Recommended grade and cutting data, Case story, Practical hints – Sandvik Coromant Parting and grooving - users guide User Manual
Page 45
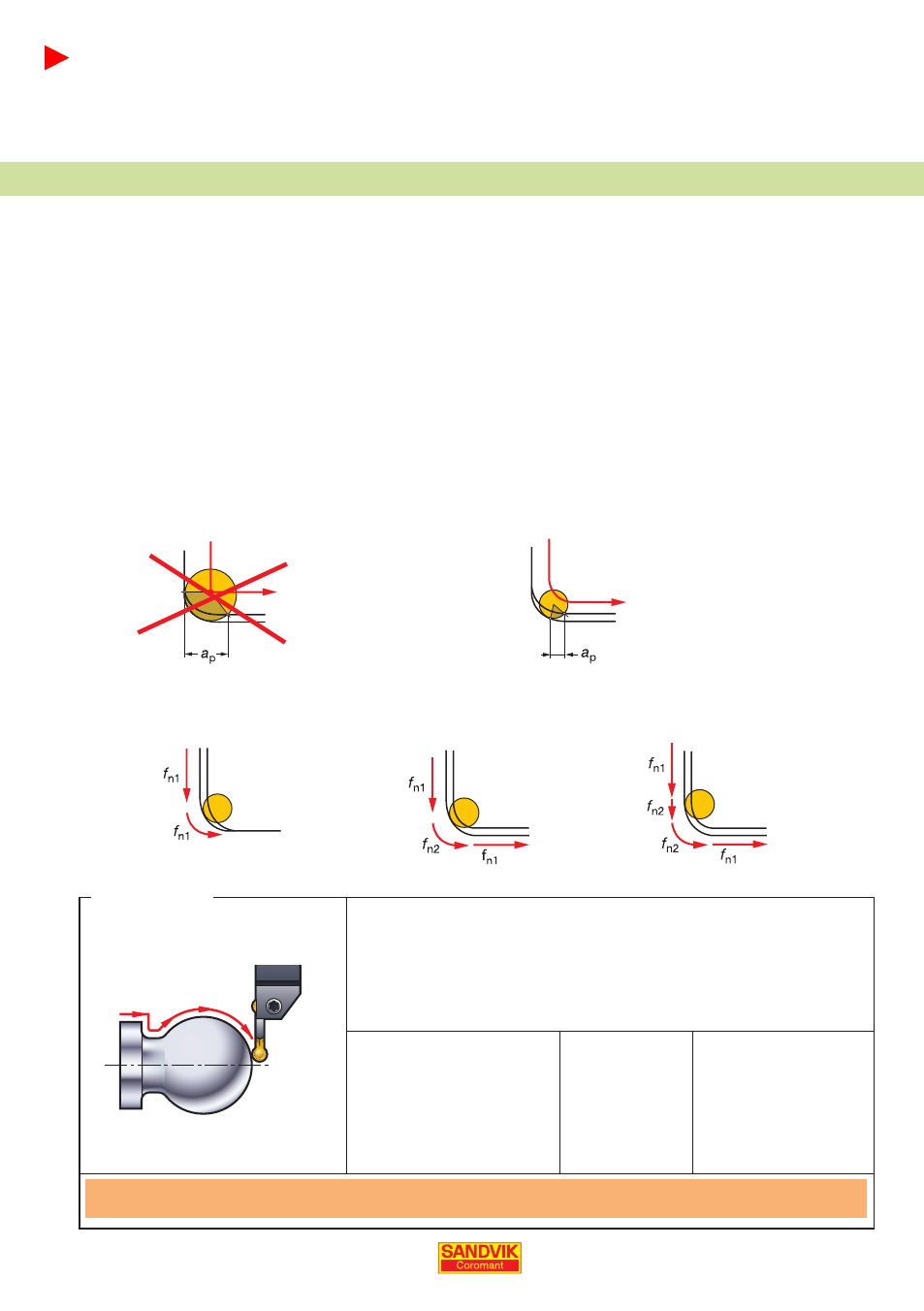
43
Wrap around is a problem that occurs with round inserts when plunging or profiling into
corners. A large area of the insert is in contact all the time, creating high cutting pressure,
so the feed needs to be reduced. HHowever, if reduced too much, vibration may occur. To
reduce this problem the insert diameter should be as small as possible compared to the radius
being generated.
A good starting point is to use 50% feed into radius plunging compared to parallel cuts, see
example.
If you must use the same insert radius, microstops (dwelling, etc) should be used to make the
chip short and to avoid vibration.
Recommended grade and cutting data
Starting grade GC1125.
Cutting speed start value 150 m/min and feed start value 0.20 mm/r.
f
n1
= parallel cuts – max. chip thickness 0.15–0.40 mm
f
n2
= radius plunging – 50% max. chip thickness
Insert radius ≥ component radius
Not recommended
Insert radius < component radius
Recommended
Machining specification
Operation: Profiling ball
Material: BS080M46, CMC 01.2, HB 180
Machine: CNC turning lathe
Toolholder: LF123J13-2525BM
Insert: N123J2-0600-RM
Grade: GC1125
Cutting data
Cutting speed:
Feed:
Cutting dept:
Time in cut:
Components:
Competitor
200 m/min
0.3 mm/r
0.5–2.0 mm
1.07 min
175 pcs/edge
Sandvik Coromant
200 m/min
0.4 mm/r
0.5–2.0 mm
0.8 min
248 pcs/edge
Case story
Tool life +42%
Productivity +25%
Annual time saving 82 hours
Practical hints