GE P&W FuelSolv - Slag Control Treatment Program at EKPC Spurlock Station User Manual
Abstract, Discussion
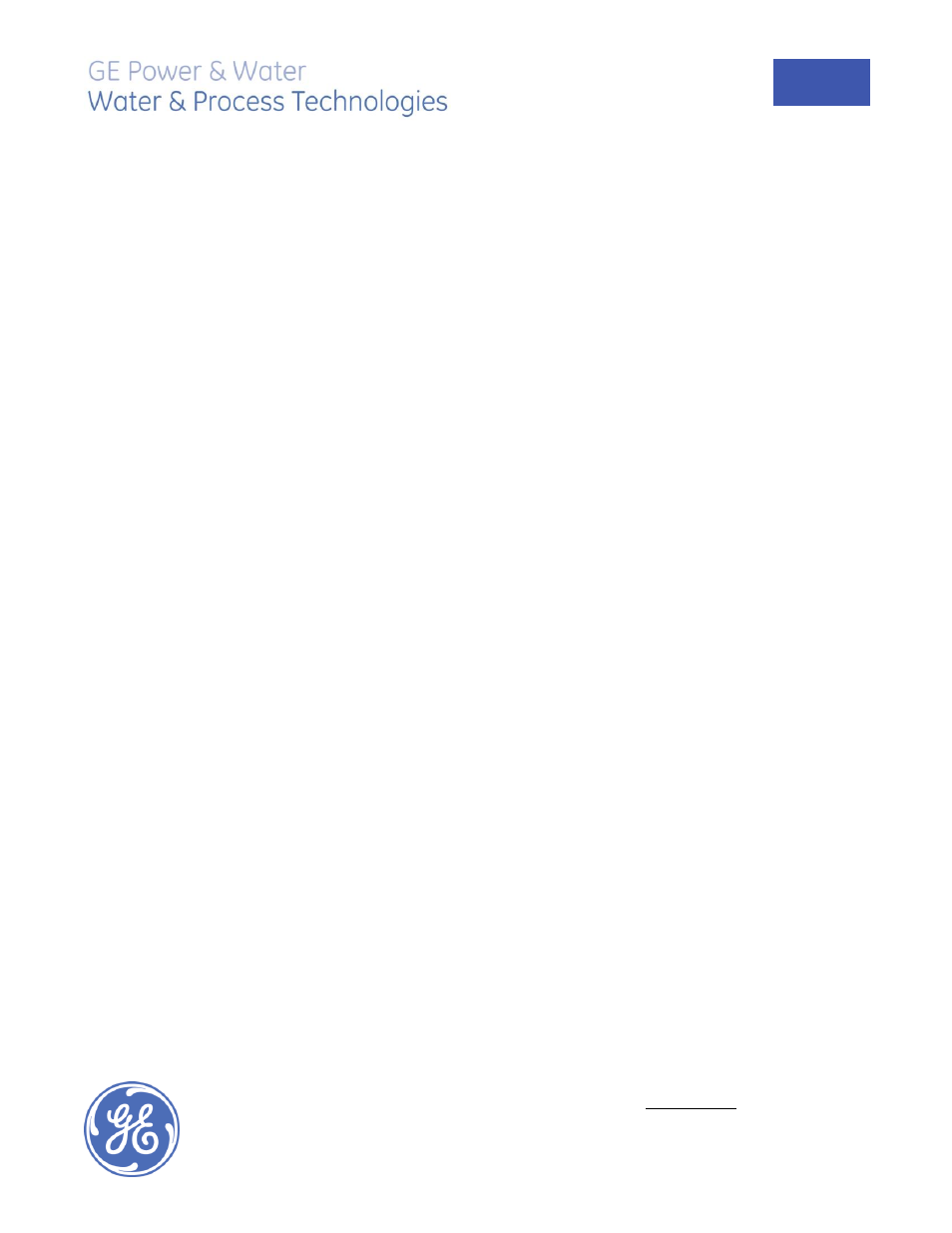
Find a contact near you by visiting www.ge.com/water and clicking on “Contact Us”.
* Trademark of General Electric Company; may be registered in one or more countries.
©2011, General Electric Company. All rights reserved.
TP1190EN.doc Jul-11
Technical
Paper
Slag Control Treatment Program at EKPC
Spurlock Station
Authors:
Mark Gabriel, Manager, Business Development, GE
Water & Process Technologies
Logan Pickrell, Process Engineer, East Kentucky
Power Cooperative
Abstract
Coal burning power plants today are challenged by
economic slowdowns and lower prices for the elec-
tric power they produce. With reduced power prices,
many power companies are looking to stay compet-
itive by burning lower cost, lower quality fuels.
Switching fuels can often be more difficult for the
plants to burn. Moreover, the most efficient and low
cost producing plants are being kept at higher load
for longer periods of time than ever before. The
changes in fuel quality and boiler operation have
caused many plants to experience an increase in
slag deposits on the furnace walls and superheater
sections of their boilers.
Spurlock Station boilers 1 and 2 are sub-critical boil-
ers with a capacity of 340 MW and 585 MW respec-
tively. Both units currently burn 100% Illinois Basin
coal. Illinois Basin coal is high sulfur, low fusion
temperature coal. Burning some Illinois Basin coals
would create a buildup of hard slag formation inside
the boiler. Typical issues included the formation of
large clinkers on SH assemblies. Spurlock Station
has experienced large slag falls causing boiler dam-
age and safety concerns.
In January of 2010, Spurlock started treating their
boilers with a unique GE Water & Process Technolo-
gies chemical additive to reduce the detrimental
effects of burning high slagging index, low fusion
temperature coal. This paper describes how the
evaluation was conducted and summarizes the
boiler performance results.
Discussion
In addition to carbon, hydrogen and oxygen found
in coal, there are numerous inorganic impurities
that are not combustible and contribute to slag-
ging and convective pass fouling in the boiler.
These inorganic constituents impact the ash fu-
sion temperatures. Fusion temperatures often
can correlate directly to the tendency for slag
formation in the boiler. Slag deposits form when
boiler fireside temperatures exceed the fusion
temperature of the ash.
Slag density increases with time and temperature,
creating a deposit that is hard and difficult to re-
move with normal sootblowing. If the sootblowers
cannot remove the ash build up from the upper
areas of the boiler in a timely manner, the slag
deposits can continue to grow, harden, and form
to an enormous size. These slag deposits typically
form on the leading edge of the platen superheat
tubes, secondary superheater tubes or pendant
reheat tubes located above the furnace or above
the bull nose of the boiler. When the slag eventu-
ally does fall, it can puncture slope tubes or dam-
age entire sections of the lower furnace, forcing
unscheduled downtime and lost generation.
Fouling deposits may also form in the convective
back-pass sections of the boiler by condensation
of gaseous ash components. Fouling deposits are
typically associated with the Vertical Reheater,
Primary Superheater, and Horizontal Reheater
tubes. Fouling deposits can bridge across these
tubes and restrict gas flow to the point of furnace
plugging off. Fouling may result in a Unit derating
on load, or force the boiler to be shut down for a
cleaning.