Analog gauge output – Lingenfelter L460260704 Lingenfelter CAN to Analog Gauge & Relay Output Module CAN2 v1.0 User Manual
Page 55
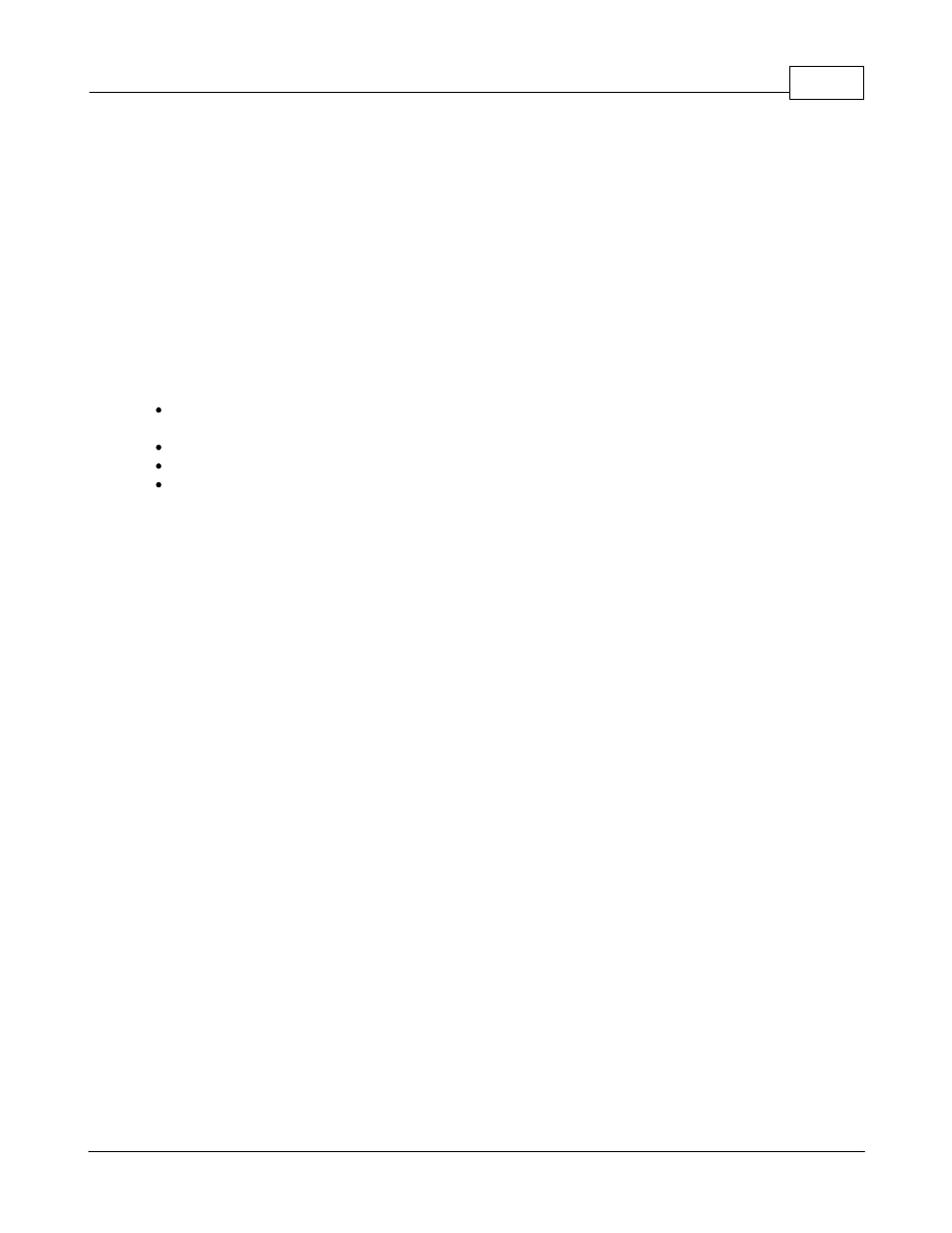
Using the software
55
© 2014 Lingenfelter Performance Engineering
When you want to use two CAN variables to control the relay status you will need to click on the check
box next to "Use primary and secondary data". This enables the Secondary CAN data in the lower
section of the window (and in the upper input related section as well).
When you are using two CAN variables to control the relay output status, you can set the logic so that
both of the values must be true (AND) or that either one can be true (Or) to enable the relay function.
Voltage Out is used to send the signal to an external device like an engine dynamometer data
acquisition system, an in vehicle data acquisition system, a nitrous or boost controller or other similar
device.
4.3.2.1
Analog Gauge Output
To calibrate the analog gauge output you will need to make sure the following items have been taken
care of:
Installation and wiring of the CAN2-002 module including power, ground, CAN hi/low and gauge output
wires.
Make sure the DIP switch on the module for this output on the correct setting (External reference).
Have the the PC powered up with the CAN2 software running and connected to the CAN2-002 module.
Determine the type of gauge you are calibrating and confirm it is an analog output type gauge.
If your gauge type already exists in the Gauge Presets drop down menu then you can skip the gauge
calibration process unless you find you need to fine tune the calibration to get the readings to display
correctly or to compensate for voltage variation.
Once you have confirmed the above items, you can now begin to create a calibration for your new gauge:
1. Under Gauge Presets select "Custom"
2. Under Function select "Analog Gauge"
3. Under Output Settings
a. Type a name for the output type in the "Output Name" field.
b. Enter a value in the Frequency field.
i. We recommend 200 Hz as a starting point.
ii. NOTE - if you change the frequency, the duty cycle value will change and you will need
to re-enter the duty cycle values.
c. Make sure "Show formatted CAN data" is selected.
4. Set the Output Type to the correct type for your gauge
a. As indicated earlier, for single wire resistance type senders the Output Type should be "Ground"
On and "Open" Off.
b. For 3 wire sensors, like those used in the Autometer pressure gauges, the Output Type should be
"Batt. V" On and "Ground" Off.
5. You should have a 3D table on the screen with Battery Voltage on the left as the vertical axis and
formatted CAN data across the top as the horizontal axis.
6. Set the top horizontal axis break points (in formatted CAN data) to be the same as the break points
on the gauge (0, 10, 20, 30 etc.)
a. If there are extra columns you can make the first and last columns the same as the ends of the
gauge travel
b. For now we will enter the same values for all battery voltages (all values in a column will be the
same).
i. Later on you can go back and adjust these values versus battery voltage if you find that battery
voltage impacts your gauge.
7. Click on the "Start/Stop Calibrate Gauge" button in the bottom right corner of the software window.
a. When the button reads "Stop Calibrate Gauge" that indicates you are currently calibrating and the
up and down arrows on the right should be darker in color (indicating they are active). The
numerical value in the box to the right of the button will also become darker in color to indicate the