System components, Specifications – Warner Electric MCS-208 User Manual
Page 3
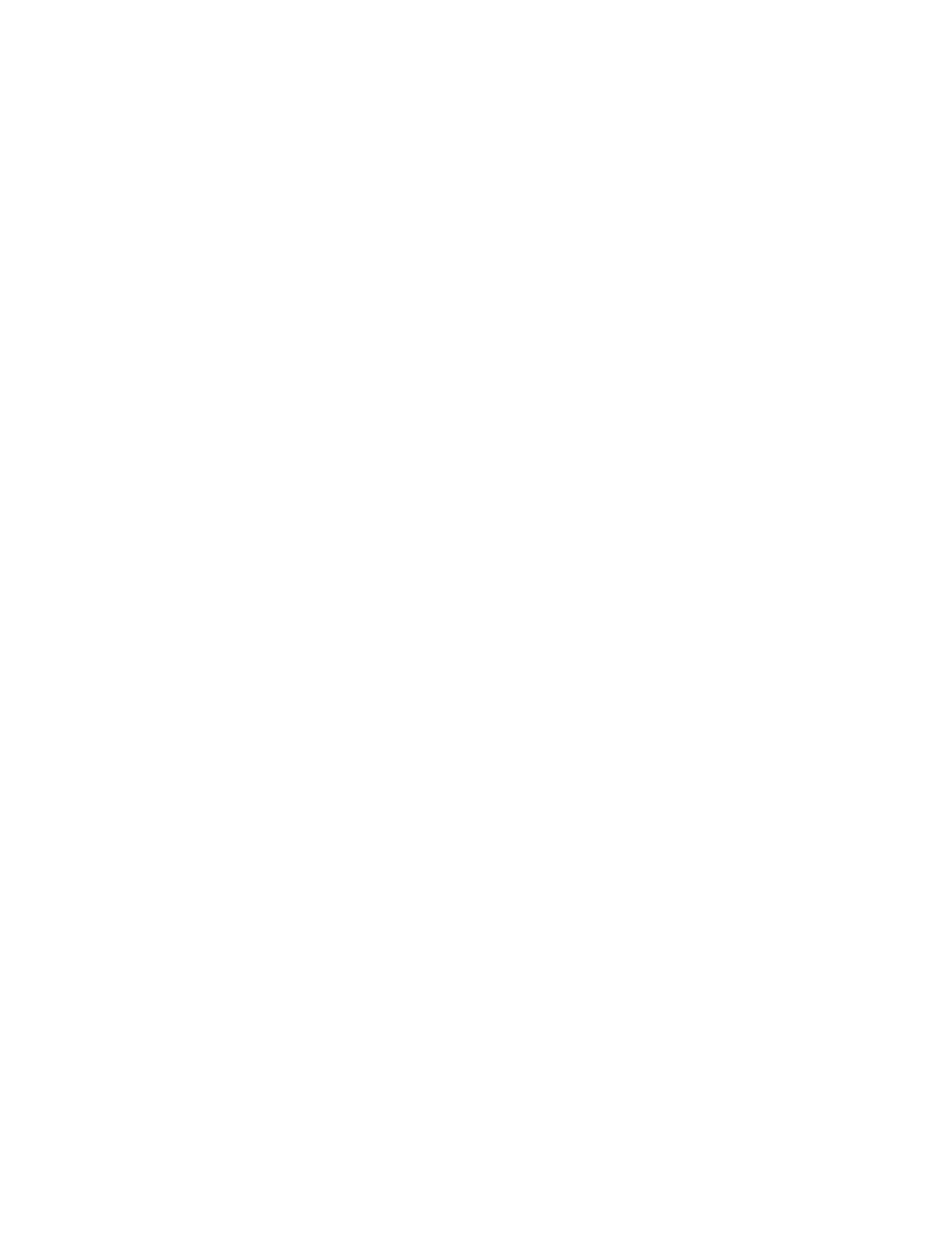
Warner Electric • 800-825-9050
P-276 • 819-9045
3
System Components
Brake
The Air Disc brake develops braking torque that is
proportional to the air pressure applied to the brake's
air chambers. The pressure required to control tension
is supplied by the electro-pneumatic transducer.
The Pneumatic Tension Control System can be used to
drive two Air Disc brakes in a dual brake application.
However, it may be necessary to add a volume booster.
Consult Warner Electric if other assistance is required.
electro-Pneumatic Transducer Kit
The transducer receives a signal from the control
module and outputs the correct air pressure to the
brake. Filtered air must be supplied to the transducer.
This kit contains the recommended filter and
transducer. Consult Warner Electric if other transducers
or filters are selected.
Power Supply
The MCS-166 Power Supply Module is designed to
operate either the MCS-207 Dancer Control or the
MCS-208 Remote/Analog Control. The MCS-166
accepts either 120 VAC or 220/240 VAC input power
and provides 26-28 VDC output power for operation of
the control modules.
Controls
The MCS-207 Dancer Control Module is a solid state
electronic control that receives a signal from a dancer
pivot-point sensor and outputs the appropriate
electrical signal to the electro-pneumatic transducer.
The transducer produces the correct air pressure at
the brake to maintain a stable dancer position. The
MCS-207 is a closed loop control.
The MCS-208 Remote/Analog Module is a solid state
electronic control that will accept a variety of input
signals and provide an output signal that is proportion
to the input signal. This output signal is converted to
brake air pressure through the electro-pneumatic
transducer. This system is open loop and any change in
air pressure to the brake must come from input to the
control from the signal source.
The MCS-208 can be
operated by the local torque knob on its face or
remotely by an external potentiometer, voltage input, or
current loop input.
Pivot Point Sensor
The MCS-605-1 or TCS-605-5 Pivot Point Sensors
provide the dancer position signal to the MCS-207
Dancer Control. The MCS-605-1 is coupled to the
dancer pivot when rotation is no more than 60 degrees,
while the TCS-605-5 covers rotation up to 300 degrees.
Specifications
MCS-166 Power Supply Module
Part Number: 6910-448-013
Input Power: 120 VAC or 220/240 VAC ±10%,
switch selectable
Ambient
Temperature: +32ºF to +120°F(0ºC to +49°C)
Output:
26± 4 VDC, unregulated, 1.5amps
maximum. over voltage protected
Fusing:
1/2 amp, 250V fast acting, type
3AG, AC input
MCS-207 Dancer Control Module
Part Number: 6910-448-066
Input Powers: 26 ± 4 VDC, 0.5 amps maximum
MCS-166 power supply recommended
Ambient
Temperature: +32°F to +120°F (0ºC to +49°C)
Outputs:
1-5 ma
4-20 ma*
10-50 ma
1-9 VDC
*NoTe: The standard transducer accepts a 4-20 ma
output.
Fuses:
1/2 amp, fast acting, 250 V
Protection:
Reverse voltage protection on the
DC power connections
Control Input: From MCS-605-1 or TCS-605-5
pivot point sensor
Auxiliary
Inputs:
Brake-On –– Applies full output
(current or voltage). Active low.
Brake-Off –– Applies minimum
output (current or voltage). Active low.
Anti-Drift –– Provides integrator
reset function. Active low.
Switch Inputs can be controlled by
switch closure between input and