Chapter 1 – introduction – Emerson Process Management Bristol ControlWave ExpressPAC User Manual
Page 7
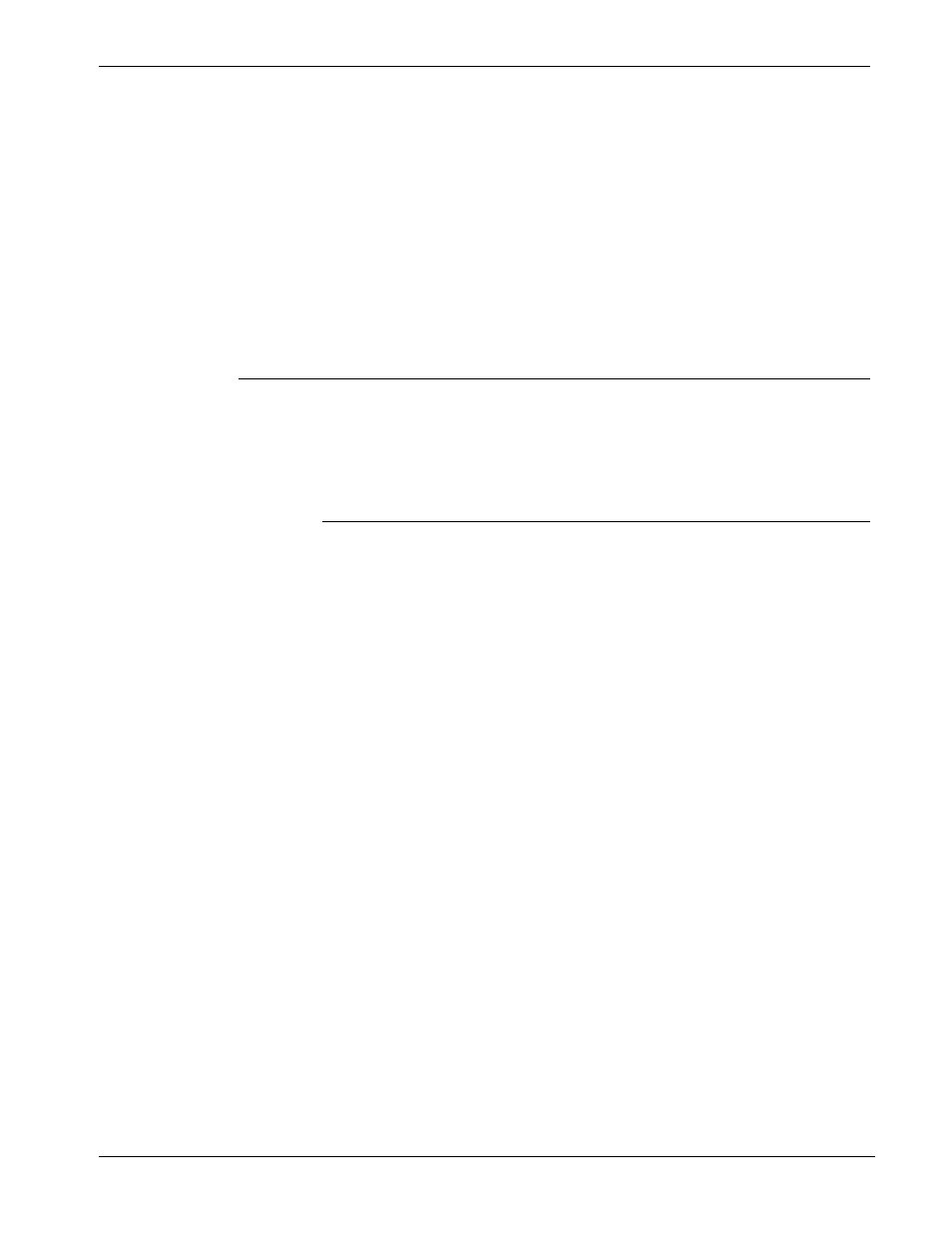
ControlWave ExpressPAC Instruction Manual (CI-ControlWave EPAC)
Revised Mar-2011
Introduction
1-1
Chapter 1 – Introduction
This manual focuses on the hardware aspects of the ControlWave
ExpressPAC Process Automation Controller/Remote Terminal Unit
(RTU). For information about the software used with the ControlWave
ExpressPAC, refer to Getting Started with ControlWave Designer
(D5085), the ControlWave Designer Programmer’s Handbook (D5125),
and the online help in ControlWave Designer.
This chapter provides an overview of the ControlWave ExpressPAC and
its components and details the structure of this manual
In This Chapter
Scope of the Manual........................................................................1-2
Physical Description ........................................................................1-2
CPU/System Controller Board .........................................................1-4
Power Options .................................................................................1-6
Software Tools .................................................................................1-7
ControlWave ExpressPAC is designed to perform as the ideal platform
for remote site automation, measurement, and data management in
process control and manufacturing. It can serve as a process automaticn
controller or remote terminal unit (RTU). Typical process inputs used
by the ControlWave ExpressPAC are pressure, flow, level, temperature
and frequency input [typically used for positive displacement (PD)],
turbine, or ultrasonic meters. In some cases, inputs may also be derived
from external multivariable transmitters using either the BSAP or
Modbus protocols. Emerson provides the ControlWave ExpressPAC in
a NEMA 3R rated enclosure which allows operation in an un-protected
outdoor environment.
Features ControlWave ExpressPAC has the following key features:
Exceptional performance and low power consumption through use
of the ARM microprocessor
Very low power consumption to minimize costs of integrated solar
panel / battery power systems
Three CPU / System Controller board configurations (see Table 1-
1.)
Three process I/O board configurations (see Table 1-2.)
Two RS-232 and one RS-232/RS-485 asynchronous serial
communication ports
Optional 10/100 MB Ethernet port
Broad selection of modem and wireless communication options
Optional display or display/keypad