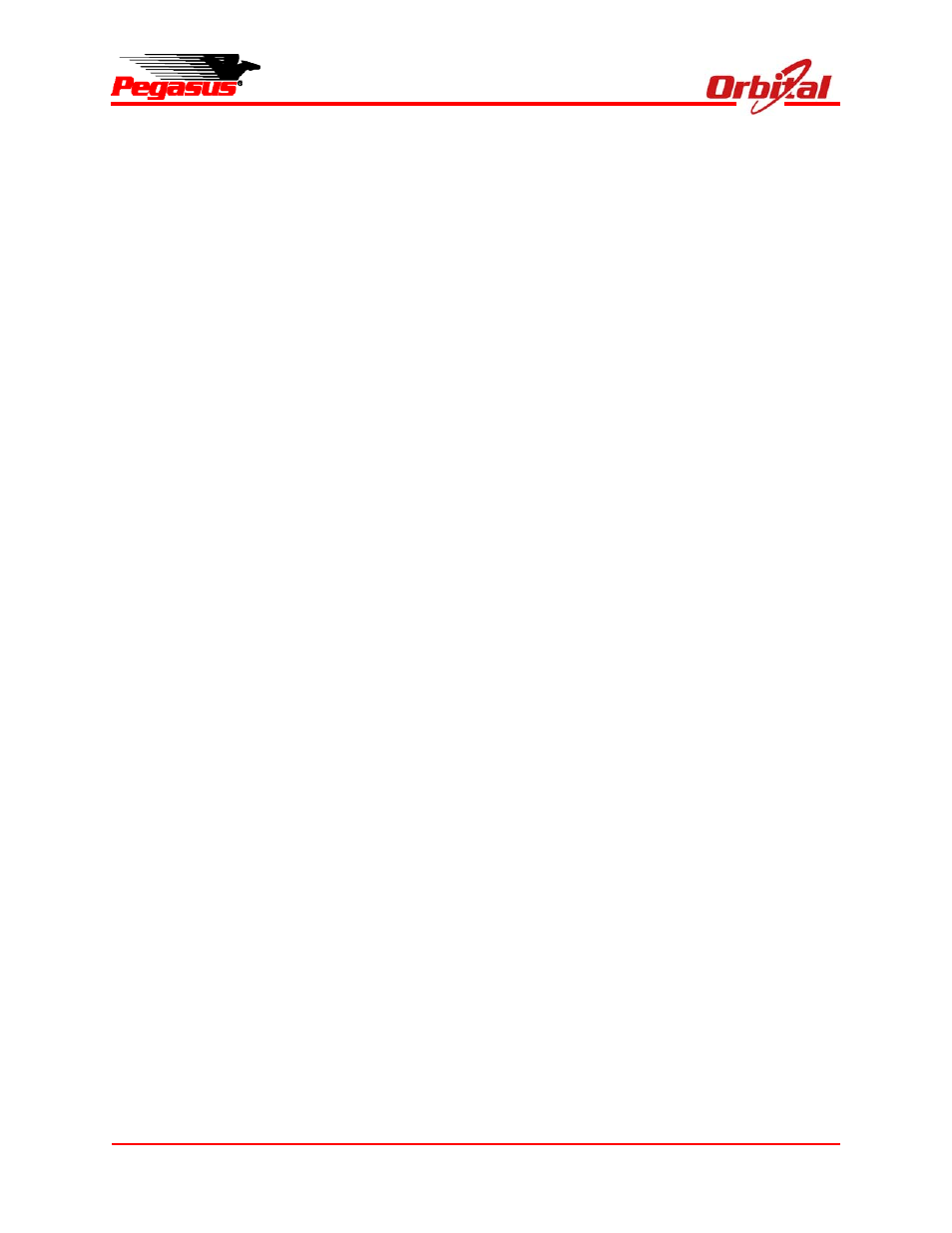
Release 7.0
Apr 2010
21
Pegasus User’s Guide
fairing is maintained to < 60%. The flowrate of air
through the fairing is maintained between 120 and
200 cfm.
4.9.3. Ground Operations at the Flightline and
Launch Operations
Following transportation of the Pegasus vehicle to
the Hot Pad, the fairing is continuously purged
with conditioned filtered air. During ground
operations, the temperature of the conditioned air,
as measured at the fairing inlet, is maintained
between 13 to 29 ºC (55.4 to 84.2 ºF). The
relative humidity of the conditioned air is
maintained to ≤55%. During ground operations,
the flowrate of air through the fairing is maintained
between 120 and 200 cfm. During launch
operations, which includes captive carry, the
flowrate of air through the fairing is maintained
between 120 and 240 cfm. During captive carry,
the air temperature within the fairing is significantly
colder than the measured inlet air temperature due
to the cold ambient conditions at altitude. The
bulk air temperature within the fairing during the
approximately 1-hour long captive carry will
typically be between 0 and 10 ºC.
4.9.4. Powered Flight
The inside fairing wall is the component with the
highest temperature that has a view factor to the
payload during powered flight. Flight data shows
that the fairing structure does not exceed 60 ºC
prior to jettison from the vehicle during Stage 2
burn. As a standard service, a low emissivity
aluminum liner is applied to the inside wall of the
fairing. The emissivity of the fairing liner is less
than 0.1.
The forward dome of the third stage motor does
not have a significant view factor to the payload
due to the RCS tank, bulkhead and avionics
components located within the avionics section.
4.9.5. Nitrogen Purge
There are two standard nitrogen systems that
provide nitrogen to the fairing during various
phases of a launch. All nitrogen meets MIL-PRF-
27401C, Grade B specifications.
Avionics Cooling purge use is used to maintain
launch vehicle avionics in their operational
temperature range. This system is controlled
solely at the discretion of the launch vehicle and
provides 725 slpm (26 scfm) directed to various
high dissipating launch vehicle avionics
components. Flow is ground adjustable in 33%
increments to maintain temperatures and post-
landing humidity within limits.
Fairing Purge is used to prevent condensation
within the payload fairing as the aircraft descends
in altitude following an abort and return to base.
This system is controlled solely at the discretion of
the launch vehicle and provides 535 slpm (19.2
scfm) to the forward part of the fairing through two
tubes and exit through nozzles that are nominally
mounted on the fairing forward bulkhead. Flow is
ground adjustable in 33% increments to maintain
temperatures and post-landing humidity within
limits. One nozzle can be relocated at payload
discretion, however, the purge system will be
turned on/off to meet launch vehicle needs. The
location of these nozzles is documented in the
payload mechanical ICD.
4.10. Payload Electromagnetic Environment
The electromagnetic environment to which the
payload will be exposed during ground processing,
launch operations and powered flight is due to a
combination of RF emitters. These emitters fall
into three categories: 1) RF systems onboard the
Pegasus launch vehicle and the L1011 carrier
aircraft; 2) Range emitters such as tracking radars
and the FTS command uplink; and 3) uncontrolled
emitters not associated with the Range such as
military, air traffic control and weather radars as
well as satellite control ground stations.
Figure 4-12 lists the frequencies and maximum
field strength associated with RF emitters on the
Pegasus launch vehicle. The worst-case field