Installation guide, Troubleshooting – Veris Industries H8036 SERIES Install User Manual
Page 10
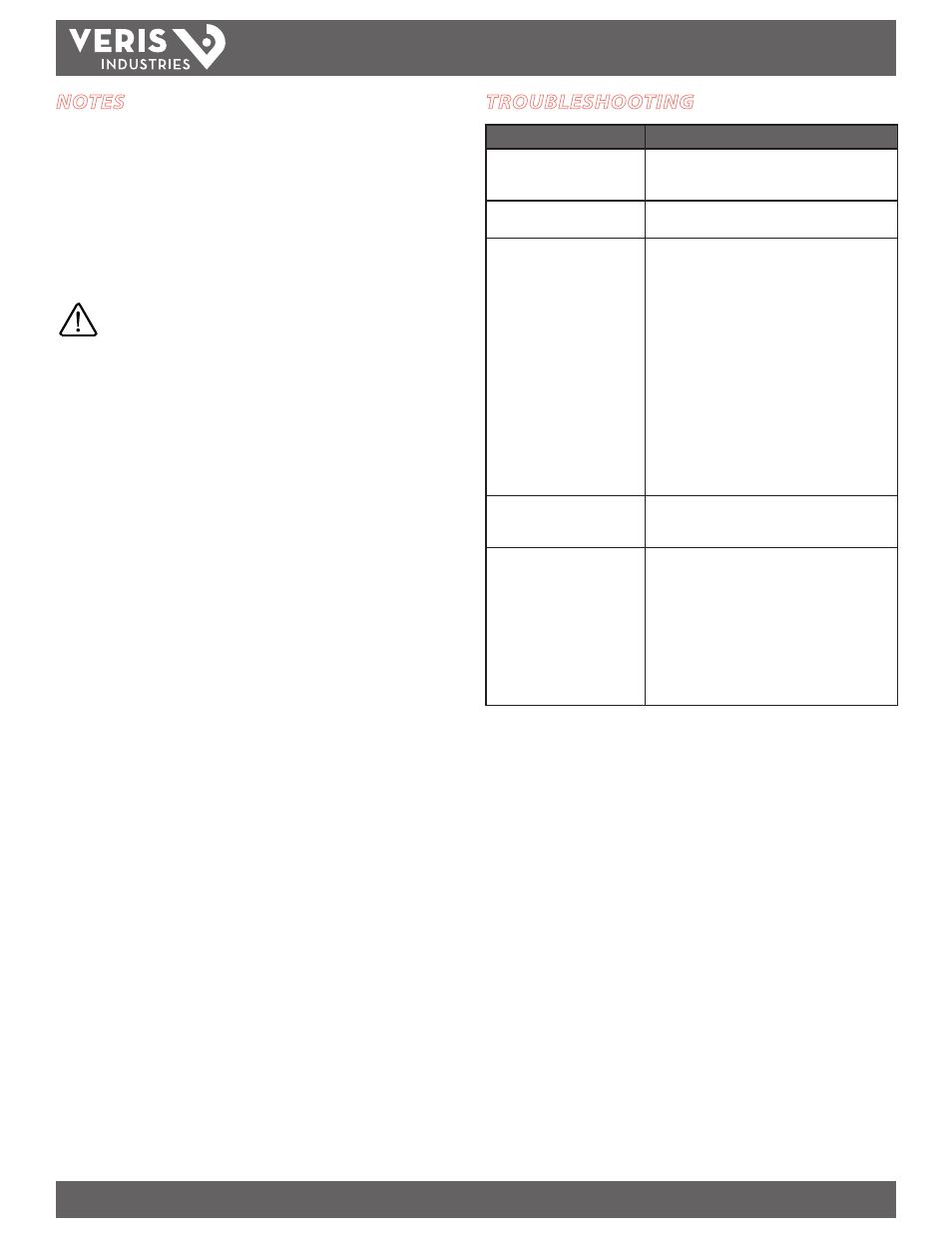
Z201686-0N
PAGE 10
©2012 Veris Industries USA 800.354.8556 or +1.503.598.4564 / [email protected]
08122
Alta Labs, Enercept, Enspector, Hawkeye, Trustat, Veris, and the Veris ‘V’ logo are trademarks or registered trademarks of Veris Industries, L.L.C. in the USA and/or other countries.
TM
H8035/H8036
INSTALLATION GUIDE
TROUBLESHOOTING
Problem
Solution
Status LED does not blink
Check fuses and voltage connections. Status LED should
blink regardless of CTs, Modbus connections, and DIP
switch setting.
Enercept interferes with another
device on the Modbus network
Set DIP switches to a different Modbus address not in
use.
Readings seem highly inaccurate. • Check that each CT is installed on the conductor with
the corresponding color voltage input lead attached. In
most cases, incorrect wiring will cause the Status LED
to blink red (slowly). However, a power factor lower
than 0.5 could cause the LED to blink this way, even if
the unit is installed properly.
• It does not matter which side of the CT faces towards
the load.
• If current is below 7% of full scale maximum for the
CT, use a smaller CT or wrap each wire through the CT
multiple times
• Check current with an amp-clamp.
Expected power:
kW = Volts x Amps x 1.732 x PF / 1000
kW = Horsepower x 0.746
PF is usually 0.7 to 0.95, depending on the load.
Enercept goes offline when load is
switched off.
Connect voltage leads on the Line side of the conductor.
The Enercept cannot communicate on the Modbus
network without voltage.
Status LED blinks red.
• If the LED blinks quickly (i.e., about 5 blinks in two
seconds), then use a CT with a higher amp rating.
• If the LED blinks slowly (i.e., about 1 blink per
second), then the CTs are not installed on the correct
conductors or the power factor is less than 0.5. The
Enercept can accurately measure these low PFs, but
few loads operate normally at such a low power factor.
• If the LED blinks slowly (i.e., about 1 blink per
second), the monitored load might be less than 10%
of the CT maximum ratings.
NOTES
1. DO NOT GROUND THE SHIELD INSIDE THE ELECTRICAL PANEL. Insulate all Modbus
wires, including the shield, to prevent accidental contact with high voltage
conductors.
2. Mechanically secure the Modbus cable where it enters the electrical panel.
3. Connect all Modbus devices in a daisy-chain fashion. Use a 120 Ω terminating
resistor between (+) and (-) on the first and last devices in the chain.
4. Use shielded twisted pair wire BELDEN 1120A or similar for the Modbus cable.
WARNING: After wiring, remove all scraps of wire or foil
shield from the electrical panel. This could be DANGER-
OUS if wire scraps come into contact with high voltage
wires!