Speedo & tach gauge – Lingenfelter L460260704 Lingenfelter CAN to Analog Gauge & Relay Output Module CAN2 v1.0 User Manual
Page 56
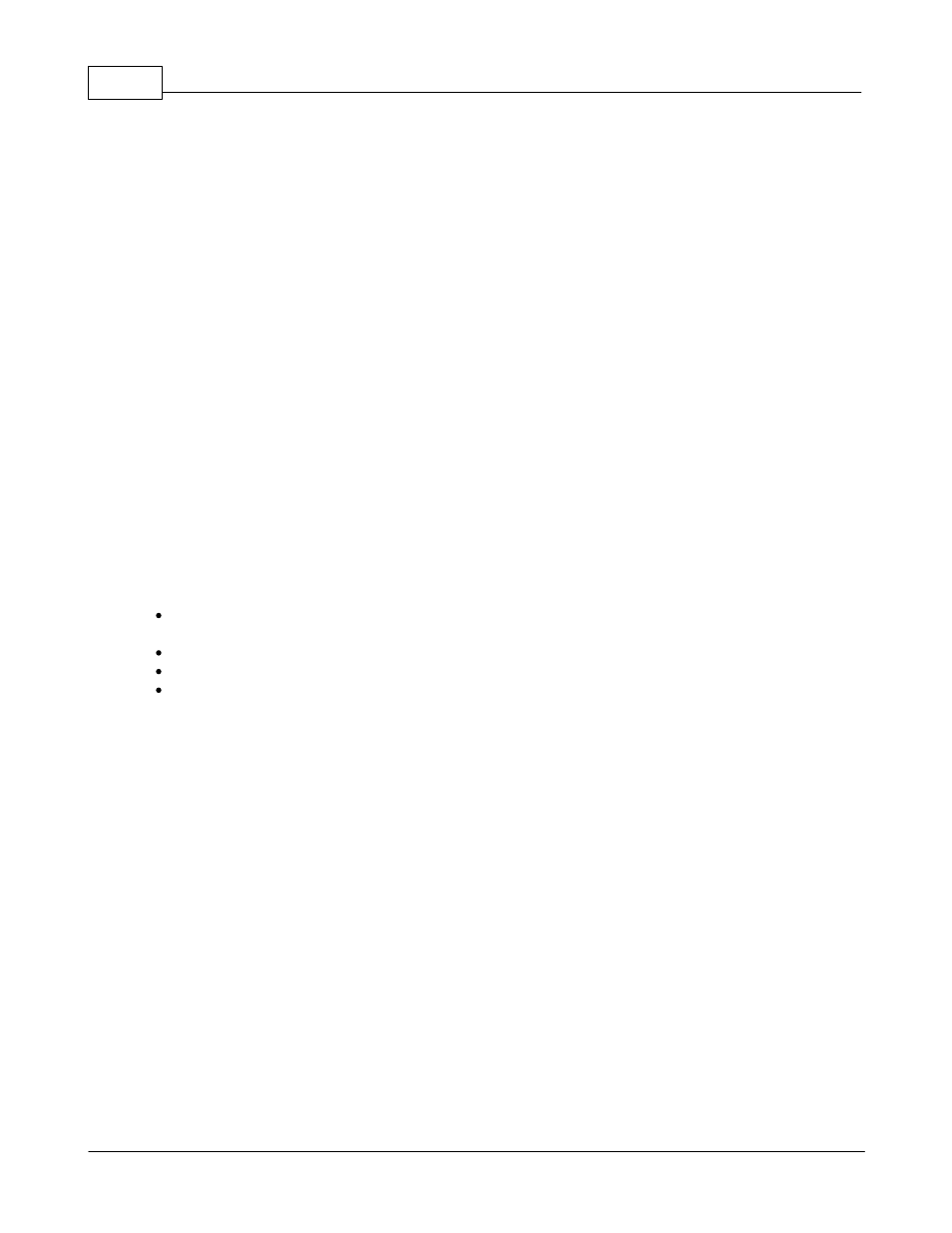
CAN2-002 Install & Operating Instructions
56
© 2014 Lingenfelter Performance Engineering
data is now active.
b. When the button reads "Start Calibrate Gauge" that indicates you are not currently calibrating the
gauge and the output adjustment up and down arrows should be gray along with the data value in
the box.
c. With the calibrate gauge mode active the signal to the gauge is now controlled by this duty cycle
value.
d. You can either type a new value into the box or change the value up or down by clicking on the up
or down arrows.
e. If you enter zero your signal will be zero. If you enter 100 the signal will be what ever the full
reference voltage is.
f. If you have a column for the beginning of the gauge travel, or zero, enter zero in the first column.
g. Starting at 0 increase this value until the gauge reads the same as your next break point. Now
enter the duty cycle into that column.
h. Move to the next break point, increase the duty cycle value until the gauge reads the same as that
break point and then enter that value into that column.
i. Repeat this process until you have programmed all of the break points.
j. Any extra columns at the end of the gauge travel should be set to the same as the last valid value.
8. Click on the "Stop Calibrate Gauge" button to return to normal operation.
a. At this point the signal will be generated from the table based on the CAN data.
b. Use a scan tool to compare the gauge readings to actual ECM data.
4.3.2.2
Speedo & Tach Gauge
To calibrate the Speedometer or Tachometer output you will need to make sure the following items have
been taken care of:
Installation and wiring of the CAN2-002 module including power, ground, CAN hi/low and gauge output
wires.
Make sure the DIP switch on the module for this output on the correct setting (External reference).
Have the the PC powered up with the CAN2 software running and connected to the CAN2-002 module.
Determine the type of gauge you are calibrating and confirm it is a frequency input type tachometer or
speedometer gauge.
If your gauge type already exists in the Gauge Presets drop down menu then you can skip the gauge
calibration process unless you find you need to fine tune the calibration to get the readings to display
correctly on your gauge.
Once you have confirmed the above items, you can now begin to create a calibration for your new gauge:
1. Under Gauge Presets select "Custom"
2. Under Function select "Speedo/Tach Gauge"
3. Under Output Settings
a. Type a name for the output type in the "Output Name" field.
b. Enter a value in the Duty Cycle field.
c. We recommend 50% Duty Cycle as a starting point.
d. Make sure "Show formatted CAN data" is selected.
4. Set the Output Type to the correct type for your gauge
a. As indicated earlier, for a tachometer or speedometer type gauge the Output Type should be "Batt.
V" On and "Ground" Off.
5. You should have a 2D table on the screen with "CAN Data Formatted In RPM" across the top.
6. Set the top row break points of formatted CAN data to be the same as the gauge break points (0,
1000, 2000, 3000, 4000, etc.).
a. If there are extra cells at the end of the table you should make them the the same as the end of the
gauge travel.
7. Click on the "Start Calibrate Gauge" button.