Motor brake control wiring – Parker Products ViX250AE User Manual
Page 42
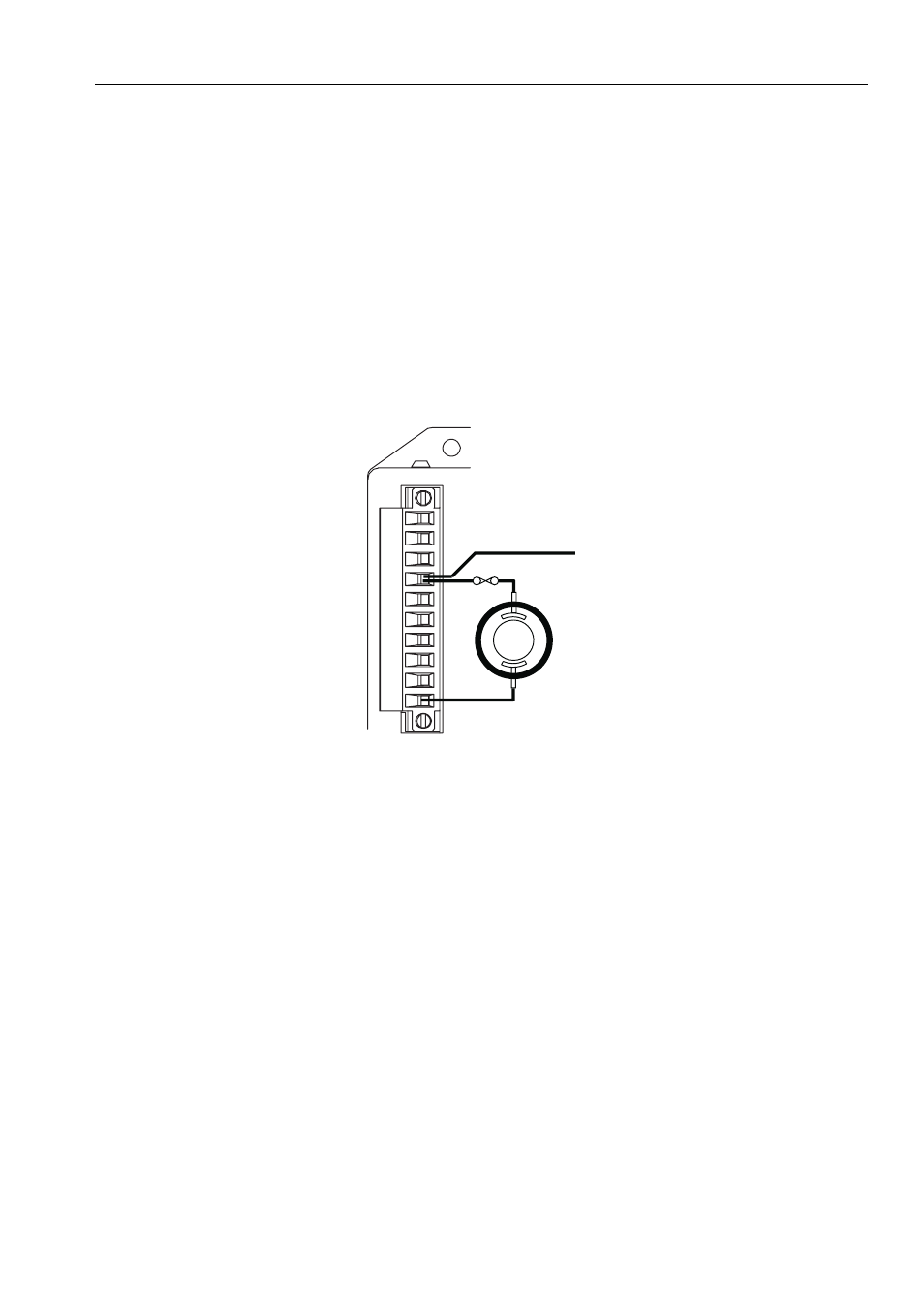
3. ELECTRICAL INSTALLATION 35
Motor Brake Control Wiring
Certain motors used with the ViX drives can be fitted with a holding brake. This enables
vertical (Z-direction) loads to be held whilst the motor is de-energised.
All brakes are fail-safe, that is you need to apply power to the brake to keep it disengaged.
Removing power from a brake will engage or activate the brake preventing further shaft
motion.
Figure 3-18 shows the connections necessary to control a motor holding brake. Power the
brake from the 24V supply, a 2A fuse is recommended to protect the circuit from wiring
faults. To release the brake, (allowing the motor shaft to turn) connect pin 1 of X1 to ground,
using the manual BRAKE command.
X1
24V DC
24V DC
SUPPLY
MOTOR BRAKE
IN ITS RELEASED
OR ENERGISED STATE
9
2A FUSE recommended
8
7
6
5
4
3
2
BRAKE
10
1
Power & motor
10-way
connector
Figure 3-18. Motor Holding Brake Connections
See Section 4. Control of ViX Drives - Brake Operation for details of how to control its
operation.
When a brake is used, the brake supply is dependent upon the value of HV.
For the majority of applications where the HV is greater or equal to 30V, the fused brake
supply is taken from the 24V supply at X1 pin 7 (as shown above).
For applications where the HV is less than 30V, the brake supply can be taken from the
motor HV supply at X1 pin 10.
Note: Whenever you change the HV supply you will need to run the motor configuration
command. If there is no motor HV present, issuing the motor command assumes a value of
80V.