Boiler operating history, Chemical additive for slag control – GE P&W FuelSolv - Slag Control Treatment Program at EKPC Spurlock Station User Manual
Page 2
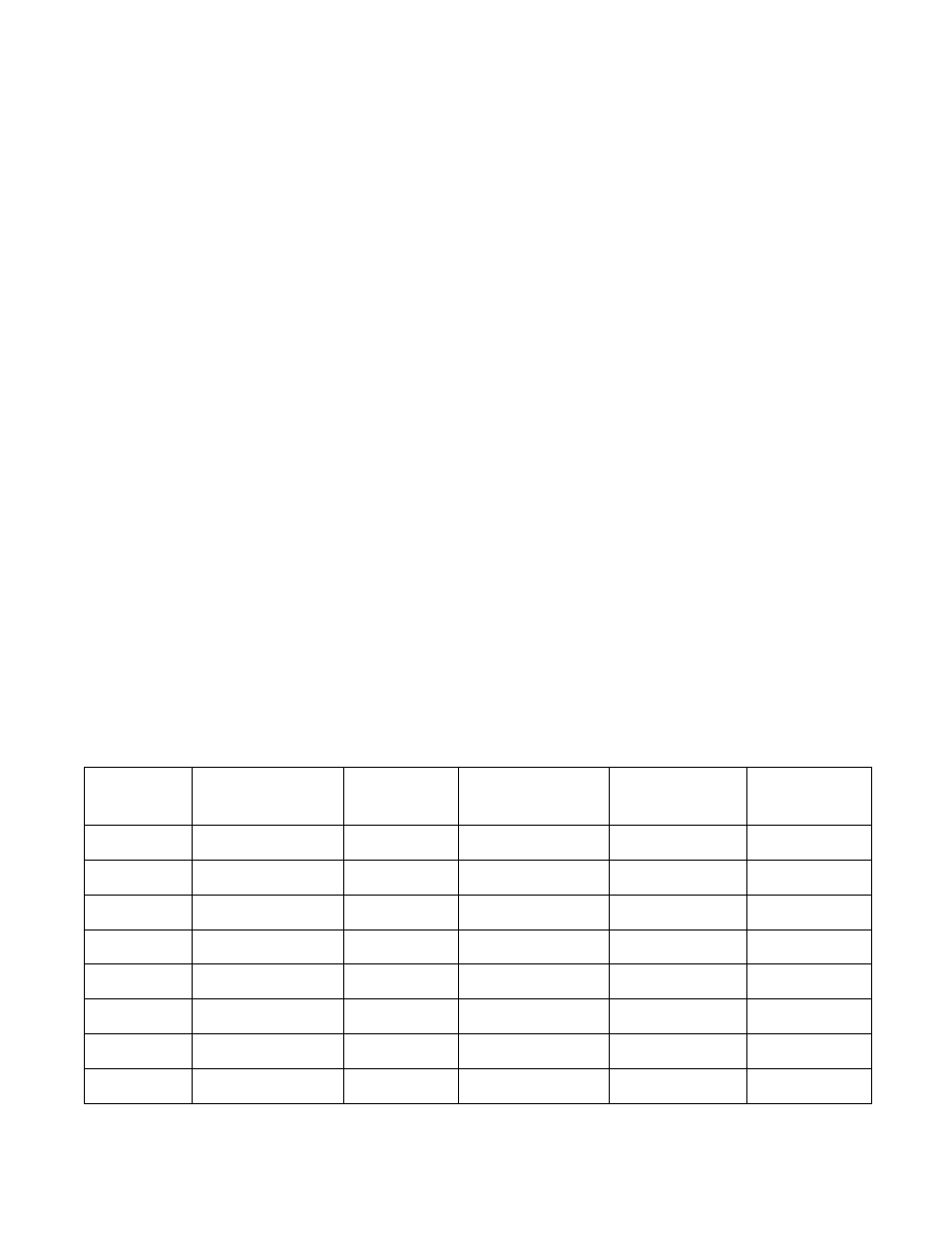
Page 2
Technical Paper
The impact of slagging and fouling can be costly.
The lost economics can be the result of unit derates,
unscheduled outages, high cleaning cost, repair
costs from slag fall damage, and incremental costs
associated having to burn more expensive fuels.
Chemical additives in combination with mechanical
ash removing devices can improve control of slag-
ging and fouling deposits on the fireside of the boiler
and reduce their overall negative impact.
Boiler Operating History
Spurlock Station boilers 1 and 2 are sub-critical boil-
ers with a capacity of 340 MW and 585 MW respec-
tively. Unit 1 is a B&W opposed wall-fired design
while Unit 2 is a CE T-fired design. The scrubber for
Spurlock Unit 2 became operational in October of
2008 while the scrubber for Unit 1 became opera-
tional in June of 2009. Installing the scrubbers al-
lowed Spurlock to switch from low-sulfur
compliance coal to high sulfur Illinois Basin coal.
Cost advantages of high sulfur Illinois Basin coal
were significant, however there were concerns that
slagging tendencies would increase significantly.
Operating experience in 2009 showed that burning
100% of Illinois Basin (ILB) Coal-A caused a severe
slagging situation that resulted in the formation of
large clinkers on the bottom of Pendant Platen
Superheat assemblies on Unit 1. Severe slagging
caused bridging across RH assemblies, blockage of
gas lanes, costly de-rates and slag falls and resulted
in unscheduled outages for off-line cleaning on Unit
2. Also, clinkers that did form were much more
difficult to grind in the bottom ash grinding opera-
tion. Operating experience also showed that un-
der operating conditions of 100% of Coal-A,
conditions could deteriorate in a matter of a few
days. In order to minimize the impact of the high
sulfur ILB coal, Spurlock Station opted to blend
their high sulfur, high slagging index coal with
lower sulfur, higher cost coal. Table 1 shows the
plants typical fuel sources, tonnage and relative
cost.
Chemical Additive for Slag Control
Fuelsolv* FMG2960 is a highly concentrated oil
based liquid additive that contains a proprietary
blend of magnesium and copper based com-
pounds. Its primary use is to inhibit slag build up
on the radiant sections of the boiler (furnace walls,
nose arch, radiant superheaters, and finishing su-
perheaters). It works by altering the sintering
characteristics of slag. The FMG2960 is fed directly
to the coal, which greatly simplifies the feed.
Transition metals and other multivalent metals
such as copper have been used for many years as
combustion catalysts. Not as well known is that
copper, in combination with magnesium, can be
an effective slag control agent and acts to reduce
the cohesive strength of ash particles. If the cohe-
sive strength is reduced, the ash becomes more
friable and easily removed by soot blowing and
operational load shedding.
Coal Source
Relative Price,
$/MMBTU
Heat Value,
BTU
Sulfur Content
lb/MMBtu
Slagging Index
Tons/ Month
Coal-A
$0.0000
11,200
6.79
2.81
45,000
Coal-B
$0.1995
12,500
4.13
0.95
30,000
Coal-C
$0.2466
11,300
5.21
1.50
15,000
Coal-D
$0.3463
11,300
5.21
1.50
25,000
Coal-E
$0.5011
11,000
5.92
1.50
30,000
Coal-F
$0.6343
12,200
6.57
2.01
20,000
Coal-G
$0.8309
11,500
4.05
0.89
20,000
Coal-H
$1.8857
11,500
4.87
1.13
20,000
Table 1