ERICO LENTON INTERLOK Rebar Splicing System User Manual
Page 23
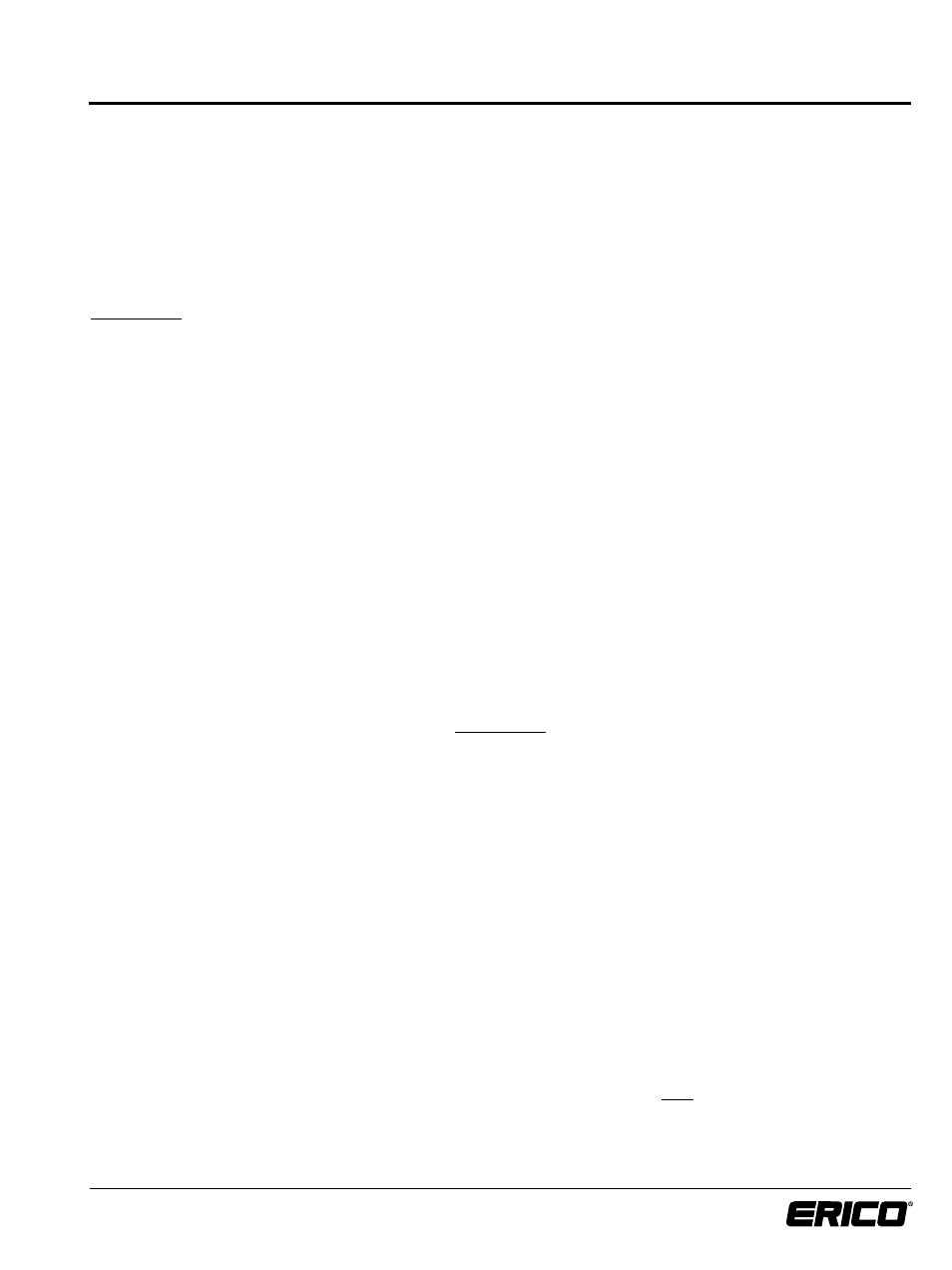
17
www.erico.com
2.4 Gravity Fill Installation Instructions
For HY10L Filler Material
6) Mix the HY10L according to the mixing directions on the bag. Use only full bags of HY10L for each batch made.
