Brooks, Model 5850e, Table 4-1 bench troubleshooting – Brooks Instrument 5850E User Manual
Page 36
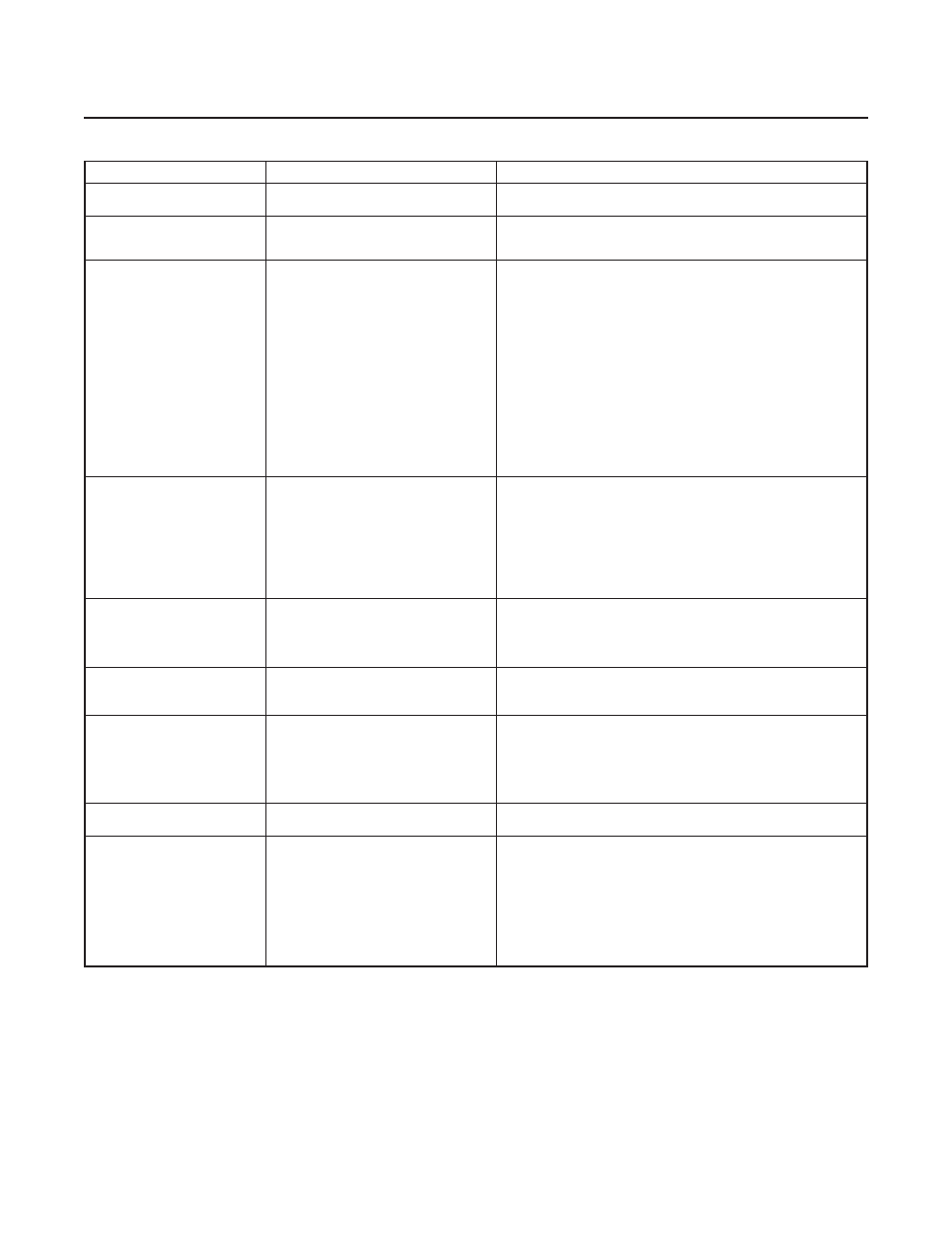
4-4
Installation and Operation Manual
X-TMF-5850E-MFC-eng
Part Number: 541B102AAG
September, 2009
Section 4 Maitenance &
Troubleshooting
Brooks
®
Model 5850E
Trouble
Possible Cause
Check/Corrective Action
Actual flow overshoots setpoint by
Anticipate potentiometer out of adjustment.
