Anchoring switchgear equipment – GE Industrial Solutions Entellisys Installation User Manual
Page 39
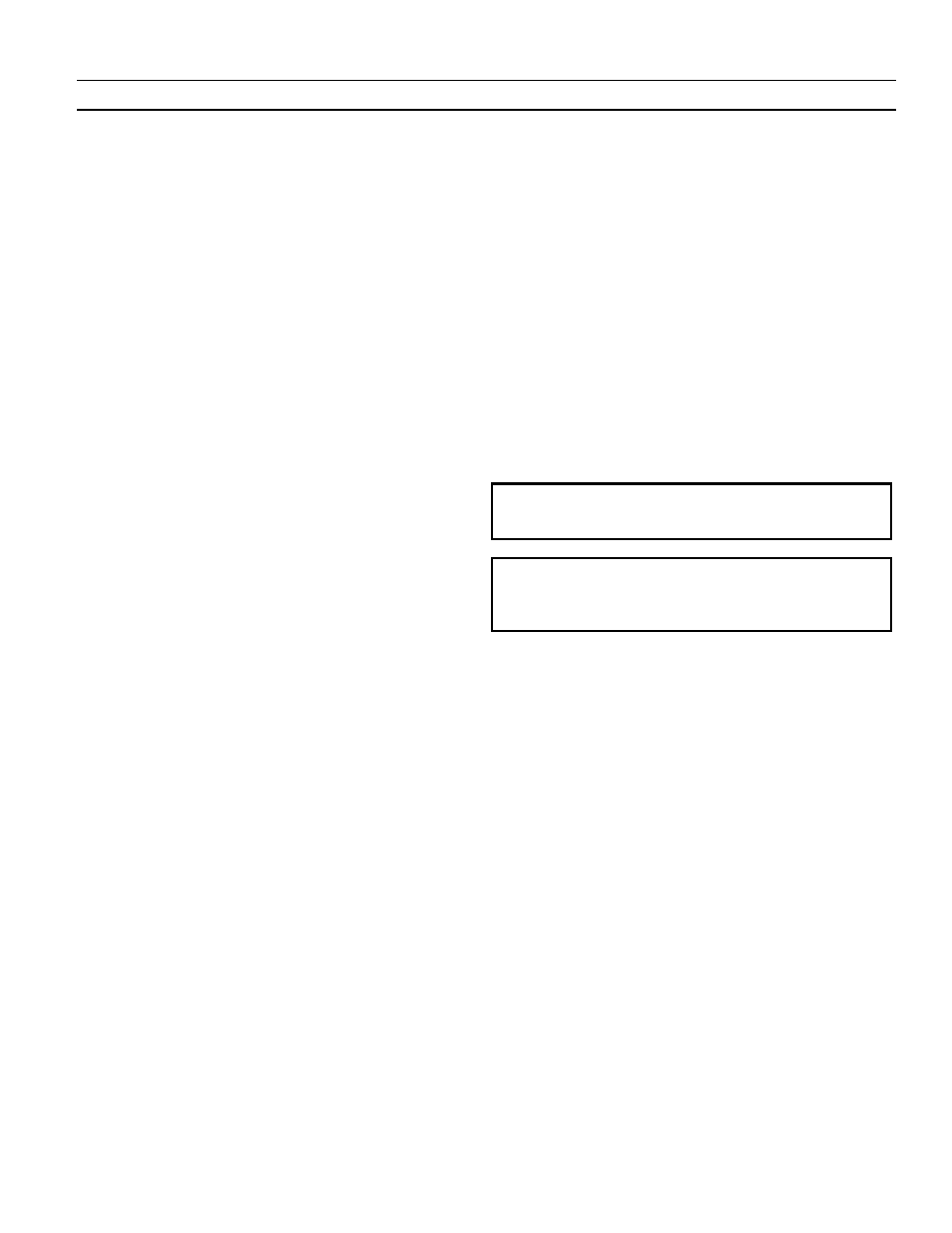
33
Entellisys Low Voltage Switchgear
Chapter 4. Equipment Installation
Anchoring Switchgear Equipment
Correct anchoring of the switchgear equipment to the
foundation is very important. After completion of re-
assembly of the equipment at the shipping splits, the
equipment anchoring procedure should be completed.
1.
ANCHORING BY ANCHOR BOLTS – Equipment is
normally secured to its final mounting surface by
anchor bolts threaded into the embedded channel sills.
The bolts were loosely threaded into place before
reassembling the equipment shipping splits and
connecting to the close-coupled transformer, if
appropriate.
The anchor bolts should now be tightened with a torque of
35-40 ft-lbs.
2.
ANCHORING BY WELD - An alternate method of
anchoring the equipment to its foundation is to weld
the equipment to floor sills (or the floor itself if
constructed of steel). Several methods, shown on Fig. 4-
15, are available to the purchaser for welding the
equipment to the channel sills.
a. The front of the equipment
is attached to the
embedded channel sills (1), Fig. 4-15, by two 3/16-
inch fillet welds (2). It is recommended that two
welds, each 2-1/2 inches long (min.), be used for each
section to firmly tie the bottom width post (3) to the
channel sill.
b. The rear of the equipment
may be anchored by one of
three procedures:
•
The first method is by plug welds (4), Fig. 4-15, using the
anchor bolt holes in the rear sill angle (5). The plug weld
should receive a minimum 1/2-inch bead around the
entire circumference of the anchor bolt hole.
•
A second method of securing the rear sill angle (5) to the
channel sill (1) is the use of two linear fillet welds (2) for
each section. It is recommended that each weld be 2-1/2
inches long (min.) with a 3/16-inch fillet (min.).
• A third method for anchoring the rear of the equipment is
to remove the rear sill angle (5) from the switchgear and
weld the rear bottom width post (6) to the channel sill (1).
These welds (2) should, like the front welds, have a 3/16-
inch
(min.) fillet and each have a minimum length of 2-1/2
inches.
CAUTION: If the equipment is to be subjected to
operational or environmental (seismic) shock loading, the
factory must be consulted for anchoring recommendations.
ATTENTION: Si l’équipement doit être assujetti à une
charge de choc opérationnelle ou environnementale
(sismique), il faut consulter le manufacturier afin d’obtenir
des recommandations d’ancrage.