7) Grout may be placed by hand or a grout pump may be used to place the HY10L. Contact ERICO for recommended grout
pumps. NOTE: Before using the grout pump, carefully read and understand the Pump Users Manual. It is important to follow
all the manufacturer’s recommended guidelines regarding safety, operations, service, and maintenance.
8) For gravity fill application, pump or pour the HY10L evenly and continuously into the open end of the coupler. Referring
to the table on the following page, fill the coupler to the level “A” shown for the bar size of interest measuring down
from the top with a ruler and filling the grout to that level. It is acceptable to slightly overfill the coupler, as any excess
grout will be removed when the bars are placed inside the coupler. However, for maximum grout economy it is advised
that the couplers be filled with the proper amounts to avoid waste.
!!CAUTION!! DO NOT UNDERFILL the coupler as this will result in reduced connection and performance. Coupler should be
filled completely and fully. Grout should be placed into the coupler in one step and no cold joints should be present.
9) Once the couplers have been filled to the proper level, remove any air that may be trapped in the HY10L by tamping it
with a small diameter rod.
10) Once the HY10L has been tamped, immediately lower the precast member until it is properly seated and aligned. It is
advised that the precast member be lowered slowly into the coupler to avoid air bubbles. Check to make sure the panels
are level and that grout completely surrounds the rebar to the top.
NOTE:
It is recommended that all grouting operations are inspected by the engineer to make sure that all the manufacturer’s
recommended procedures and all applicable building codes have been observed. If any HY10L leaks out onto the
surface of the precast panel remove it immediately with flushing water to avoid unsightly rust stains.
11) The decision to remove bracing following grouting must be determined solely by the Structural Engineer. In order to
ensure a quality structural connection, it is important that the grouted couplers in a precast panel or member be secured
and undisturbed by movement, shock, or vibration until the HY10L has reached a compressive strength of at least 3000
psi (21 MPa). Typically this will occur after 1 day at 68°F (20°C), however, this time will vary depending on the temperature
and job site conditions. In cold weather, the curing time will be significantly lengthened (2 or more days at 40°F; 4°C),
therefore, the bracing time may need to be increased. It is strongly recommended that the compressive strength of the
HY10L be checked under job site curing conditions according to the procedures outlined in ASTM C-109 before proceeding
with upper story erection.
12) Once the installation of the grout is complete and the panels are braced and secured, fill the seam between the two panels
with a dry pack sealing mortar.
!!CAUTION!!
ANY OF THE FOLLOWING ITEMS IF NOT OBSERVED MAY RESULT IN REDUCED CONNECTION PERFORMANCE.
1) Refer to Mixing Directions and Cautions on the LENTON
®
INTERLOK bag before mixing or doing any work with the
HY10L. Do not use any damaged, wet, or open bags. Do not use grout which is more than 1 year old. These bags
should be discarded in accordance with Federal, State, and Local Regulations.
2)
When pumping, never let the hopper become empty as this will result in air getting into the couplers.
Prepare additional HY10L to keep on hand to avoid this situation.
3) If grouting is interrupted, keep recirculating the HY10L by operating the pump with the nozzle in the hopper. This
movement of the HY10L will aid in keeping it fluid. If the shut down exceeds the limits of time specified in this manual
noted in Figure 1 of Hot & Cold Weather Grouting Instructions, (for example 60 minutes at 70°F (21°C), THE GROUT
MUST BE DISCARDED.
4) Never leave a coupler partially filled for an extended period of time. Make sure all couplers are filled completely and no
couplers are left ungrouted. Do not underfill the coupler. Place the grout into the coupler in one step – do not create a
cold joint in the coupler.
5) After grouting, keep the walls and panels undisturbed for at least 24 hours at 68°F (20°C). The final decision to
remove bracing is an engineering decision which must be determined solely by the structural engineer based on job
site conditions.
During cold weather grouting (temperature below 50°F; (10°C) the bracing time must be extended to at least 48
hours to allow the HY10L to gain the required strength.
6) Immediately following check grouting to make sure that no grout has leaked from the coupler.
Refer to the Trouble Shooting Guide located in this manual for additional guidelines.