Pegasus user’s guide – Orbital Pegasus User Manual
Page 56
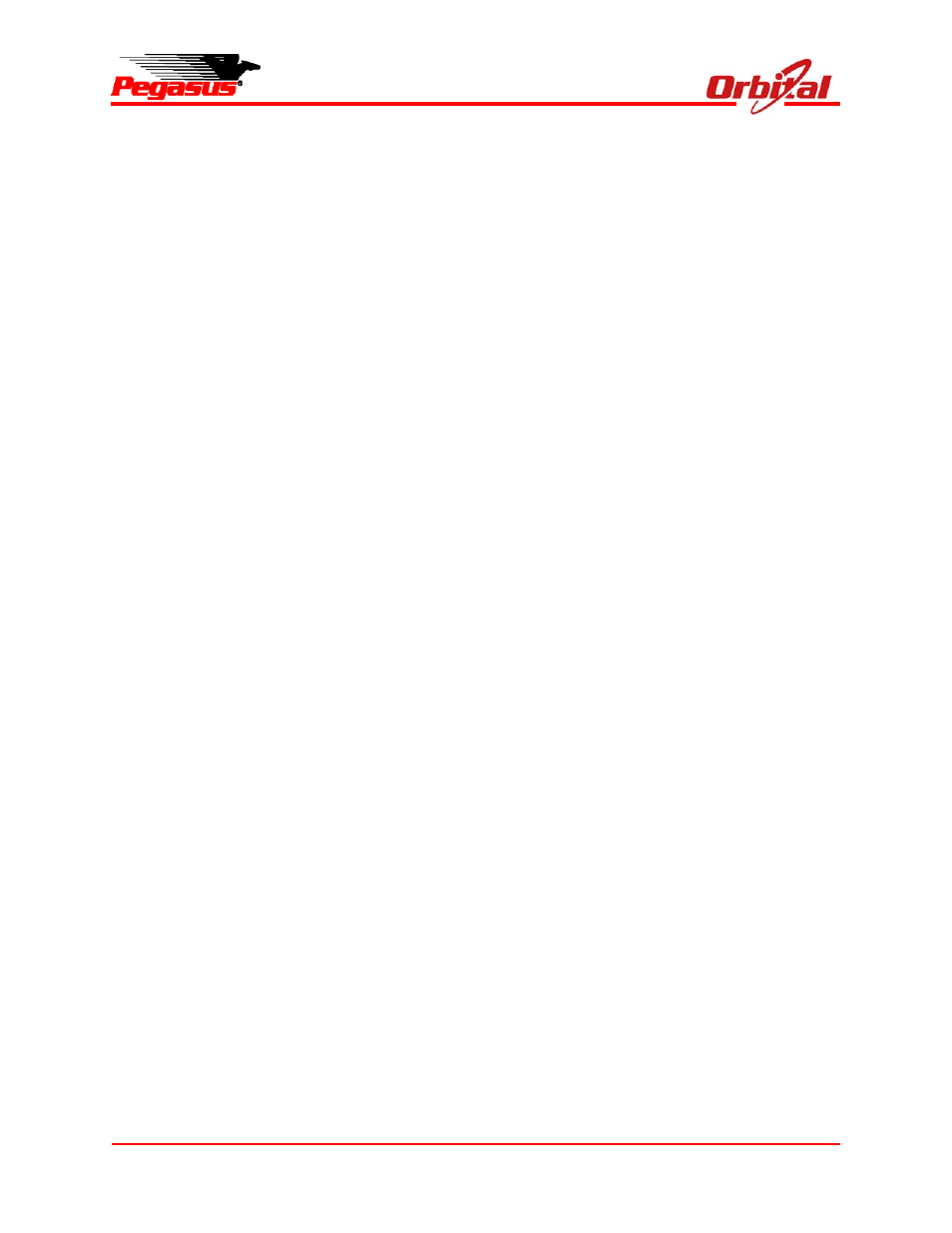
Release 7.0
Apr 2010
45
Pegasus User’s Guide
It cannot be overstressed that the applicable
safety requirements should be considered in the
earliest stages of spacecraft design. Processing
and launch site ranges discourage the use of
waivers and variances. Furthermore, approval of
such waivers cannot be guaranteed.
6.5.2. System Safety Documentation
A Payload System Safety Program Plan (SSPP)
shall be submitted to and approved by Orbital and
the applicable Range Safety Organization. The
SSPP shall include a description of the payloader
System Safety Program as required in
AFSPCMAN 91-710.
Range Safety requires certification that spacecraft
systems are designed, tested, inspected, and
operated in accordance with the applicable
regulations. This certification takes the form of the
Missile System Pre-Launch Safety Package
(MSPSP) (also referred to as the Accident Risk
Assessment Report (ARAR)), which describes all
hazardous systems on the spacecraft and
associated GSE. Hazardous systems include
ordnance systems, separation systems, solar
array deployment systems, power sources, RF
and ionizing radiation sources, high pressure
systems, and propulsion systems. The MSPSP
must describe all GSE used at the processing and
launch sites, with special attention given to lifting,
handling GSE, and pressurization, or propellant
loading equipment. AFSPCMAN 91-710 Volume 3
provides an outline of a typical MSPSP.
At certain sites, specific approval must be
obtained for all radiation sources (RF and
ionizing). Orbital will coordinate with the
spacecraft organization and the specific site safety
office to determine data requirements and work to
obtain approval. Data requirements for RF
systems normally include power output, center
frequency, scheduling times for radiating, and
minimum safe distances. Data requirements for
ionizing sources normally include identification of
the source, source strength, half-life, hazard
control measures, and minimum safe distances.
The MSPSP must also identify all hazardous
materials that are used on the spacecraft, GSE, or
during operations at the processing and launch
sites. Some examples of hazardous materials are
purge gases, propellant, battery electrolyte,
cleaning solvents, epoxy, and other adhesives. A
Material Safety Data Sheet must be provided in
the MSPSP for each hazardous material. Also, an
estimate of the amount of each material used on
the spacecraft or GSE, or consumed during
processing shall be provided.
A Ground Operations Plan (GOP) is required to be
submitted to Orbital and Range Safety. After
approval from Orbital and Range Safety, the GOP
may be incorporated into the MSPSP. If the GOP
is incorporated into the MSPSP, the MSPSP shall
specify the ground operations flow and identify
those operations that are considered hazardous.
Hazardous operations include lifting,
pressurization, battery activation, propellant
loading, and RF radiating operations.
All hazardous procedures that will be performed at
the processing or launch site must be submitted to
the specific site safety office for approval.
Additionally, Orbital shall review and approve
hazardous spacecraft procedures to ensure
personnel at Orbital facilities will be adequately
protected from harm. Orbital shall provide the
coordination necessary for timely submission,
review, and approval of these procedures.
6.5.3. Safety Approval Process
Figure 6-5 depicts the typical safety approval
process for a commercial Pegasus mission. If
permitted by the processing and launch site safety
organizations, it is recommended that tailoring of
the applicable safety requirements be conducted
early in the spacecraft design effort. This will
result in greater understanding of the site-specific
regulations, and may provide more flexibility in