2 communicating with the controlwave expresspac, 1 default comm port settings, 2 collecting data from the controlwave expresspac – Emerson Process Management Bristol ControlWave ExpressPAC User Manual
Page 64: Communicating with the controlwave expresspac -2, Default comm port settings -2, Collecting data from the controlwave expresspac -2, Default comm port settings, Collecting data from the controlwave expresspac
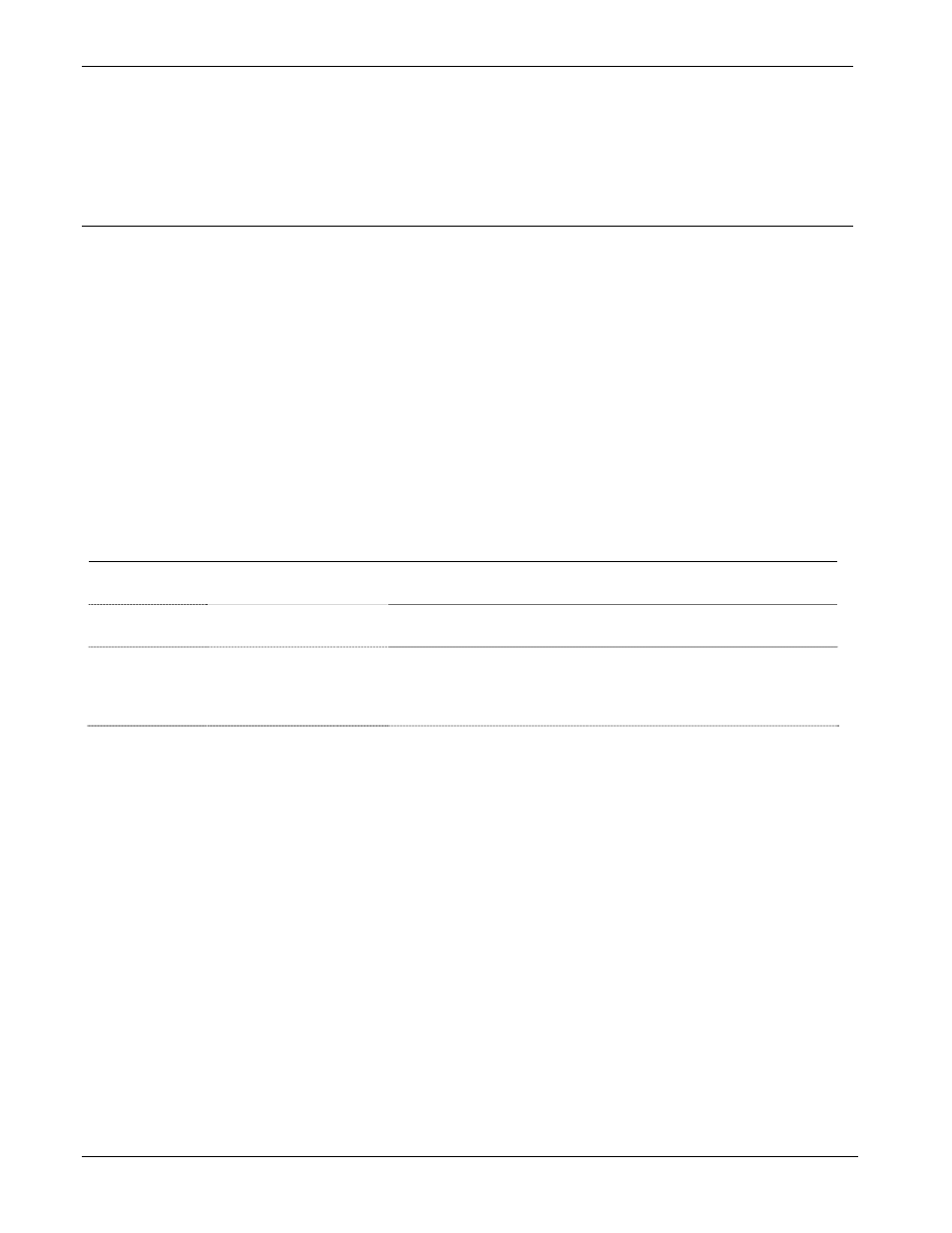
ControlWave ExpressPAC Instruction Manual (CI-ControlWave EPAC)
4-2 Operation
Revised
Mar-2011
Power
Down
To remove power from the ControlWave ExpressPAC, unplug
connectors TB1 and TB2 from the CPU/System Controller board.
4.2 Communicating with the ControlWave ExpressPAC
You communicate to the ControlWave ExpressPAC by connecting a
cable between a port on your PC workstation and one of the
ControlWave ExpressPAC ports.
The port at the PC workstation must match the configuration of the
ControlWave ExpressPAC port.
4.2.1 Default Comm Port Settings
As delivered from the factory, ControlWave ExpressPAC
communication ports have default settings. Table 4-1 details these
defaults.
Table 4-1. Default Comm Port Settings (by PCB)
Port
PCB
Default Configuration
COM1
CPU
RS-232; 115.2 Kbps using BSAP or ControlWave Designer
protocol.
COM2
CPU
RS-232; 9600 baud, 8 bits, no parity, 1 stop bit, BSAP or
ControlWave Designer protocol
COM3
CPU
RS-485; 9600 baud, 8 bits, no parity, 1 stop bit, BSAP or
ControlWave Designer protocol. Intended for use with Bristol
3808 transmitters. You use jumpers W12 through W16 to
configure COM3 for either RS-232 or RS-485
Note
: You can re-enable the factory comm settings at any time by
setting switch 3 on the CPU module’s SW3 to “OFF.”
Ethernet
Using an optional Ethernet port (located on the CPU module), you can
connect either directly or through a network to a PC equipped with an
Ethernet port. The default IP address and mask for the Ethernet port is:
ETH1 IP Address: 10.0.1.1 IP Mask: 255.255.255.
4.2.2 Collecting Data from the ControlWave ExpressPAC
OpenBSI utilities such as DataView, Data Array Save/Restore and
Harvester allow you to collect real time data (values of variables, array
values, alarm messages) and historical data (audit records, archive files)
from the ControlWave. See the OpenBSI Utilities Manual (D5081) for
details. SCADA software such as OpenEnterprise can then present this
data to an operator in the form of graphical displays and reports.