Fulton FB-S Horizontal Firetube Boiler User Manual
Page 23
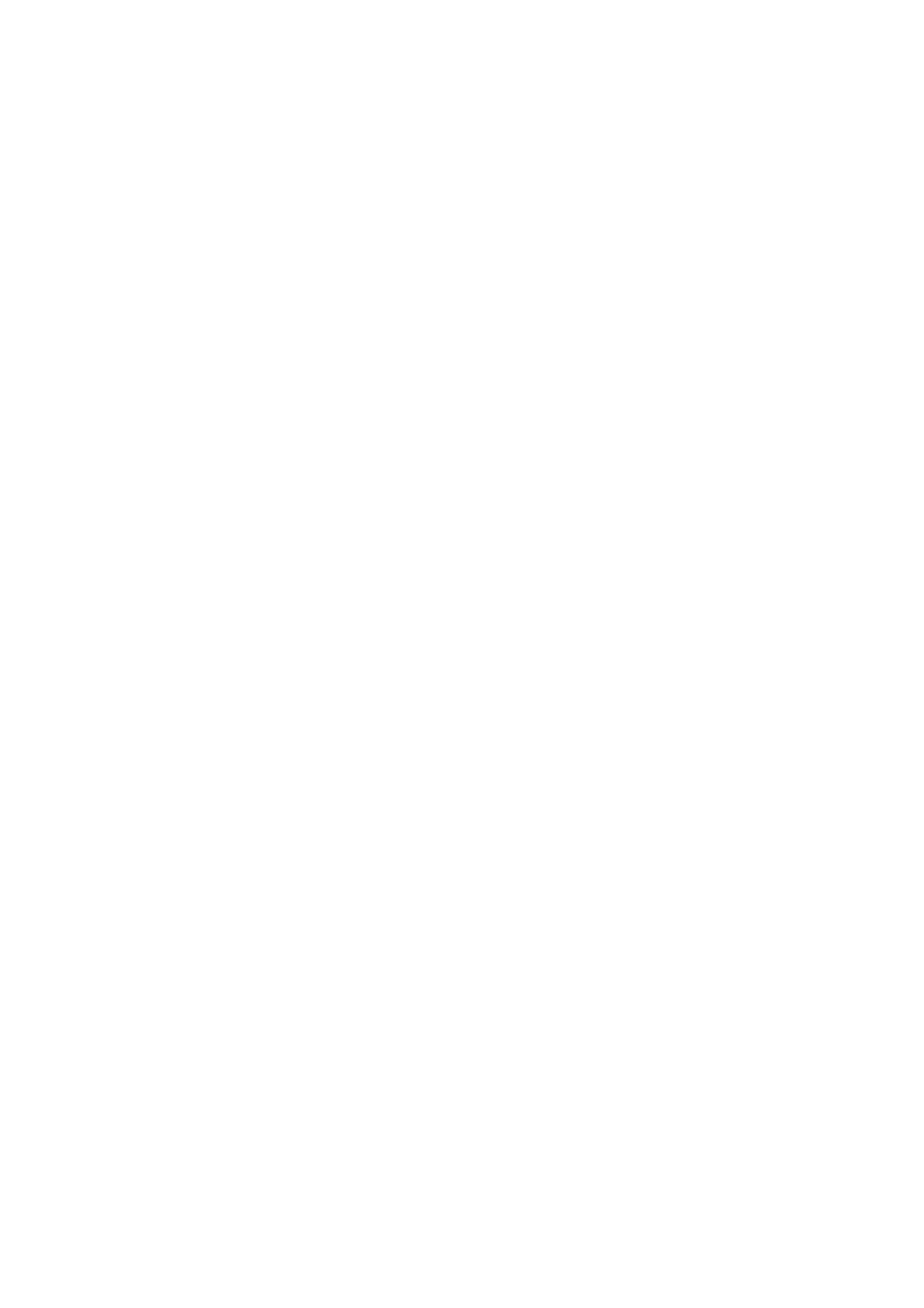
The Fulton Companies*FB-S Series Manual*Version 2010-0820 rev. 3/5/13
Page 23
only in the boiler proper, but also in pre-boiler equipment such as ecomomizers,
feedwater tanks, and feedwater lines.
b) Sodium Sulfite: Its purpose is to chemically remove the dissolved oxygen left in
the feedwater after the feedwater has been mechanically deareated. Sodium
Sulfite reacts chemically with dissolved oxygen, producing sodium sulfate. Since
it is desirable to remove dissolved oxygen from the feedwater before it reaches a
boiler. Sodium sulfite is best introduced continuously at some suitable point in the
feedwater system (the storage section of the feedwater heater or deareator, six
inches below the water line). Chemical residual control is based on the
maintenance of a specific excess of sodium sulfite in the boiler water. The
essential requirement being to maintain in the feedwater at all times slightly more
than enough sodium sulfite to consume all of the dissolved oxygen that slips
through the deareating equipment. Sulfite as a treatment represents the second
line of defense against oxygen corrosion. Primary protection against this type of
attack requires adequate facilities for mechanical deareation of the feed-water
plus a vigorous maintenance program to safe guard against oxygen leakage into
the pre-boiler system.
c) Suspended Solids: Suspended solids are the undissolved matter in water, inc-
luding dirt, silt, vegetation, iron oxides, and any other insoluble matter. Normally
suspended solids are expressed in terms of turbidity. Suspended solids may also
deposit in low velocity areas and create fouling. In line filters, or various types of
pretreatment can be used to lower the suspended solids level. Various polymers
assist in holding solids in suspension. Periodic blowdowns will eliminate
suspended solids.
d) Alkalinity: Alkalinity is the capacity of a water to neutralize acids. Common water
alkalinities consist of bicarbonate, carbonates, hydroxide, phosphate, and
silicate. These alkalinities, especially bicarbonates and carbonates, break down
to form carbon dioxide in steam, which is a major factor in the corrosion on
condensate lines. High alkalinity also causes foaming and carry over in boilers.
Both foaming and carry over cause erratic boiler operation. When foaming occurs
an antifoam should be added or increased. The reason for the high alkalinity
should be determined. It may result from lack of sufficient blow off. Quite often
the source of alkalinity is an overdose of alkaline internal water treatment
chemical.
e) pH: pH is a measure of the degree of acid or base of solution. pH ranges of 8.0-
10.5 will have little influence on the corrosion rate of carbon steel. A low pH can
result in corrosion of metals, while a high pH can result in scale formation or