7 cable connections from mb-40r/emb-40r to robot, Installing the arm power/signal cable, Specifications for 24 vdc power – Adept s350 Cobra User Manual
Page 26
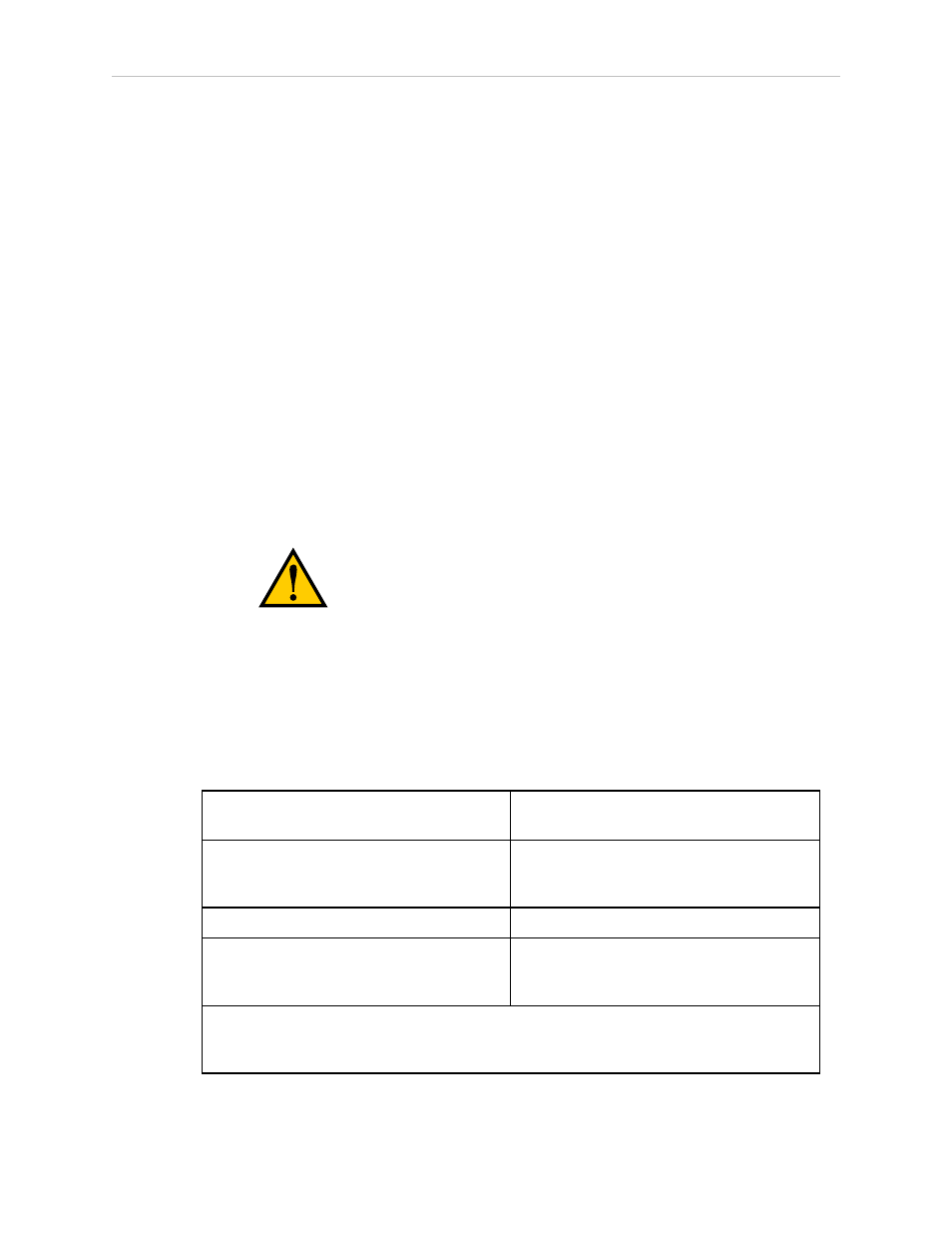
Chapter 3: System Cable Installation
eMB-40R: Install the eAIB XSYS cable between the XSYS connector on the
SmartController and the eMB-40R XSYSTEM connector, and tighten the latching screws.
If you are upgrading from an MB-40R to an eMB-40R, you can use an eAIB XSLV
adapter cable between your existing XSYS cable and the XSYSTEM connector on the
new eMB-40R.
NOTE: The IEEE 1394 and XSYS/eAIB XSYS cables should be routed away from AC
power and robot interconnect cables.
3.7 Cable Connections from MB-40R/eMB-40R to Robot
Installing the Arm Power/Signal Cable
The cable between the robot and the MB-40R/eMB-40R is called the Arm Power/Signal cable,
as shown in Figure 3-1.
1. Connect one end of the Arm Power/Signal cable to the CN22 connector on the back plate
of the robot. Tighten the thumb-screw securely.
2. Connect the other end of the cable to the large, circular connector on the MB-40R/eMB-
40R. Tighten the screws securely.
WARNING: Verify that all connectors are fully inserted
and screwed down. Failure to do this could cause
unexpected robot motion. Also, a connector could get
pulled out or dislodged unexpectedly.
3.8 Connecting 24 VDC Power to MB-40R/eMB-40R Servo Controller
Specifications for 24 VDC Power
Table 3-2. Specifications for 24 VDC User-Supplied Power Supply
Customer-Supplied Power Supply
24 VDC (± 10%), 150 W (6 A)
(21.6 V < V
in
< 26.4 V)
Circuit Protection
1
Output must be less than 300 W peak
or
8 Amp in-line fuse
Power Cabling
1.5 – 1.85 mm² (16-14 AWG)
Shield Termination
Cable shield connected to frame ground
on power supply and ground point on
MB-40R/eMB-40R, as shown in Figure 3-2.
1
User-supplied 24 VDC power supply must incorporate overload protection to limit
peak power to less than 300 W, or 8 A in-line fuse protection must be added to the 24
V power source.
Adept Cobra s350 User's Guide, Rev. D
Page 26 of 94