Introduction – MicroBoards Technology HCL-6000 User Manual
Page 5
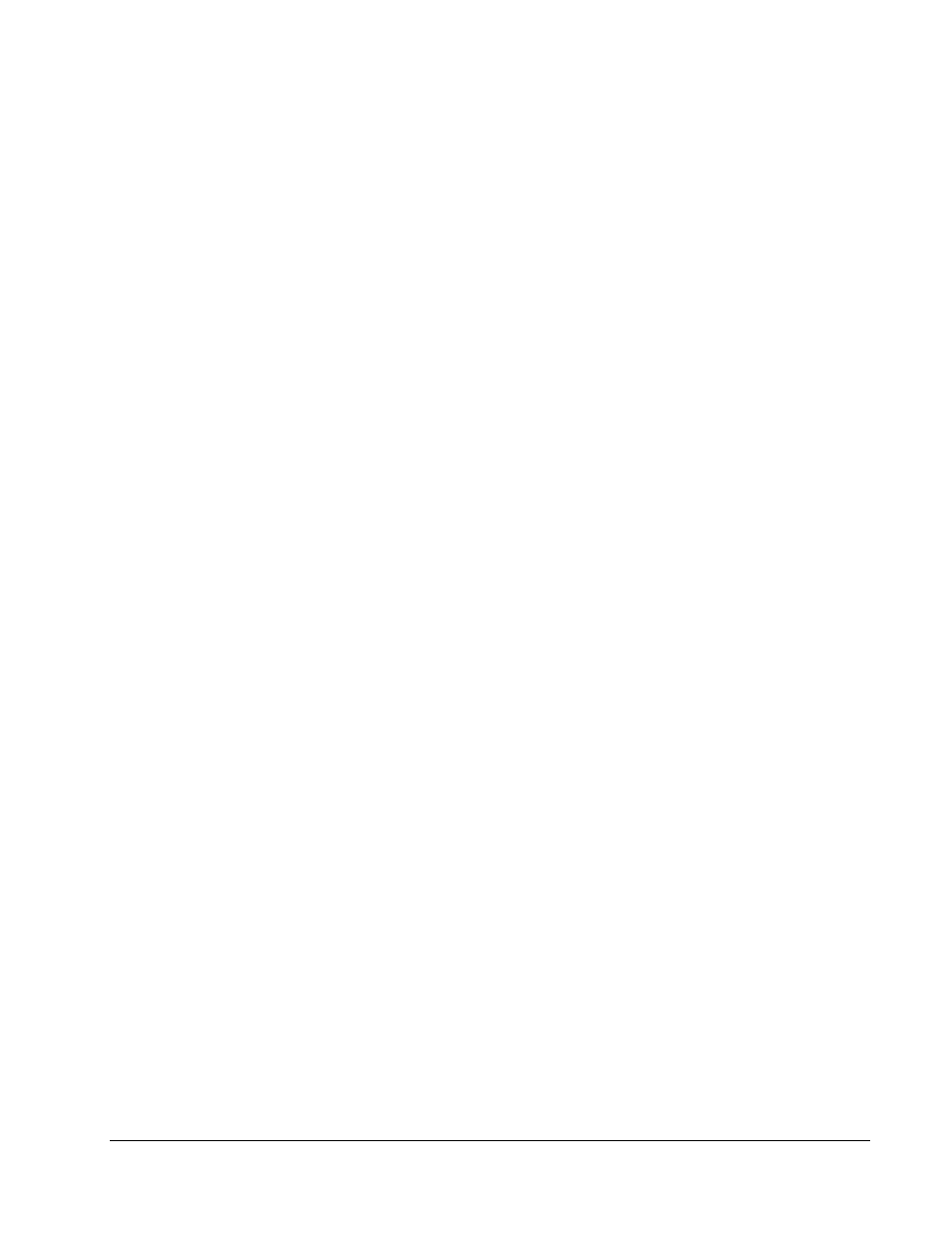
MICROBOARDS TECHNOLOGY, LLC HCL Series
5
Introduction
The Microboards HCL Series autoloader is a reliable, high performance, high speed, standalone, robotic DVD
and/or CD autoloader. With its professional industrial design and simple user interface, it makes your
duplicating experience easier than ever.
With the Microboards HCL Series, you can have a capacity up to 1000 discs, duplicate continuously for 24
hours (even with multiple masters), and get the highest quality duplication, all at an extremely affordable
price.
The Microboards HCL Series includes the HCL-4000, HCL-6000, and HCL-8000, with 4, 6, and 8 drives,
respectively. The number of drives will not affect the overall capacity of the HCL Series autoloader. More
drives, however, will result in increased throughput.
Before you start using this autoloader, please read the following to ensure proper operation:
DVD Duplication Limitations
DVD masters must be copied to blanks of the same capacity. In other words, DVD Dual-Layer must be
copied to DVD Dual Layer, and DVD Single Layer must be copied to DVD Single Layer.
DVD +R media does not support Test mode and will be burned if used.
Temperature Warning
If the autoloader was stored in a location where the temperature dropped below 32° F (0° C) within the past
24 hours, leave the autoloader in a warm room with temperatures at least 65° F (19° C) for four hours prior to
powering it on for the first time. Failure to do so may cause irreparable harm and prevent the autoloader from
functioning.
Maintenance
Dust is the number one killer of CD/DVD recording devices. It is very important to operate the autoloader in a
dust free, clean environment. Failure to do so can severely damage your autoloader. We strongly suggest
that you constantly use an Air Duster (Canned Air) to clear off any dust on the surface of the autoloader.
Note: Do not try to use an Air Duster to clean the autoloader while the writer trays are open. In doing so, you
may inadvertently blow dust into the recording device and damage it.
Proper Shutdown
To avoid possible system failures, you need to shut down the autoloader properly. To shut down the
autoloader, scroll to menu 15. Shutdown and follow the instructions on the screen. Not performing this
function increases the risk of damaging the autoloader.
Double Layer/Dual Layer Partition
If you have a 16x speed or higher autoloader with DVD Dual Layer capability, the hard drive partitions are set
to a default size of 9 GB each to accommodate DVD Dual Layer format. If you require more partitions and do
not plan on using DVD Dual Layer media, you can reduce the size of the partitions using the instructions
given in “Partition Size” on page 26. Keep in mind that if you alter the partition size, all previous data/video
stored on the hard drive will be lost and you will only be able to load media with less than 5 GB capacity such
as DVD Single Layer (4.7 GB), CD (700 MB), etc.
Disc Static and Sticky Media
The most common problems when using an autoloader are the disc static and sticky media issues. These
static charge problems cause multiple discs to stick together, resulting in improper operation and more
severely, can shock the robotic arm while loading a disc that causes the system
to
freeze. Even though the
autoloader has a sticky media separator function to prevent the sticky media, but you should still follow these
steps to prevent sticky media from disrupting your operation and protect your system from disc static charge.
This issue is most commonly seen when you buy a 100 pack of blank discs and insert them into the
autoloader without any treatment. If you have experienced this kind of problem, please do the following to
remove the adhesive static between the discs:
¾ Separate the blank discs before you place them into the autoloader's spindle(s). Separating them will
greatly reduce the static between discs.
¾ If this doesn't achieve the desired outcome, use an air duster (canned air) to blow air around the
circular edge of the blank discs. This process reduces the static between the discs up to 90%. The
amount of air to use depends on factors specific to your environment.