Faults group, Tools group, Run panel – Lenze IMSS500+ Simple Servo 500 600 i1000 User Manual
Page 52: Drive monitor, Oscilloscope tool, 7 faults group, 8 tools group
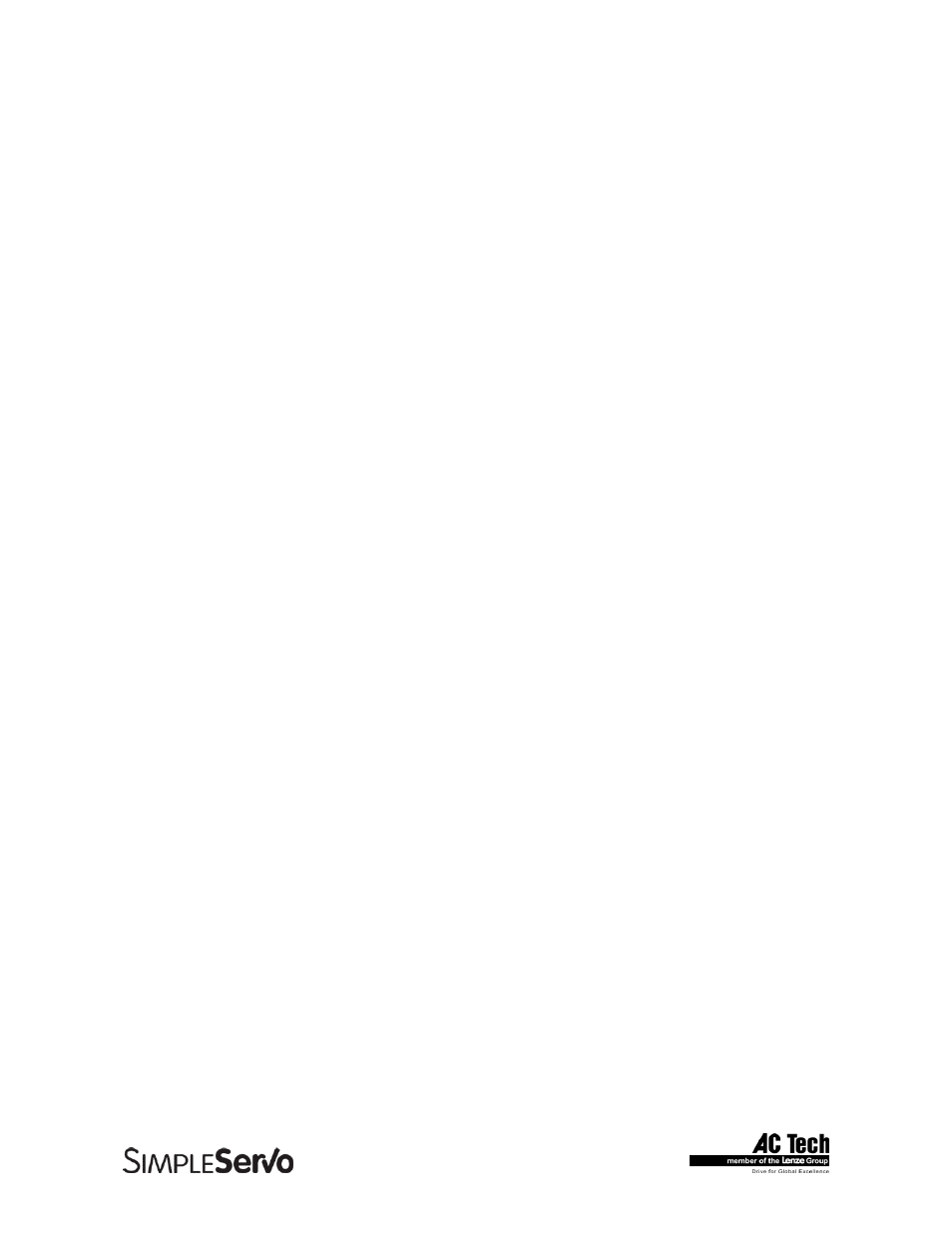
SimpleServo 500/600/i1000 User Manual Rev 3.4
• Vff (Velocity feed forward)
The output of the Vff-term portion of the filter proportional to demanded motor speed when drive shaft
travels from position to position. Vff-term is an open loop term. It is responsible for removing velocity
error while positioning thus increasing system response and precision.
• IL – integral gain limit in % of torque
The output of the I-term portion of the integral gain compensator could be limited to some level set by
IL limiter. In other words, the influence of I-term on motor shaft torque could be controlled by IL limiter.
This helps to decrease overshoot caused by I –gain especially when position error is integrated over a
long time period.
6.7 Faults Group
Faults Group loads fault history from the drive. New faults replace oldest faults in a circular manner. In
any case fault # 0 is the most recent fault. To clear faults history from the drive’s memory click on
“Reset Fault history” button. Each fault has its code and explanation of the fault.
6.8 Tools Group
6.8.1 Run
Panel
Run Panel is active in velocity mode only. It replicates an analog potentiometer as if it would be
connected to analog reference input. Velocity Scale parameter in Parameter Group set the scale of
this “potentiometer” just the same way it sets it for analog input. There is a check box “Enable
Reference sweep” which makes reference invert with period set by parameter (on run panel) “Sweep
Time”. This feature of the run panel allows you to create “Square wave” reference with adjustable
period (“Sweep Time”) and magnitude (Reference Slider) for easy tuning.
6.8.2 Drive
monitor
Drive monitor shows you motor hall sensors’ states and actual motor encoder counts. This tool is
useful when troubleshooting motor encoder’s connections.
6.8.3 Oscilloscope
tool
Oscilloscope tool gives real time representation of different signals inside the SimpleServo drive and is
helpful when debugging and tuning drives. Operation of oscilloscope tool described in MotionView
software’s User’s Manual. Below given the list of the signals you can observe with oscilloscope tool:
Phase Current (RMS):
Motor phase current
Phase Current (Peak):
Motor peak current
Iq Current:
Measures the motor Iq (torque producing) current
Motor Velocity:
Actual motor speed in RPM
Commanded Velocity:
Desired motor speed in RPM (velocity mode only)
Velocity Error:
Difference in RPM between actual and commanded motor
speed
Position Error:
Difference between actual and commanded position (Step &
Direction mode only)
52