Pegasus user’s guide – Orbital Pegasus User Manual
Page 35
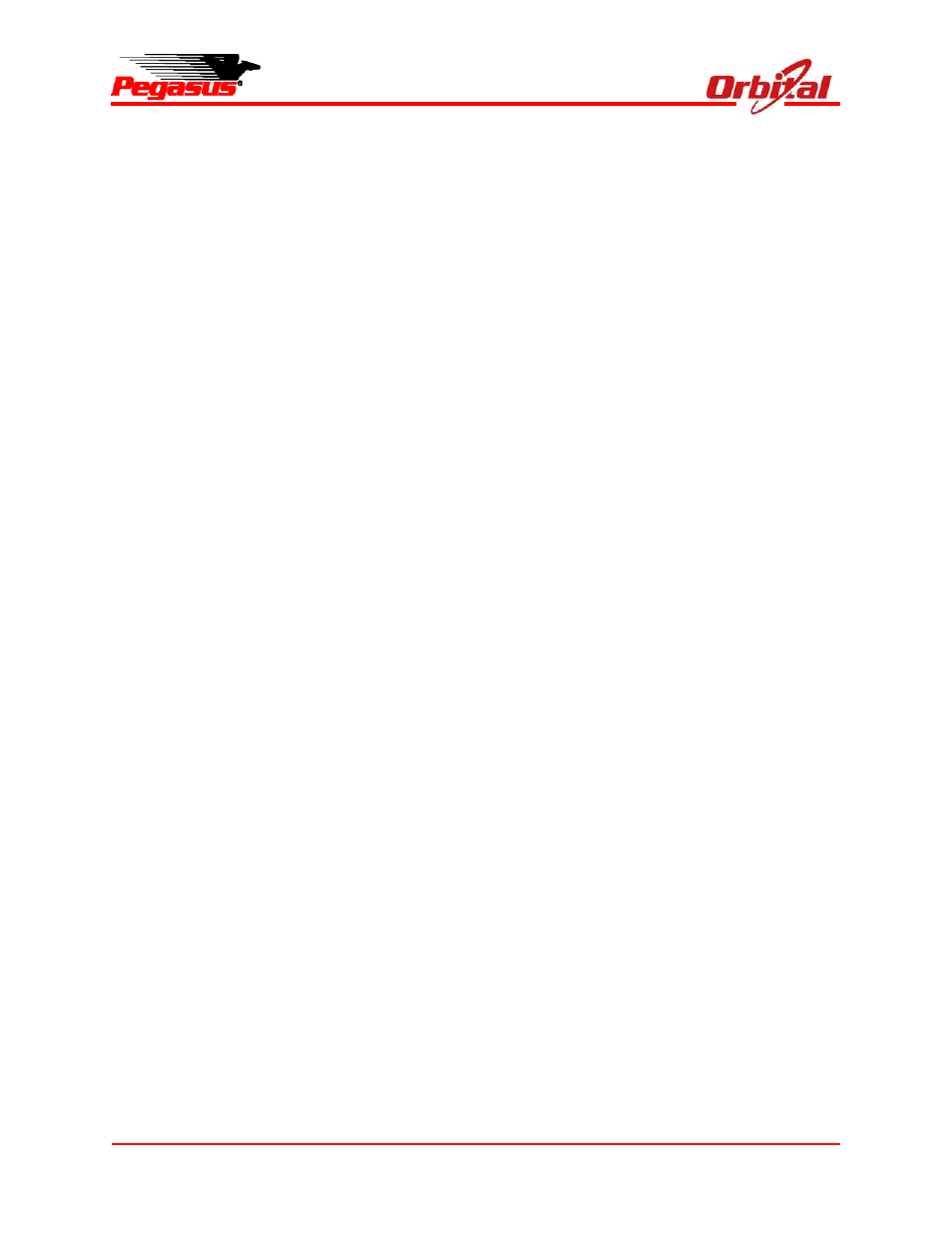
Release 7.0
Apr 2010
24
Pegasus User’s Guide
aluminum attach joint allows each half of the
fairing to then rotate on hinges mounted on the
Stage 2 side of the interface.
5.1.1. Fairing Separation Sequence
The fairing separation sequence consists of
sequentially actuating pyrotechnic devices that
release the right and left halves of the fairing from
a closed position, and deploy the halves away
from either side of the core vehicle. The nose bolt
is a noncontaminating device. The pyrotechnic
devices include a separation nut at the nose,
forward and aft bolt cutter pairs for the external
separation straps at the cylindrical portion of the
fairing, a frangible joint separation system at the
base, and a pyrogen gas thruster system for
deployment.
5.1.2. Payload Design Envelopes
The payload static envelope for a rigid payload
hard mounted to the 97 cm (38 in.) PA is shown in
Figure 5-1. The payload static envelope for the 59
cm (23 in.) PA is shown in Figure 5-3. No portion
of the payload shall extend aft of the
payload/launch vehicle interface plane, unless
otherwise approved in the ICD. The static
envelopes account for fairing and payload
structural deflections assuming a minimum lateral
bending frequency of 20 Hz for the payload. The
static envelope accounts for PAF interface plane
deflection and rotation. The static envelope does
not account for payload non-rigid body deflections,
payload dimensional errors due to
manufacturing/design and tolerance stack-up shall
be accounted for within the static envelope.
Extensions of the static envelope are common but
must be assessed on a mission-specific basis.
Pegasus payload dynamic envelopes are provided
in Figure 5-2 and Figure 5-4.
5.1.3. Payload Access Door
Unless otherwise specified in the contract, Orbital
provides one 21.6 cm x 33.0 cm (8.5 in. x 13.0 in.)
graphite payload fairing access door. The long
dimension of the load-bearing rectangular door
shall be oriented along the vehicle x-axis, and can
be positioned according to user requirements
within the zones defined in Figure 5-5. The
position of the payload fairing access door must
be defined no later than L-18 months.
5.2. Payload Mechanical Interface and
Separation System
Orbital will provide all hardware and integration
services necessary to attach nonseparating and
separating payloads to Pegasus. All attachment
hardware, whether Orbital or customer provided,
must contain locking features consisting of locking
nuts, inserts, or fasteners. Orbital provides
identical bolt patterns for both separating and
nonseparating mechanical interfaces.
5.2.1. Standard Nonseparating Mechanical
Interface
Figure 5-6 illustrates the standard, nonseparating
payload mechanical interface. This is for payloads
that provide their own separation system and
payloads that will not separate. Direct attachment
of the payload is made on the Avionics Structure
with sixty #10 fasteners as shown in Figure 5-6.
Orbital will supply a detailed drawing of the bolt
circle to allow accurate machining of the fastener
holes and will supply all necessary attachment
hardware per the payload specifications.
5.2.2. Standard Separating Mechanical
Interface
If the standard Pegasus payload separation
system is used, Orbital controls the entire
spacecraft separation process. The standard
separation system uses a Marmon clamp design.
Two different separation systems are available,
depending on payload interface and size. They
are the 97 cm (38 in.) and 59 cm (23 in.)
separation systems. The 97 cm (38 in.) separable
payload interface is shown in Figure 5-7 and the
59 cm (23 in.) separable payload interface is
shown in Figure 5-8.