Lingenfelter L460260704 Lingenfelter CAN to Analog Gauge & Relay Output Module CAN2 v1.0 User Manual
Page 51
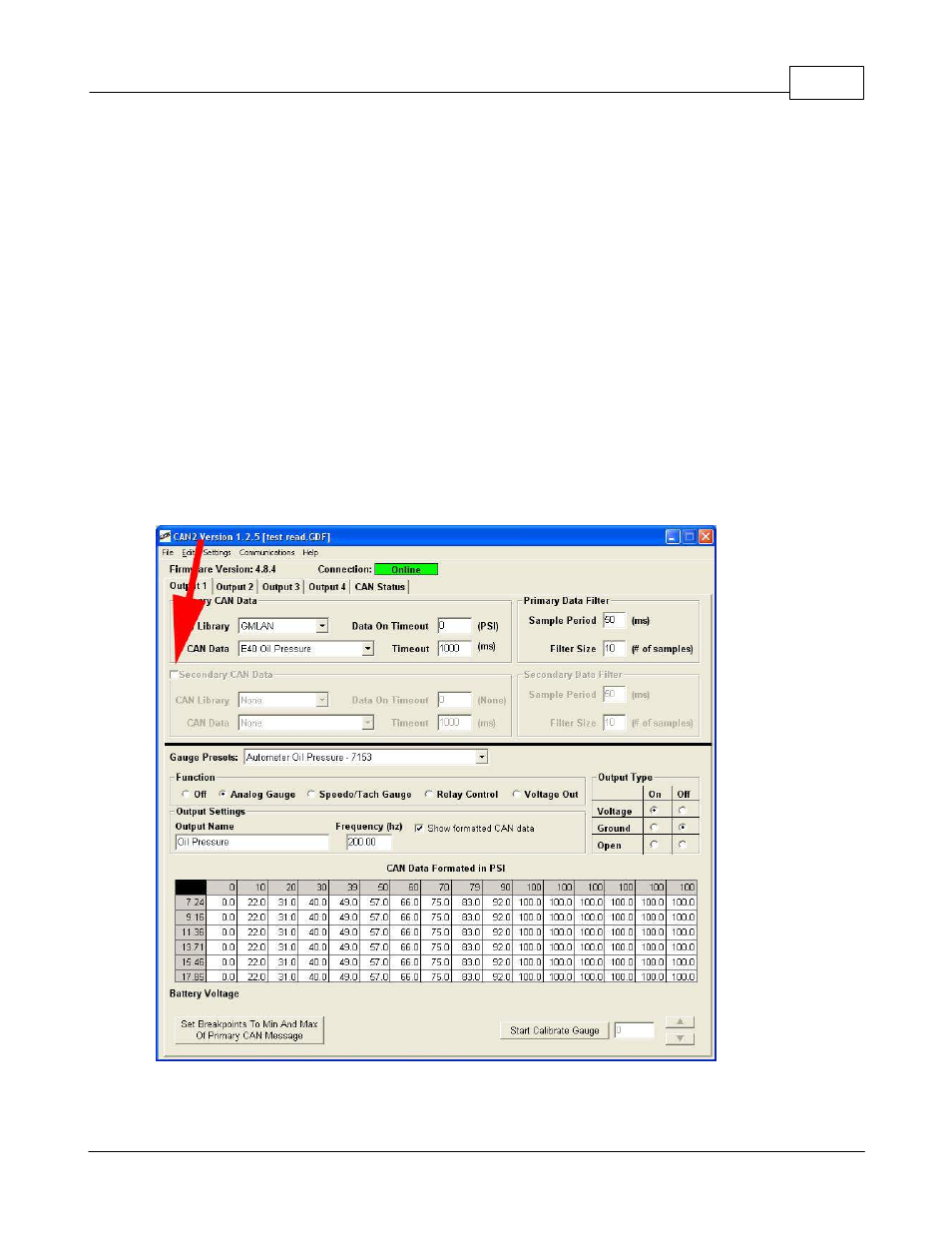
Using the software
51
© 2014 Lingenfelter Performance Engineering
slow to respond to sudden changes. If you have 10 for a filter and 50 ms for as sample period then the
CAN2-002 module will be take the average of 10 samples, 50 ms apart each and then report a new value
so the output will be updated every 500 ms (half a second) since 50 ms X 10 = 500 ms.
The CAN2-002 module allows you to assign a secondary CAN variable to each output in case the
primary output does not exist on that vehicle type or for some other reason the primary variable may not
always exist. When the Secondary CAN Data is selected, if a timeout occurs on primary data (it
reaches your "Timeout" value without receiving data for that variable) then, instead of transmitting the
"Data On Timeout" value for the Primary CAN Data it would then look for the Secondary CAN Data value
and transmit that value if it exists. If the Secondary CAN Data times out then the Data On Timeout from
the Secondary CAN Data is used. When Secondary CAN Data is selected the Data On Timeout for the
Primary CAN Data is not used.
The primary and secondary data should be the same type of variable with the same units (both engine
coolant temperature variables, for example). You would probably not want the CAN2-002 module to
broadcast oil pressure if the coolant temperature were not being transmitted for some reason as this
could lead to confusion on your readings.
By default only the Primary CAN Data is active. If you want to enable the secondary CAN data you must
click check the box to the left of the "Secondary CAN Data" as shown by the arrow below: