Brooks, Model 5850e – Brooks Instrument 5850E User Manual
Page 27
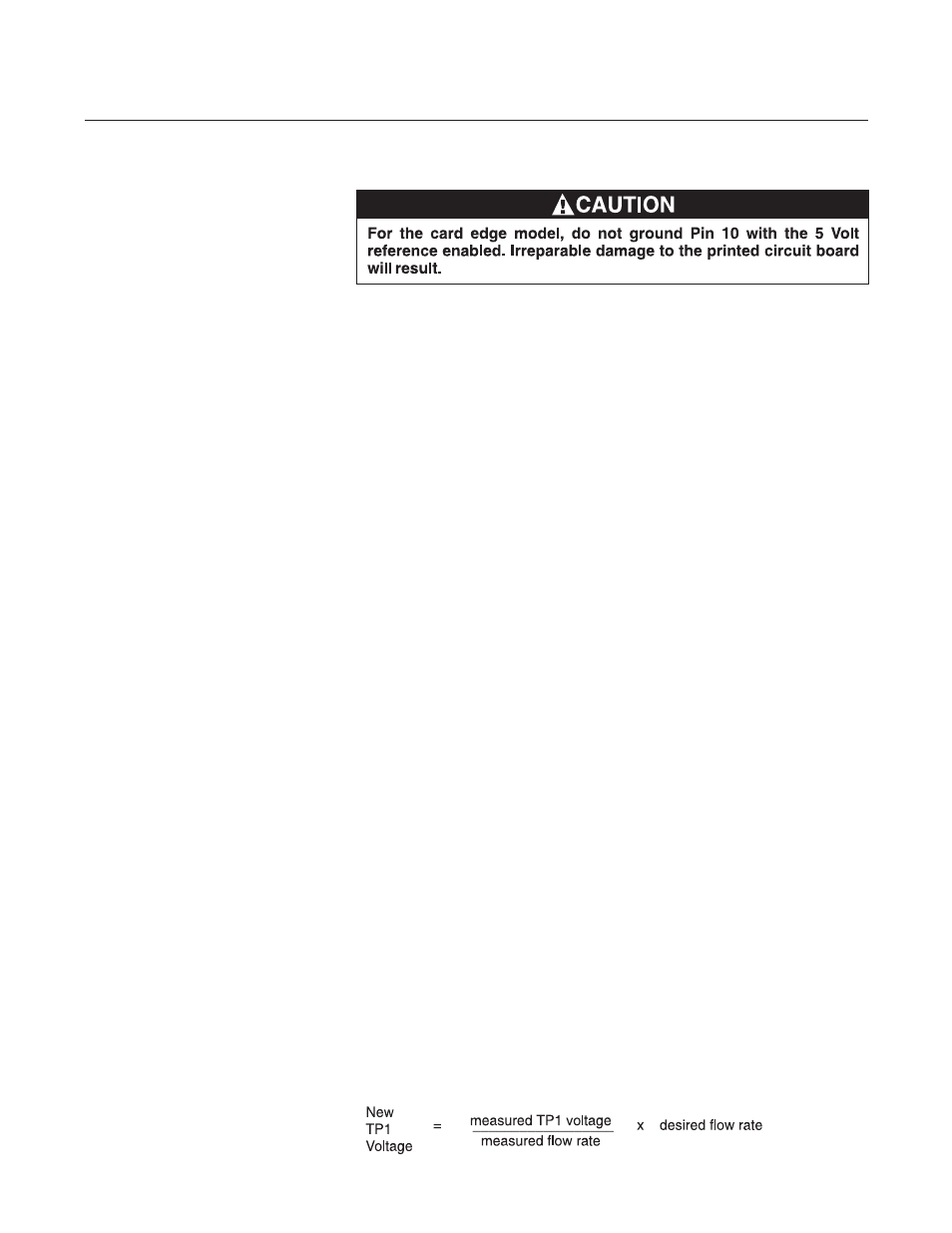
Brooks
®
Model 5850E
3-7
Section 3 Operation
Installation and Operation Manual
X-TMF-5850E-MFC-eng
Part Number: 541B102AHG
September, 2009
orifice for actual operating conditions.
Note 4: If Brooks’ secondary electronics are being used as a power supply
during the calibration, the 5 Volt reference must be enabled on the Card
Edge version for proper operation (see Section 2-13). Remember to
deactivate the 5 Volt reference before installing the calibrated mass flow
controller in the system where Terminal 10 is grounded.
a. With the controller installed in an unpressurized gas line, apply power
and allow approximately 45 minutes for warm-up. During the warm-up,
adjustment and calibration check procedures do not allow the control
valve to open when gas flow is not present. This situation is not a
normal operating mode and will cause abnormal heat-up of the control
valve. With this abnormally warm valve, the meter will be difficult to
calibrate. This situation can be prevented by switching the valve
override “closed” when there is no gas flow or by setting the command
to less than one percent (1%). Also, avoid unnecessary periods with the
valve override “open.”
b. Adjust the anticipate potentiometer with 20 clockwise full turns. Next,
adjust the anticipate potentiometer with 10 counterclockwise turns to
center the potentiometer. This will provide a rough adjustment of this
circuit and make the flow more stable for calibration.
c. Connect the DVM positive lead to the 0-5 Volt signal output (Terminal 3
Card Edge, Pin 2 D-Connector) and the negative lead to signal com-
mon (TP4). Adjust the zero potentiometer for an output of zero mV ±2
mV.
d. Apply pressure to the system and insure that the zero signal repeats
within 2 mV of the voltage set in Step “c” above. If the zero does not
repeat, check for leakage.
Note: Controllers supplied with all metal or Teflon valve seats do not
provide tight shut-off. A 0-8% leak-through is typical. For metal or Teflon
seat controllers, close a downstream shut-off valve and observe the
zero signal.
e. Set the command potentiometer (connected to terminals A, B and 10 of
the Card Edge connector and Terminals 1, 8 and 11 of the D-Connec-
tor) for 100% of flow (5.000V). Connect the DVM positive lead to TP2
(linearity voltage) and the negative lead to TP4 (signal common). Adjust
the linearity potentiometer for an output of 0.0V (zero volts).
f. Connect the DVM positive lead to TP1 (-100x sensor voltage) and the
negative lead to TP4 (circuit common). The command potentiometer
should still be set at 100% flow (5.000V). Measure the flow rate using
suitable volumetric calibration equipment. To adjust the controller to the
proper full scale flow, calculate a new TP1 voltage using the following
equation: