Relay outputs – Lingenfelter L460260704 Lingenfelter CAN to Analog Gauge & Relay Output Module CAN2 v1.0 User Manual
Page 57
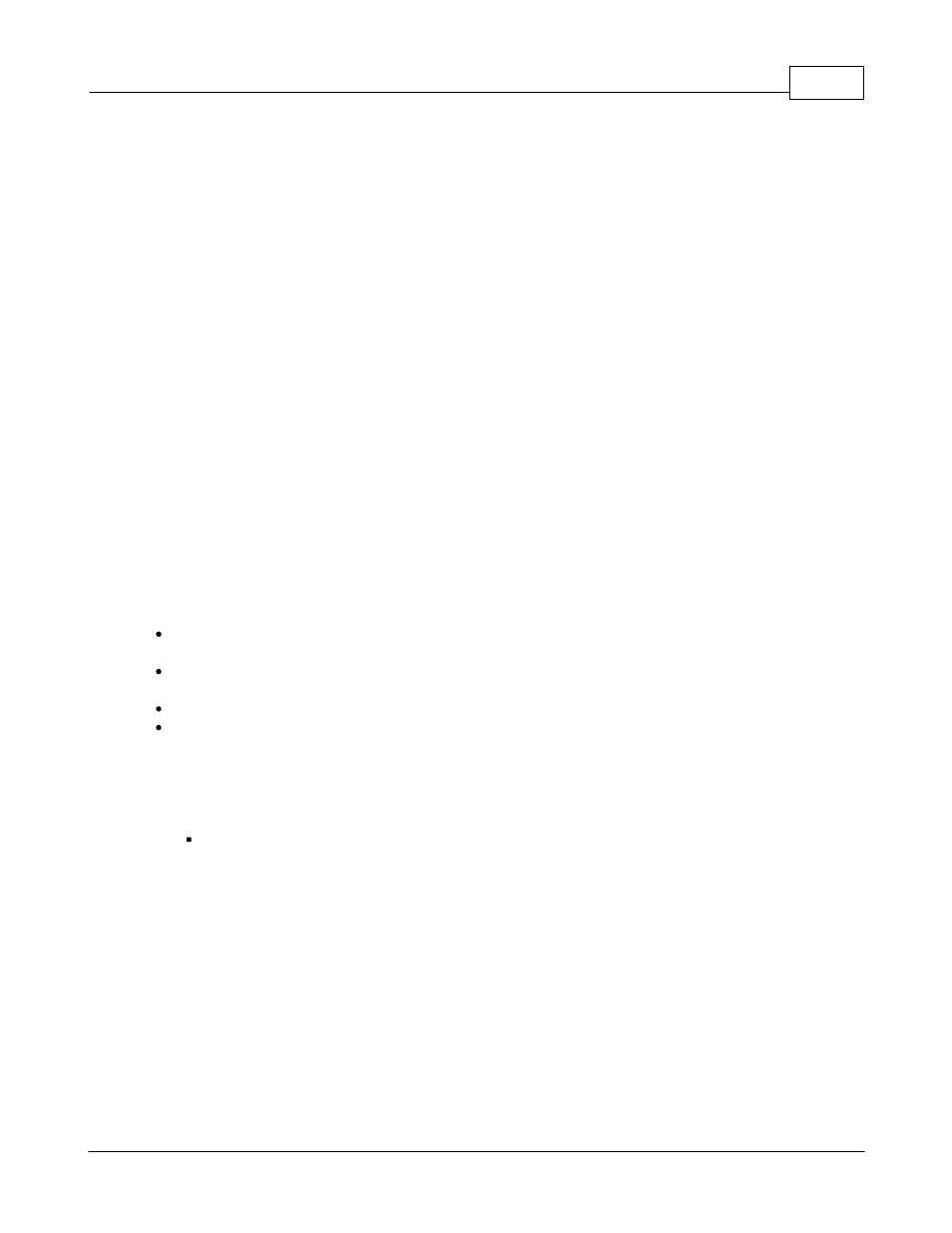
Using the software
57
© 2014 Lingenfelter Performance Engineering
a. When the button reads "Stop Calibrate Gauge" that indicates you are currently calibrating and the
up and down arrows on the right should be darker in color (indicating they are active). The
numerical value in the box to the right of the button will also become darker in color to indicate the
data is now active.
b. With the calibrate gauge mode active the signal to the gauge is now controlled by the frequency
value in the box.
c. You can either type a new value into the box or change the value up or down by clicking on the up
or down arrows.
d. If you have a point for the beginning of the gauge travel, or zero, enter zero in the first cell.
e. Move on to the next break point, increase the calibration value until the gauge reads the same as
that break point and then enter the calibration value into that cell.
f. Repeat this process until have programmed all the break points.
g. Any extra cells at the end of the gauge travel should all be the same as the last valid value.
h. Be careful to test to the maximum value because on many tachometer and speedometers the
gauge will drop to zero or the gauge reading will become erratic if you exceed the maximum
frequency the gauge will accept.
8. Click on the "Stop Calibrate Gauge" button to return to normal operation.
a. At this point the signal to the gauge will be generated from the table based on the CAN data.
b. Use a scan tool to compare the gauge readings to actual ECM data.
NOTE - in J1939 the maximum RPM is 8192. If you try to enter a higher value than this the software will
revise the value back down to 8192.
4.3.2.3
Relay Outputs
To calibrate the Relay output you will need to make sure the following items have been taken care of:
Installation and wiring of the CAN2-002 module including power, ground, CAN hi/low and relay output
wires.
If you will be using a +12 volt output relay configuration make sure the DIP switch in the module for
this output is on the correct setting (External reference).
Have the the PC powered up with the CAN2 software running and connected to the CAN2-002 module.
Determine how you want your relay control logic to operate and how it is being wired.
Once you have confirmed the above items, you can now begin to create a calibration for your new relay
output.
Example 1:
Ground side control of a relay to turn on at a desired engine coolant temperature (ECT) below a
desired vehicle speed.
1. Make sure the CAN Data output settings are configured correctly (for the Primary and, if applicable,
the Secondary CAN Data)
a. For a relay to be controlled by two variables the Secondary CAN data will need to be populated. For
this example:
i. Coolant Temperature should be selected for your Primary CAN data
ii. Vehicle Speed should be selected as your Secondary CAN data
2. Under Gauge Presets select "Custom"
3. Under Function select "Relay Control"
4. Under Output Settings
a. Type a name for the output type in the "Output Name" field.
b. Enter a value in the Time Delay field.
i. For this example we will set it at 0 ms.
c. Make sure "Show formatted CAN data" is selected.