Fulton FB-S Horizontal Firetube Boiler User Manual
Page 47
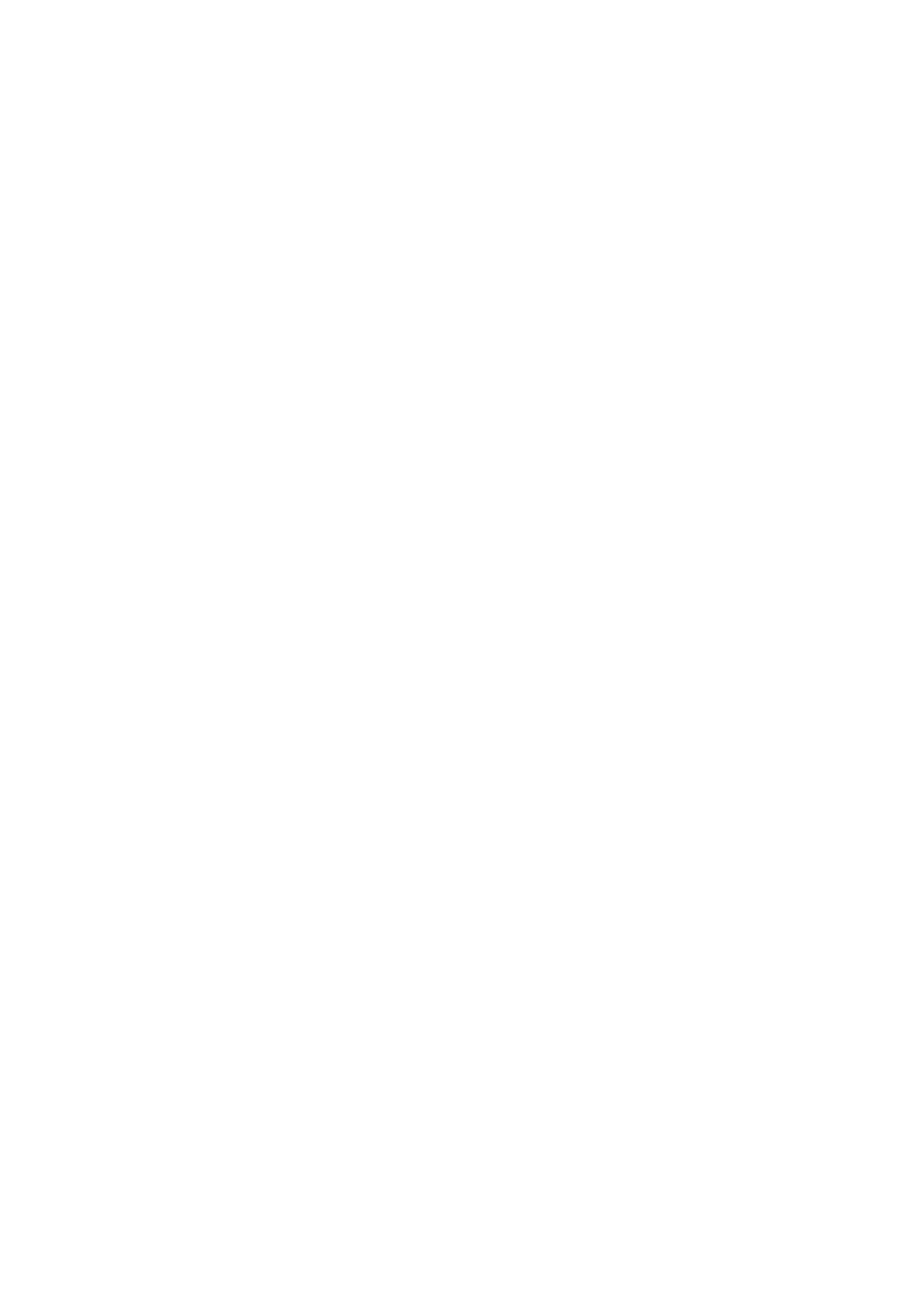
The Fulton Companies*FB-S Series Manual*Version 2010-0820 rev. 3/5/13
Page 47
temperature and by the heat transfer rate and gas temperature. The tube temperature lies
between the shell and furnace temperature, but is nearer the shell temperature. Since all
these components are virtually the same length, they expend longitudinally by different
amounts causing mechanical and thermal stress. Whilst this is catered for in mechanical
design of the pressure vessel, the life expectancy of the boiler can be affected if the boiler
is frequently heated to quickly from cold. When starting from cold the furnace approaches
its design temperature shortly after start-up, whereas the tube and shell temperatures are
delayed by the time taken to bring the contained water up to temperature. As a result, the
thermal expansion is at its greatest. Additionally, the temperature gradient which exists
between the bottom and the top of the boiler is exaggerated. This can be
reduced by blowing the boiler down during the heat-up period. In practical terms, the ideal
solution would be to gradually raise the temperature and pressure in the boiler
progressively by firing the boiler on low fire for a few minutes and leaving it to ‘soak’ (e.g.
allowing the temperatures in the boiler and water to even out by diffusion) for 20 to 30
minutes, blowing down the boiler, firing the boiler again for a little longer and soaking for
less, and so on. If the boiler has been fired the day before, the large thermal mass in the
boiler will maintain the internal temperature to a point that the boiler can be simple switched
on (preferably on low fire) and then left to reach working temperature/pressure. The life
expectancy of the boiler and door insulation, ignoring other factors, is proportional to the
number of the thermal/mechanical cycles that the boiler undergoes from cold/zero pressure
to working temperature and pressure. A boiler that is continually maintained at working
pressure will last longer than one that is constantly heated and cooled.
Service Inspection of Weld Joints
The frequency of the safety requirement for in service inspection of the main welded joints
of the boiler is calculated by the number of cycles since the last inspection. Boilers running
twenty four hours a day require the shell and furnace end plate welds to be inspected at
intervals specified by local boiler codes. Boilers that are continually heated and cooled
require more frequent inspection. The purpose of the in-service weld inspections is to check
for:
i.
Buried defects during manufacture that are outside acceptable limits.
Because the boiler was 100% tested during manufacture none should be
found, and upon proof of 100% manufacturer testing these tests may be
waived at the discretion of the ‘competent person’.
ii.
Cracks propagating from region of the toe of the fillet weld on the shell to
the tube plate weld, resulting from fatigue or corrosion fatigue cracking.