Pegasus user’s guide – Orbital Pegasus User Manual
Page 34
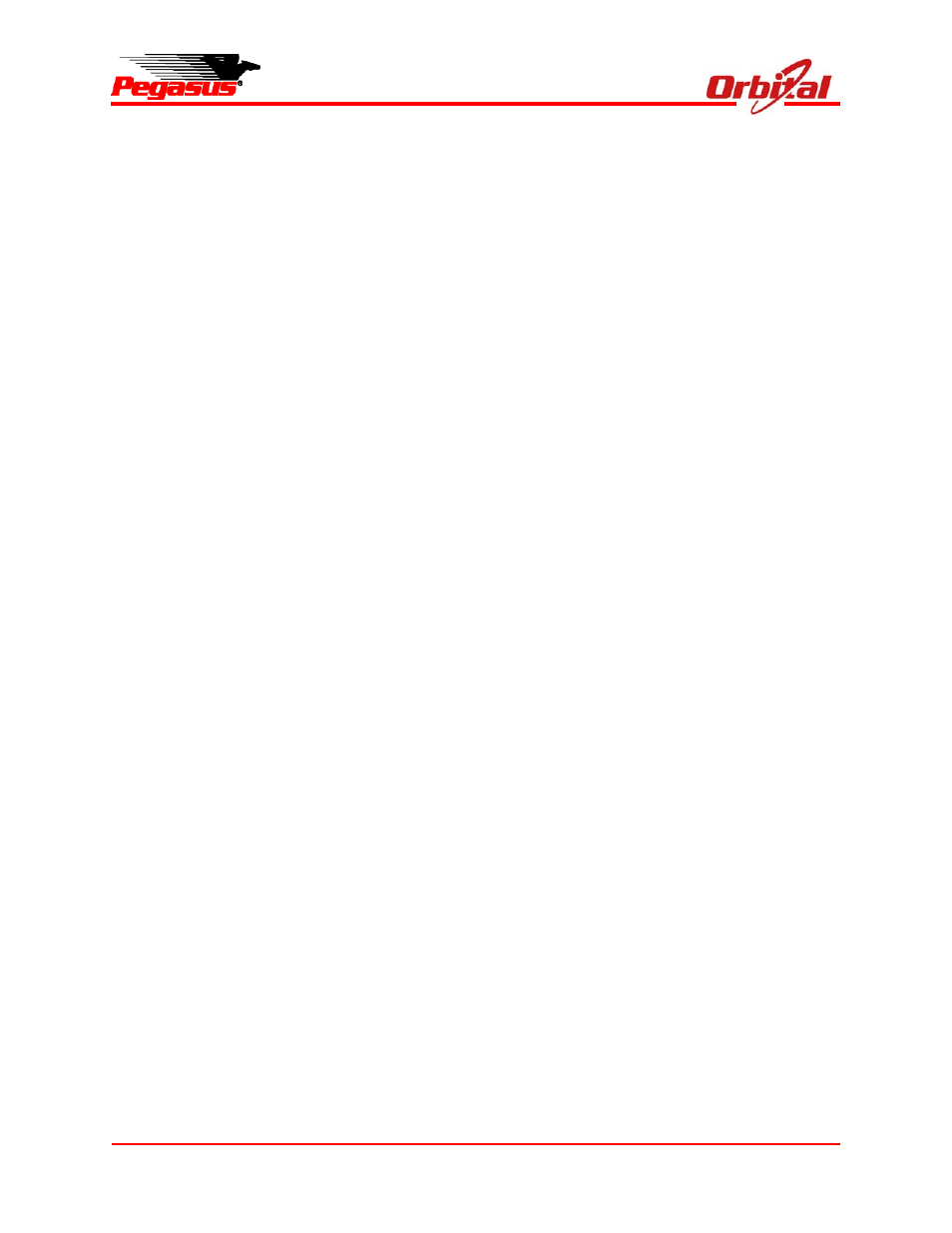
Release 7.0
Apr 2010
23
Pegasus User’s Guide
practices that are followed to ensure payload
contamination requirements are met.
The VAB is maintained at all times as a visibly
clean, air-conditioned, humidity-controlled work
area. As a standard service, the payload can be
provided with a soft-walled cleanroom that is
certified and operated at Class 8 (Class 100,000)
level per ISO 14644-1. This vertical down flow
cleanroom is 12’(W) x 24’(L) x 14’(H). As an
optional nonstandard service, the cleanroom can
be certified and operated at ISO 14644-1 Class 7
(Class 10,000). Overhead crane lifts must occur
outside of the cleanroom. If crane lifts are
required for payload handling, it may be necessary
to bag or otherwise protect the payload while it is
outside of the cleanroom.
After encapsulation of the payload, the fairing is
purged with conditioned air that is certified to ISO
14644-1 Class 8. Within the VAB, this air flow is
provided by an air conditioning system. The
output of the facility air conditioner is routed
through an activated charcoal and high-efficiency
particulate air (HEPA) filters prior to being directed
into the nose of the fairing. Particulate levels
within the airflow are measured prior to and
continuously after the system is connected to the
fairing. The activated charcoal filter removes
better than 95% of volatile hydrocarbons with a
molecular weight of 70 or higher. During
transportation of the Pegasus launch vehicle to the
Hot Pad, the fairing purge air is provided using a
mobile blower. The output from the blower is
routed through a desiccant bank to control
humidity and a similar activated charcoal and
HEPA filter system. While at the Hot Pad, the
fairing purge air is supplied using a specially
designed ground air conditioning system (GACS)
that includes a desiccant dryer wheel and heater
to allow control of humidity and temperature.
During launch operations and captive carry, the
fairing air flow is provided using the airborne air
conditioning system (AACS) on the L1011 carrier
aircraft. For both air conditioning systems, the
output air flow is routed through an activated
charcoal and HEPA filter system prior to entering
the fairing. The air flow to the fairing is constantly
monitored for temperature, humidity, flow rate, and
particulate levels.
The inner surface of the Pegasus payload fairing
is a low emissivity aluminum liner. As a standard
service, this liner is cleaned and maintained to
Level 750A cleanliness requirements of IEST-
STD-CC1246D. As an optional nonstandard
service, the fairing liner can be cleaned and
maintained to Level 600A or 500A.
All materials within the fairing that are in close
proximity to the payload are selected based on
NASA RP-1124. To the extent possible, all
materials meet NASA outgassing standards of
total mass loss (TML) <1.0% and collected volatile
condensable material (CVCM) <0.1%. For those
materials that do not meet these requirements, an
accounting of material quantity, location and
contamination mitigation measures is provided to
the customer.
5. SPACECRAFT INTERFACES
5.1. Payload Fairing
This section describes the fairing, fairing
separation sequence, payload static and dynamic
envelopes, and payload access panel. The
standard payload fairing consists of two graphite
composite halves, with a nosecap bonded to one
of the halves, and a separation system. Each
composite half is composed of a cylinder and an
ogive section. The two halves are held together
by two titanium straps, both of which wrap around
the cylinder section, one near its midpoint and one
just aft of the ogive section. Additionally, an
internal retention bolt secures the two fairing
halves together at the surface where the nosecap
overlaps the top surface of the other fairing half.
The base of the fairing is separated using a
noncontaminating frangible joint. Severing the