Adjust anticipate potentiometer. Refer to Section 3-5 .
more than 5% full scale.
Output stays at 0 Volts regardless
Clogged Sensor. Refer to Section 4-4.
Clean sensor. Refer to cleaning.
of command and there is no flow
through the controller.
Output stays at 0 Volts regardless of
Clogged Control Valve
Check TP3 with the command valve at 100%. If the voltage is more negative than
command and there is no flow through
-11V for NC Valve or +11V for NO Valve, disassemble and repair the control valve.
the controller.
Refer to Section 4-4C and 2-10.
Card Edge Version internal reference
Refer to Section 2-12.
is being used as the command source and
the yellow jumper is in the E-F position.
-15 Volts applied to the valve override input
Check valve override input. Refer to Figures 2-3 & 2-4 for terminal assignments.
Defective printed circuit board
Replace printed circuit board. Refer to Section 4-4.
Valve voltage not returned, pin L at common.
Check jumper for external valve return. Refer to Section 2-12.
"Valve-off" pin grounded.
Check "Valve-off" input. Refer to Figures 2-3 and 2-4 for terminal assignments.
Output signal stays at +6.8V regardless
Valve stuck open or leaky.
Clean and/or adjust control valve. Refer to cleaning procedure and/or Section 4-4C.
of command and there is flow
through the controller.
+15V applied to the valve override input.
Check the valve override terminal. Refer to Figures 2-3 & 2-4 for terminal assignments.
Detective printed circuit board.
Replace printed circuit board. Refer to Section 4-4.
Command input floating.
Connect command signal. Refer to Figures 2-3 and 2-4 for terminal assignments.
Pin D connected to common.
Remove Pin D from common.
Output signal follows setpoint
Leaky control valve
Disassemble and repair valve. Refer to Section 4-4C.
at higher commands but will not go
to zero.
Excessive resistance in valve voltage
Reduce wiring resistance or re-configure controller for "External Valve Return:.
Refer to Section 2-12.
Output signal follows setpoint
Insufficient inlet pressure or pressure drop.
Adjust pressure, inspect the filters and clear/replace as necessary.
at lower commands but does not reach
full scale.
Partially clogged sensor.
Check calibration. Refer to Section 3-4.
Partially clogged valve.
Disassemble and repair control valve. Refer
to Section 4-4.
Valve out of adjustment.
Adjust valve. Refer to Section 4-4.
Valve guide spring failure.
Controller oscillates (see below).
Controller grossly out of calibration.
Partially clogged sensor.
Clean sensor, refer to the cleaning procedure.
Flow is higher than desired.
Controller grossly out of calibration.
Partially clogged restrictor.
Replace restrictor. Refer to Section 4-4.
Flow is lower than desired.
Controller oscillates.
Pressure drop or inlet pressure excessive.
Adjust pressures.
Oversized orifice.
Check orifice size. Refer to Section 4-6.
Valve out of adjustment.
Adjust valve. Refer to Section 4-4.
Anticipate potentiometer out of adjustment.
Adjust anticipate potentiometer. Refer to Section 3-5.
Faulty pressure regulator.
Check regulator output.
Defective printed circuit board.
Replace printed circuit board. Refer to Section 4-4.
Table 4-1 Bench Troubleshooting
An alternate method for flushing out the sensor is to replace the
restrictor element with a low flow plug restrictor. This plug forces all the
flow through the sensor and may dislodge any obstructions. With the
valve orifice removed, subject the flow controller to a high differential
pressure. Pressurizing the outlet of the MFC higher than the inlet may
help force the obstruction upstream and out of the sensor tube.
4. Inspect the orifice for clogging by holding it in front of a light source and
looking for light through the bore. Clean by soaking in a suitable non-
residuous solvent and directing a stream of compressed clean, dry
Nitrogen through the bore.