Lenze IMSS500+ Simple Servo 500 600 i1000 User Manual
Page 46
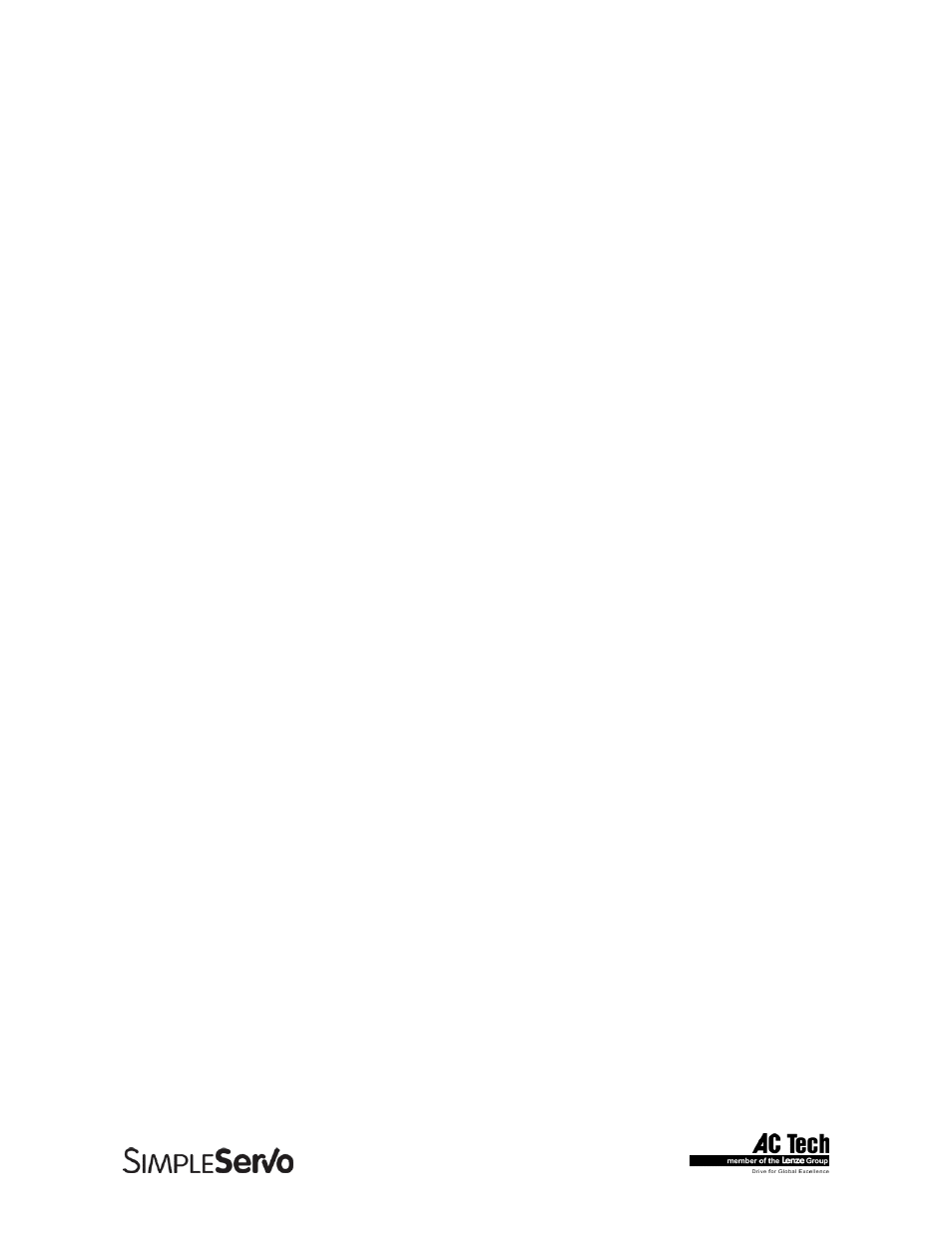
SimpleServo 500/600/i1000 User Manual Rev 3.4
• Step and Direction mode
In this mode drive reference is step and direction digital inputs. Drive position and distance
moved can be calculated using formula:
DISTANCE MOVED (Revolutions) = NUMBER OF PULSES SUPPLIED TO INPUT / Steps
per revolution. Scaling is set in Steps per revolution parameter and input type is set by Step
input type parameter. (See below in this topic) .
• Gearing
Gearing is accomplished by connecting Master encoder to Step and Direction Inputs. If master
encoder has outputs in quadrature parameter “Step input Type” should be set to “Master
Encoder”. If Master encoder has single output (unidirectional encoder) then “Step input Type”
should be set to “Step and Direction” type. Direction inputs should be shorted together to
avoid noise penetration.
To obtain necessary gearing ratio you should set “Step Per Revolution” parameter. Here is
how to calculate:
SpR = MEppr *4 / G
, where
SpR
-
step per revolutions parameter
Meppr -
Master Encoder resolution (pre-quad)
G
-
desired gear ratio
Example 1:
500 ppr (pre-quad) master encoder.
Desired ratio G = ¼, i.e on every master encoder revolution slave motor will rotate ¼
of the revolution.
SpR = 500 *4 / ¼ = 500 *4 / 0.25 = 8000
Example 2:
1000 ppr (pre-quad) master encoder
Desired G = 1.24
SpR = 1000 *4 / 1.24 = 3225.8 , round up to nearest integer number 3226.
Calculated gear error: 3225.8 / 3226 = 0.99993 (or 99.993 %)
100%-99.993 = 0.007% - gearing error
1.24 * 0.99993 = 1.239923 – real gear ratio.
• Step & Direction P+V mode using inner velocity compensator and outer position loop
compensator. Both Velocity and Position loop filters are active. This mode is recommended for
general purpose mechanisms. Especially helpful when instantaneous velocity precision is
required.
• Step & Direction PIVFF mode using integral position regulator which embeds velocity loop. This
mode recommended for rigid servo mechanisms while trying to accomplish maximum
performance. Mode is recommended for mechanisms with low inertial ratio match 1:4 or less.
46