Voltage out – Lingenfelter L460260704 Lingenfelter CAN to Analog Gauge & Relay Output Module CAN2 v1.0 User Manual
Page 59
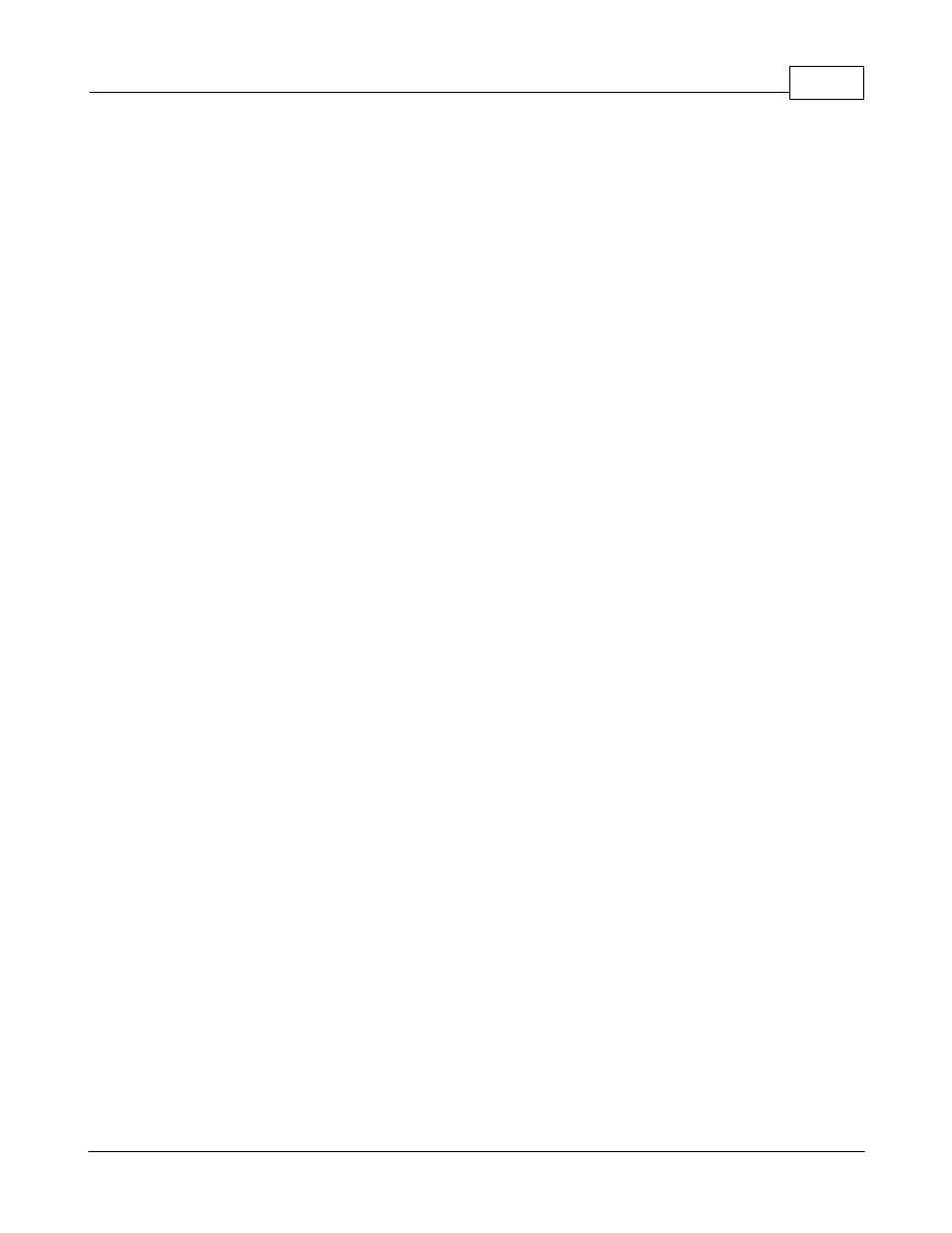
Using the software
59
© 2014 Lingenfelter Performance Engineering
In the above example the relay output would be off until the engine coolant temperature reached 180
degrees F. Once it achieved that temperature the relay output would be enabled as long as the vehicle
speed remained below 60 mph. Once the vehicle speed exceeded 60 mph the output would turn off and
would not turn back on again until the vehicle speed dropped below 55 mph. If the coolant temperature
dropped to below 175 degrees F then the output would also be disabled and would not enable again until
the temperature exceeded 180 degrees F. This example could be used to control a fan.
If you want to delay the relay output, use the "Time Delay (ms)" to provide this output delay. Keep in
mind this value is in milliseconds (1000 ms = 1 second). The Time Delay delays both the activation and
the deactivation (the On and the Off).
Be VERY careful on the "Output Type" settings in Relay Control. You can switch the logic from Normally
Off to Normally On by
4.3.2.4
Voltage Out
The Voltage Out Function is used to transmit vehicle CAN data to other modules or data acquisition
systems. The voltage out pulse width modulates the internal 5 volt reference signal from the CAN2-002
to simulate a variable 0 to 5 Vdc signal to these external modules.
This function can be used to send ECM data to an engine dynamometer data acquisition system, an in
vehicle data acquisition system or to other modules such as stand-alone transmission controllers, boost
controllers or nitrous controllers that are not able to read the CAN data directly.
Internal DIP switch on the CAN2-002 module must be set to Internal for the Output channel you are
using when you want this Function.
The Output Type must be set to Voltage On/Ground Off.
When you configure the outputs in this mode you are providing two output points for a linear output.
These two points should be the high and the low for your expected output.These values MUST be the
minimum and maximum values you want to output. The CAN2-002 module will not output data outside
the minimum and maximum values calibrated in these locations.
Min Duty Cycle provides the voltage output for the lowest point. 0 duty cycle is roughly 0 volts (you will
need to confirm this with your controller or data acquisition system).
Max Duty Cycle provides the voltage output for the highest point. 100% duty cycle is roughly 5 volts
(again you should confirm this with your controller or data acquisition system).
In most cases you will want to configure the outputs using formatted CAN data so enable that check box
in order to see formatted CAN data.
In the example below the 0 duty cycle value has been programmed to indicate 0 degrees F for ECT and
100% duty cycle has been set to 300 degrees F coolant temperature.
You will also notice that Primary and Secondary CAN data have been set to two different sources for
ECT. This makes the signal more likely to work on several different vehicle applications without requiring
configuration changes.
The frequency setting should default to 200 Hz. For most systems this should be the correct frequency.
Make sure your data acquisition system sampling rate is significantly less than this value or you may
see the PWM signal. If that is the case, you can increase the frequency of the output or you can slow
the sampling rate on this channel in your data acquisition system (if your system offers that option).